The search for alternatives to petrochemical-based dyes led Loreto from the hills of Vietnam to working with laboratory scientists and bacteria strands in Spain. Her Re-FREAM co-creation project centered on the colorization of garments through biotechnology and application processes which are gentler on the environment. It envisions more sustainable fashion futures which blend cutting-edge machinery with microorganisms and embrace the beauty of natural dyes.
Loreto’s designs flourished with the help of natural ingredients, petri dishes, microbiologist in white lab coats, and the pounding drums of nebulization machines. The team worked with two strands of bacteria chromobacterium and serratia, as well as with plant dyes. Different shades – including pale violet, warm marigold and bright lime – resulted from distinct processes.
Direct dying involved growing bacteria strains directly on textiles, creating unpredictable colorscapes of loops and coils, organic color splashes in pale pastels. Dying with extracted pigments using a nebulization spin cycle provided unified color distribution – a far more scalable process. Beyond experimenting with molecules of dyes and fibers, Loreto also used the laser cutting expertise and facilities of Aitex. Fine laser detailing added ripples of movement to several of the final wrap designs.
Using natural colorants, Loreto created a fashion collection for her brand anima at the crossroads of design and technology. Nebulization for plant dyes, in particular Marigold and Mulberry, showed the best results. Bacterial direct dyeing methods remained challenging due to the high sensitivity of the Serratia bacteria strands to temperature and nutrient compositions, producing variable results. Chromobacterium bacterial pigment extraction proved more promising in terms of evenness of color distribution as well as production scale. Future research needs to address the color yield, complexity and cost of this dying process: colors results were very pale yet costly.
However, natural dyes worked exceedingly well with the Eco Finish nebulization machine. Though the process is less suited to delicate fibers such as silk, it proved ideal for cotton weaves, knits, and denim. Nebulization technology optimized the environmentally friendly dying method, enabling an environmentally friendly approach to dyeing textile fabrics.
Combining new technologies with natural dyes could replace synthetic dying processes based on petrochemicals. Synthetic textile dyes have been one of the most polluting aspects of fashion production, requiring high energy and water consumption and causing devastating levels of water pollution as well as unsafe labor conditions. They also remain in our ecosystems, as they resist spontaneous biodegradation.
As Loreto explains, some natural dyes can also impact the environment: “but working with organic waste will always be easier to solve than a petrochemical waste!”. Nebulization allows for 80% in water savings and requires up to 60% less dye, in a safe work environment. Dyeing with microorganisms and plants can save up to 500 times the amount of water used in industrialized dyeing methods, a far less toxic and more resource effective way of dyeing.
Once the challenges of cost-effectiveness and colorfastness are resolved, micro-organism fabric dyes could also potentially add bacterial functionalities to textiles and garments, such as antimicrobial properties which are highly relevant for healthcare applications.
The slow pace and the high costs of current bacteria dying methods remain a challenge. Direct dying with bacteria strains can take between two and five days, sometimes more. The bacteria are dipped in the nutrient and fed; only at the right temperature will it produce color and dye fabrics. It remains a temperamental process and requires lab space and machinery. Even more costly is the extraction of the dye from the bacteria. However, the co-creation has brought new visibility to both the topic and the designer, and has had immense immediate and tangible results.
Though Loreto would love to keep researching, she can now apply the natural plant dyes to her collection: “That’s how we’re going to start making a change, by going to market with things, by showing the customer that we can use more natural dyes.”
The Project
Loreto Binvignat experiments in using microorganisms in the dying process in combination with innovative technologies, thus creating avant-garde garments at the crossroads of design and technology.
The Partners
Loreto worked within the Sustainable Finishing Hub of Re-FREAM. She collaborated with Aitex and Care applications to research new methods in textile dyeing.
Alicia Romero, Aitex, about the project
“Loreto is a visionary in terms of new dyeing approaches. She is an environmentally conscious designer and has the ability to adapt to the situation, willing to learn microbiology techniques in the lab as necessary, in order to pursue her objective.
Having a project like Loreto’s opened a door for researching bacteria dye at the Aitex facilities. Our wide experience in microbiology together with the inspirational ideas of Loreto has prompted us to begin research in this new interdisciplinary field.”
The Technologies
The co-creation team worked with two strands of bacteria, chromobacterium and serratia, as well as with plant dyes. Only biodegradable textiles were used: organic cotton, silk and a silk hemp mix. Direct dying involved applying live bacteria directly to textile in the lab and letting them feed and grow to produce unique pigments as well as organic patterns.
Results included T-Shirts tinted with Serratia Marcens and a vest direct dyed with Chromobacterium Violaceum. Pigment extraction proved the more scalable method for urban manufacturing. Using Eco Finishing Nebulization Technology, the team dyed one jacket with Violacein extract coming from Janthino bacterium lividum (with extracts purchased from the Vienna Textile Lab), as well as several garments with Marigold, Mulberry and Logwood (plant dyes).
Dyeing with microorganisms can save up to 500 times the amount of water used in industrialized dyeing methods. Selected garments were finished with organically shaped laser cut patterns.
The Artist
Loreto is an international artist, designer and author. She has worked in the academic field, working for 10 years at IED Barcelona, within the fashion department affiliated to Westminster University London. She also worked for five years as a professor in design and fashion at the London College for design and fashion Hanoi. Her background is in fashion design and art. For the last 10 years she has been developing her multidisciplinary ethical and sustainable practice. This practice intersects in her brand: anima. by loreto.
Understanding the textile dye industries huge pollution problem she began to experiment with sustainable dyes. This research led her to create bonds, collaborate with and learn from ethnic communities around the globe, in particular the Hmong community in the mountains of Sapa Vietnam. After all these years of working with traditional dyeing techniques it was only natural to go a step further and take the leap into innovative, sustainable dyes.
Throughout the last year she has been working with the Vienna Textile Lab, researching and experimenting with bacteria dyes. Through this partnership they became one of the Worth Partnership Project 3rd call winners. This incredible experience positioned her at the intersection of art, science and technology.
Follow Loreto
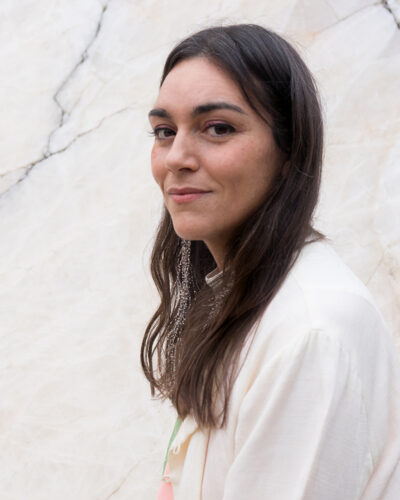