Marinero – 9
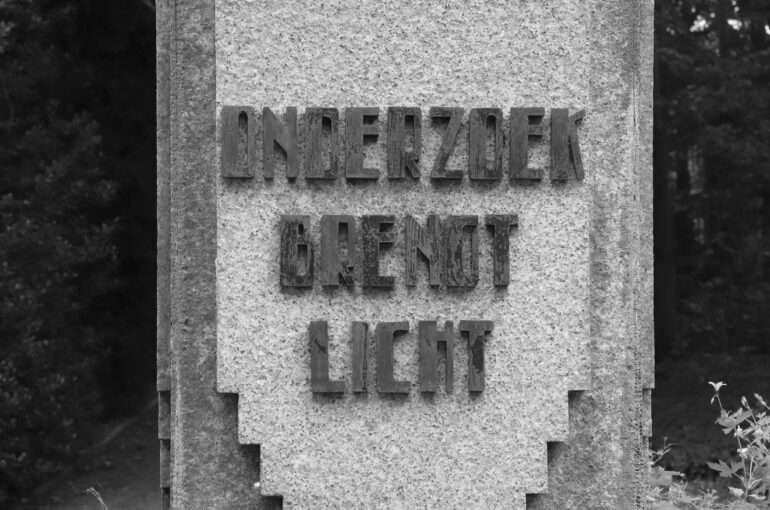
Dear reader, this is my 9th and last Re-FREAM blog. ”Onderzoek brengt licht, meaning research brings light” The Marinero journey for project Re-FREAM comes to its final stage. 2020/21 has been an interesting year and I want to thank you for following this journey with me. I learned that creativity never stops, it’s always an ongoing process, even more important during difficult times. Losing a loved one has been a very painful experience for me personally during this worldwide pandemic. Thankfully I can find some positive balance and distraction throughout my work.
I am currently starting an upcoming new project ”Adaptive Archi-Filament”. Together with my tech partner WK+ at the Johannes Kepler University in Linz we will continue to work on the next steps for new filament developments. There is more to research in terms of new Archi-Filament technology. Next to that I will also work on the commercial development of the textured monofilament, developed with WK+ during project Re-FREAM. I will first need to find a monofilament supplier that is able to develop the textured filament. In 2022 I will showcase the filament prototype available for order at the Frankfurt TechTextilMesse.
Developing a commercial product is an interesting new step for me, because it opens a wider perspective on who will eventually use the textured monofilament. My initial target group are textiles designers and other creatives that work for example at TextielLab Tilburg. The TechTextilMesse Frankfurt will be an interesting platform to see what kind of new buyers I might attract. I love the unexpected things in life, so I might get surprised to see how all of this will unravel in the future.
If you are interested to follow this journey with me, I will upload all the upcoming steps further on the Studio Adaptive Skins website ( https://studioadaptiveskins.com/ ). Underneath you can see the final stage of the Tailored by Weather installations. For me personally the design follows material process has been a positive learning experience. I am very happy that we were able to collect such a huge amount of data. Till now we created 42 Marinero designs + 9 total time lapse camera documentations.
All Re-FREAM reference Marinero blogs can be found underneath:
https://re-fream.eu/marinero-1/
https://re-fream.eu/marinero-2/
https://re-fream.eu/marinero-3/
https://re-fream.eu/marinero-4/
https://re-fream.eu/marinero-5/
https://re-fream.eu/marinero-6/
https://re-fream.eu/marinero-7/
https://re-fream.eu/marinero-8/
–
*Installation 5 before & after effect
–
*Installation 5 overview – one by one
The 6 designs for this installation belong to the Aitex category. It has been interesting to see how these designs were developed at TextileLab Tilburg. In the end this category did not result into what I had in mind. For example: design 33 is what I had in mind, but this design only had almost 10 km of Aitex archi-filament. It was impossible to create an entire new category based on design 33, because we had a total of 70+ km, so there was not enough Aitex yarn to create what I had in mind for the entire Aitex category. What we did was to twist some other yarns from TextielLab Tilburg. At first I thought it was a good idea, but in the end there have been too many yarns added into one fabric design. The risk in this is that yarns get shifted and not woven correctly. So a lot of confusion happend and fabric restoration was needed within this category.
- Design 25: Failed production test 1. Within this twill designs most of the yarns are shifted and need to be restored by hand, meaning that yarns need to be taken out piece by piece. In terms of Aitex yarns you can see that there is some shape change, but not interesting enough for what I had in mind.
- Design 26: Failed production test 2. The satin binding shows the most interesting shape change of all 3 designs (25, 26 and 27 are related, because of yarn use). This one needs to be restored also.
- Design 27: Failed production test 3. Too many yarns, the fabric looks heavy on this rib variation. This design also needs to be adjusted by hand. This involves a lot of extra work inside my studio.
- Design 28: This soluble twill variation shows shape change in a more dramatic way. We added soluble yarns within the last 3 designs. It causes another way of friction in combination with the Aitex yarns. It is interesting, but less wearable compared to designs 25, 26 and 27. Where is the balance?
- Design 29: The change on this rib variation shows the best waist tailored effect. I like the asymmetrical sleeve design within these open and tight rib binding technique.
- Design 30: Although these last 3 designs are less wearable, I do like the texture effect of the pre-deformed textile ( left in the picture ), but the production flaws still bother me within this category. I cant adjust the last 3 designs, because the soluble yarns have manipulated most of the yarns, making it impossible to restore the flaws.
–
*Installation 5 time lapse documentation
–
*Installation 6 before & after effect
–
*Installation 6 overview – one by one
The interesting part of the test category is that we started thinking that most of these designs would turn out to be less interesting test tryouts. In some of the cases this was true, but I would say that 50/50 turned out to be pleasant surprises. As a designer and researcher it makes me happy when unexpected things happen.
- Design 31: The test design for the Seaweed category. We applied 4x 20 cm techniques in the front of the garment and 4x 20 cm techniques in the back of the garment. We picked 6 out of 8 to create the entire Seaweed category (designs 1, 2, 3, 4, 5 and 6). This test garment (31) also shows potential of an alternative design aesthetic. But in this case I don’t really like the shape change and overall shape of the design. Still a flawed test design to me.
- Design 32: This was supposed to be an alternative to design 33. What happened with the Aitex category and developing design 33 left us with no choice but to use soluble yarns and twisted TextielLab yarns. This to me just feels like a simulation of design 33. The soluble integrated yarns also make this design not so wearable. I think that if this had been done like design 33 we would have had 2 similar variations. One rib variation (32) and another satin variation (33) of this design aesthetic.
- Design 33: I would say that the perfect balance is a match on this one, in terms of a wearable second skin, adaptive material communicating with the human body and tailored effect going from 2D to 3D. Design 33 would be the best result within the entire research. It’s ironic, because at first I thought this design was a failed one during the development at TextielLab. This even motivates me more at this stage to always keep an open mind and try out alternatives from the original idea. It’s very easy to think about something that sounds like a daydream, but never reaching that level of visual effect. In this case I am happy that we went from text, to sketch board and successfully reaching the final design. Design 33 to me personally reflects an early experiment of adaptive wear to the personal user in the future. It’s an early prototype and simulation of what could become better, when further researched and improved. At this point in time we were lucky enough to create the tailored effect (flat surface towards 3D shape, using female mannequin to shape around it). This was already a highly challenging process to reach. In the future it will be interesting for me to see how the Archi-Filament stays adaptive, constantly slightly changing with the person who wears it, as well as external factors from the environment. But then again, this process needs a lot of time, patience and step by step approach.
- Design 34: This is an example of a test design turning into a better result than the entire developed category afterwards. However, the Wood K Plus category has been a success in terms of aesthetic and deforming fabric change balance. But to me personally design 34 has an interesting contrast of back to front contraction of the deforming garment. I am so excited about this surprise that I wanted to create another category, named the ”conclusion” category.
- Design 35: The test version for the mix category. I think that this design also turned out to be more interesting compared to the entire mix category. It’s about adding another binding style each 20 cm’s that shows an interesting shape contrast. It feels well balanced and wearable.
- Design 36: Another test that turned out to be stronger than the entire category. This Aitex design was developed before adding twisted (fake) Aitex yarns. We made some design mistakes after finding out that the Aitex coated yarns were almost entirely used. The production mistake afterwards made the entire category marked as failed. However, the test design is strong in shape (feels a bit too heavy still for my taste) and also wearable, but not as strong as the Aitex design 33.
–
*Installation 6 time lapse documentation
–
*Conclusion category TextielLab development
After analyzing the 36 garments it was clear that design 33 was the best one, but I had the idea of choosing a few of the other remaining best results and start an additional experiment named the conclusion category. The idea behind is was to create improved versions of designs 2 and 34. Each of them would get 3 variations, to see the difference between detailed style alternatives. I send this idea to TextielLab Tilburg and Judith already had a good idea how to approach these improved variations.
At first I needed to send an overview to Judith with images and ideas on how to improve these designs. This way we could prepare ourselves beforehand. The best part of this ambitious plan was that Jaime from Aitex and Jurgen from WK+ were willing to produce additional filament production. This made me super happy, because all the yarns produced before were almost finished. The Aitex version of the archi-filament is great to create tension in the fabric, that creates the new shape. The WK+ version adds the interesting texture on top of the deforming yarns, which create an interesting contrast woven together within a gradient.
The three variations from design 2 create the waist effect that I initially really wanted to reach. The balance here lies within the twill technique versus the Aitex archi-filament. These 2 work very well woven together and deformed result afterwards. The gradient of this design begins with the textured monofilament of WK+ and fades out towards the Aitex yarns within the center of the woven material.
The three variations from design 34 are merged materials from designs 19, 20, 21, 22, 23 and 24. We used the front parts of the garment from designs 22 + 23 + 24, with the back parts of the garment from designs 19 + 20 + 21. These different styles together, with front parts merged with other backsides, cause an intricate deforming contraction from front to back. This is an interesting design aesthetic outcome, because it’s so different from what I had thought about beforehand. This is where the materials take over and surprise me as a designer. It’s always thrilling to me when these little accidents turn out to be something unexpected. It makes me want to explore more and more.
–
*Installation 7 before & after effect
–
*Installation 7 overview – one by one
This category was supposed to be the conclusion category. But once again more unexpected things happened. I would say that this is another failed production category, that eventually turned out to be partly successful. It’s ironic to me how situations like these shift my mind into adaptations of the original idea. The adaptation on this one was to first restore designs 25, 26 and 27. Why did I do this? Because once again the TextielLab made production mistakes, leaving me but no other choice than re-use past designs and create an entire new test category. Designs 37 + 38 + 39 are the restored previous ones and designs 40 +41 + 42 are flawed newly woven conclusion designs. The last 3 designs turned out to be super long (materials almost touching the floor) slightly mermaid tail aesthetically looking, with a very low transparent open back (late 20’s silhouette)
- Design 37: Former design 25. Restored twill material, cutting away several failed floated woven yarns, allowing the textile to breath again. The cutting by hand lasted over 3 weeks. The final design feels lighter aesthetically and also shows an interesting deforming effect. I decided to add a new experiment after thinking about my future plans. I used the tumble dryer to see what happens with the material. Next to that, design 37 shows the twill effect versus gradient yarns.
- Design 38: Designs 37, 38 and 39 were experimented using rain water and tumble dryer effect afterwards. This experiment is about simulating the wave force of the sea. I tried to simulate the effect of the sea, because I would like to bring the installation below sea level in the future. Design 38 shows the repetitive woven yarn rib effect (woven 1 after 1 repeated throughout the entire fabric)
- Design 39: This design shows the best result in terms of gradient effect versus shape change. I like the fact that this design shows an abstract and distorted waist effect. What you see here is the satin technique woven with several yarns: Seacell dyed with algae yarns, Aitex archi-filament, Rpet yarns, shrinking yarns and monofilament.
- Design 40: One of the three mermaid garments. This is a failed woven TextielLab produced conclusion category material. The final design is scheduled mid 2021, this design needs to be adjusted within the digital blueprint. The mermaid dress is woven far too long and also has the backside of the fabric flipped onto the front. I would need to sit together again with Judith to rework this design.
- Design 41: I do like the three mermaid designs aesthetically. But these designs are flawed in terms of weaving machine production. I needed to repair a lot of finishing mistakes, making the fabric strong enough again, to hold the entire construction together in one piece.
- Design 42: We produced three twill versions where the binding in each design slightly shifts within the construction of the fabric. On top of that we used yarn gradient using several yarns: WK+ archi, Seacell yarns, Aitex archi, Rpet yarns and monofilament. Design 41 is my favorite of the three mermaid designs. The deformed Aitex yarn effect shows something different in terms of shape change. The mermaid effect is created because the Aitex yarns deform around the knee area. The intention was that this effect would have been placed within the waist area. Nonetheless still an interesting design.
–
*Installation 7 time lapse documentation
–
*Overall conclusion project Re-FREAM
Project overall steps:
- yarn and filament development study
- prototype Archi-Filament concept #1 Valencia
- prototype Archi-Filament concept #2 Linz
- artisanal dyeing of natural yarns research and development
- filament and yarn quality research St. Gallen
- 36 woven textiles production
- 6 knitted textiles production
- material installation process and experiment
- data collecting and report overview open source online
In terms of project accomplished goals, I would say that we reached 100% successful status. This is mainly reached because of the commitment and dedication of all project partners involved. I am very thankful to all of the amazing people that helped me during this journey. Design 33 would be the best result in terms of the original Marinero concept design. Next to that we have found more possibilities on several levels. This excites me to keep the research and development going for the upcoming years.
The documentation of the entire project has been one of the main important topics. We would have never reached these interesting results without these years and years of research. It’s important to share experience and showcase all these steps. This journey will be presented in the exposition ”makers secrets” at the Dutch national TextielMuseum Tilburg, starting 26th of June 2021 till the 8th of May 2022.
–
*What’s next?
- Presentation: I have been thinking about showcasing the project throughout an official presentation. But after everything locked down it was interesting to learn that several showcasing platforms have been going from physical towards digital presentations. During London Fashion Week I have collaborated with Fashion Scout, to make a digital presentation for project Marinero. For this presentation I have worked with a model and used my studio rooftop as an alternative presentation platform. This was an interesting coming together of new worlds, because the installations seemed to be an appealing backdrop for the fashion design documentation. The process film and final designs can be watched in the link underneath:
- Project overview: After finishing project Marinero I have been focusing on the exposition of the TextielMuseum. This is a logic step for me because it is about showcasing the entire process of this project. It was very nice to find out that the curator from TextielMuseum Tilburg wanted to purchase the installation and best selected design results. Good news, because this way the designs will be well taken care off by the museum professionals and stored safely within the archive of the museum.
- New experiment: Looking back at project Marinero it has been all about ”an alternative and sustainable production method”. This keeps me thinking about making the next step. My idea is to go from rainwater towards seawater. The original concept of Marinero was to create the collection using the waves of the sea. These brainwaves have been still active in my mind and I would like to still do this experiment in the future. The goal is to re-use the installation and bring it below sea level. This idea has been illustrated by Erik Crins in the image underneath.
New project: Currently I am working on the next project “Adaptive Archi-Filament”. I have been lucky to receive a new national grant that will help me to further develop future goals. My partners from Linz have been very cooperative and are also looking for new grants, to have more research possibilities and therefor improved final filament outcomes. Next to that I will be also working again with Damien Semerdjian from TextielLab Tilburg, to further research techniques and develop wearable knitted Archi-FIlament prototypes.
–
For more info visit: www.studioadaptiveskins.com