Can we print and wear the intricate filtering processes of underwater coral forests? The co-creation designs of Filippo Nasssetti and Vincenzo Reale draw on marine organisms to investigate the new visual languages for additive manufacturing. New materials and technologies become a means to augment respiratory masks, fusing functionality with aesthetics. Manufacturing becomes a measure for enhancing both survival and personal expression.
Key to their approach is the concept of the mask as an interface, which mediates between the external environment and the body. They applied their extensive additive manufacturing expertise to enveloping a moving human being for the first time. Data of bodily needs provided by Empa was transformed into a swirl of coiling growths, printed with Stratasys directly unto fabric. The parameters of average facial thermal and sweat rates defined their structural distribution, informing future mask performance. Based on the 3D printed design, a computer numerical control (CNC) mold was developed with Haratech, allowing both for the creation of a 3D Model to fine-tune the use of different materials, as well as simplifying the production of multiple editions.
The resulting designs anticipate breathable filtering materials, forecasting the use of personalized and artistic medical devices. The organic shapes rest on the head like growths emerged from oceanic depths. An experimental transparent prototype added a new dimension to the masks: the translucence of both air, water, and sweat. Darker gradations of color indicate areas of higher transpiration, visually defining the comfort of wear.
Inspired by marine organisms, which combine filtering with the absorption of nutrients, Nassetti and Reale aim to transform masks from protective devices to a form of bodily enhancement. They employ additive manufacturing to allow for highly customized protection, but also aim for a cultural redefinition of prosthetic devices: by rethinking medical shields as fashion or art pieces, which manifest new artistic pandemic and post-pandemic identities. The designs document the disruption of ecological environments and climate change, showcase our relationship between artificial and natural, and propose a powerfully aesthetic solution.
As a major challenge was finding expert tailors for the mask construction, the team envisions digital paths for augmenting the knowledge of craftspeople with traditional skills to include 3D printing knowledge.
New design languages and innovative technologies for modelling and for production are central to Nassetti and Reale’s approach. According to Reale, “with the development of a more permeable, 3d printable, material, this is a project that can hit the market straight away. That missing ingredient may be available in five or ten years, perhaps sooner”. The team envisions future production via external suppliers hubs who receive the orders to print (and if needed, ship) the masks. In the meantime, the visually compelling project aims illustrate the team’s research into the new languages of identity and aesthetics generated by new materials and production processes.
Apart from limitations of existing material compositions, the most challenging aspect of wearables was combining the team’s extensive expertise in computational modelling with traditional fashion skills. “You can work with software that are state of the art, but fabric moves and changes shape ”, Nassetti explains, “so you need to work with people that have the skills to manipulate it”. Their Re-FREAM experience generated reflections on future digital training of artisans, but also opened the doors to a variety of new approaches, knowledge networks, and skills. A precious outcome they are looking forward to is the exposure and resulting feedback to their project.
The Project
In their collaboration, Filippo Nassetti & Vincenzo Reale are changing the notion of prostheses, from medical devices to customised fashion products by radically rethinking the relationship between technology in the form of wearable objects and the human body.
The Partners
Nassetti and Reale worked within the Additive Manufacturing Hub of Re-FREAM, focused on urban manufacturing. They partnered with Stratasys, Haratech and the Fashion & Technology department at the Kunstuniversität Linz , using 3D scanning and the latest 3D printing innovation. Empa provided detailed bodily data analysis.
The Technologies
In their collaboration, Filippo Nassetti & Vincenzo Reale used Polyjet 3D printing by Stratasys directly on fabric to customize medical masks. The translucent designs are adapted to average measurements of thermoregulation and sweat, enabling increased comfort.
The project pre-empts the development of breathable materials with filtering properties. Based on the 3D printed design, a computer numerical control (CNC) mold was developed with Haratech, allowing both for the creation of a 3D Model for the use of different materials, and simplifying the production of multiple editions.
The Artists
Filippo Nassetti
In 2015 Filippo joined Zaha Hadid Architects, initially as part of the Computation and Design team, then of Zaha Hadid Design. His focus there is on small scale research projects, from product design to experimental sculptures and installations.Filippo Nassetti is an architect and generative designer. His design agenda was initiated in 2012 by co-founding MHOX, a EU-funded research practice and start-up focused on the design of radical artefacts and wearable products through computational techniques and 3d printing.
Since 2016 he teaches at UCL The Bartlett School of Architecture, as part of the B-Pro Master’s Degree program, Urban Morphogenesis Lab. Filippo’s independent work has been published and exhibited internationally. He lectured at The Royal College of Arts (London), China Central Academy of Fine Arts (Beijing), Florida International University (Miami) among others and exhibited at Centre Pompidou (Paris), Design Museum (London), Bozar Centre (Bruxelles).
Follow Filippo:
Vincenzo Reale
During the last ten years Vincenzo has worked with several contemporary architectural and design practices, including Zaha Hadid Architects, Antony Gormley Studio, and Tom Wiscombe Emergent Architecture. He currently holds the position of senior structural engineer in the Specialist Technology + Research group in Arup in London.Vincenzo Reale is a chartered structural engineer (ICE) and architect (ARB). He holds a master’s degree with distinction in Structural Engineering and Architecture from the University of Bologna and a Master of Science from the Architectural Association in London.
Concurrently with his professional work he has also held several academic positions, teaching at the Architectural Association, Imperial College, Bartlett School of Architecture and Arup University. His works and collaborations have been exhibited worldwide, notably at the Venice Biennale of Architecture, Royal Academy of Arts and Design Museum in London.
Follow Vincenzo:
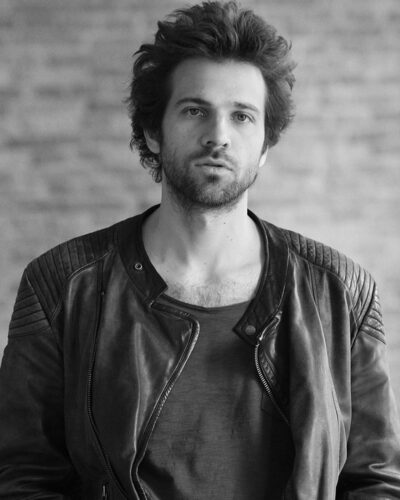
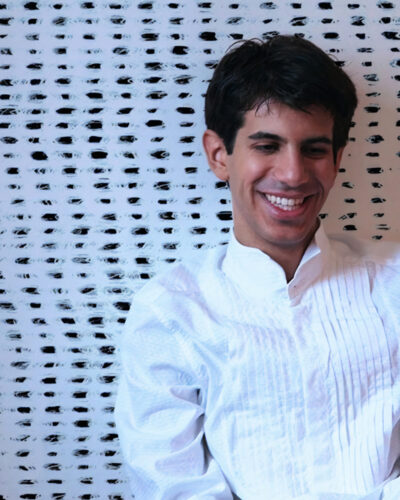