From conventional Denim to BIO-Denim
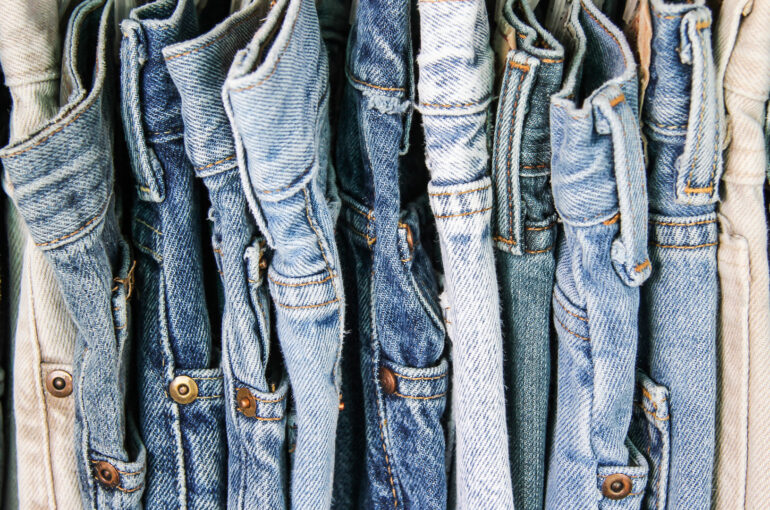
Today we use to buying products based on our own knowledge, generating in our mind an abstract idea regarding the process that has been used to achieve a particular effect or finish. But most of the time, according to what we heard, what people tell us, and the little knowledge of the textile sector leads us to buy garments whose process is much more polluting than the final product itself, for example as it happens to the animal leather.
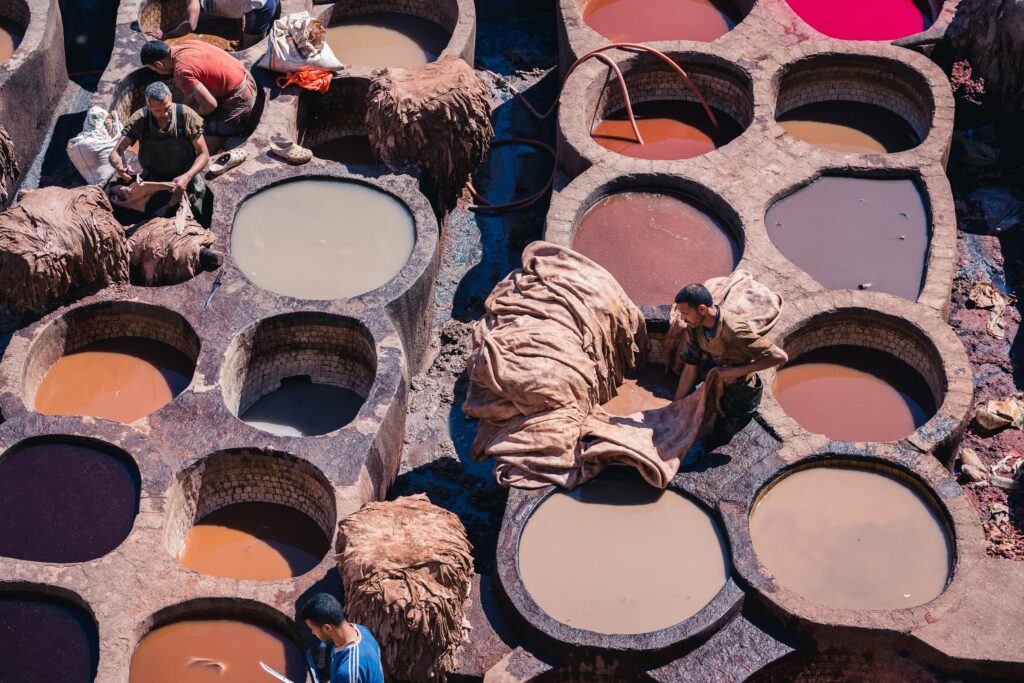
Tanning and dying process in India
During my experience with Care Application I could understand that also in the finishes sector it is “not all that glitters is gold“. This is the case of the well-known Denim/worn effect, which since the 20th century has been the basic clothing that each of us has in the wardrobe.
Thanks to the EcoFinish technology of Care Application I was able to discover the world of finishes and provide a current solution to generate a new finish by nanonebulization. BIO-Denim was born.
But let’s know more about the actual state of Denim landscape, and how, some improvements have been done to create a new eco solution to the fashion market, having a quick overview of the current process from more to less polluting ones. The finishing processes for Denim are different but basically include dyeing, washing, including special visual effects, such as stone-washing, drying, pressing, etc..
Effects such as resin whiskers, accent abrasion, and color discharge can be combined to achieve the final premium effect.
These processes also consume vast quantities of water, resulting in denim manufacturing with a high-water footprint. Incredibly, one pair of jeans, including its production and general wear uses up to 132 liters of water.
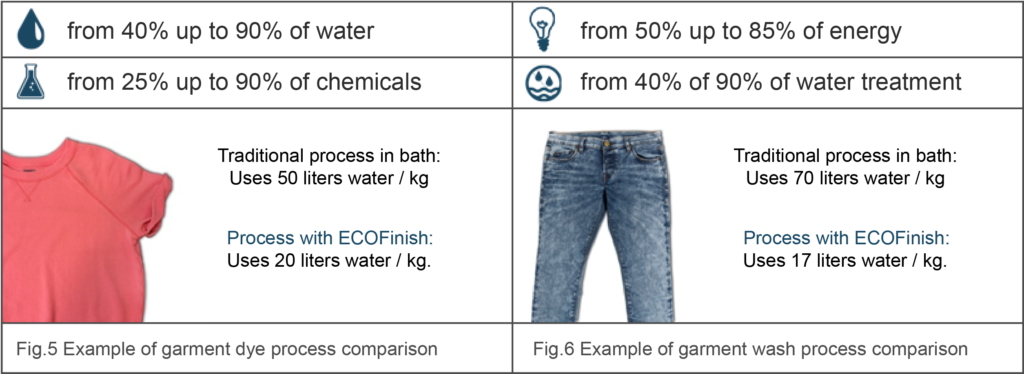
The use of chemical dyes in the production of ‘distressed’ denim is intensive. The denim is subjected to several chemical washes. Added to that, there are serious health risks to the workers through exposure to the harmful chemicals that are used to spray the material in pursuit of an ‘acid wash’. Chemical run-offs from some of these manufacturers are also dumped into the water system, turning them indigo-blue such as the Pearl River in China.
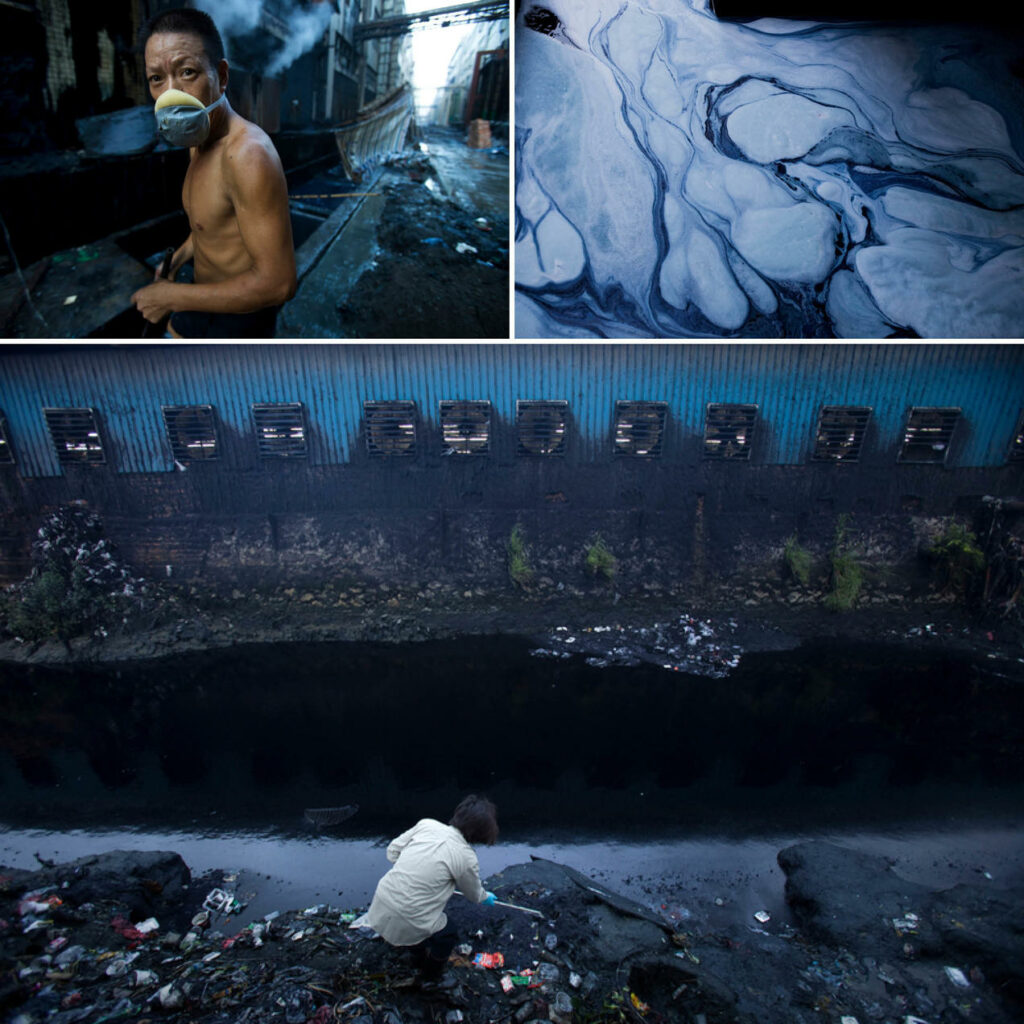
Xintang pays heavy price for putting world in blue jeans
Sandblasting is also a long-known process and it’s involves taking fine sand and channeling it into an airgun, it is then sprayed at high pressure onto denim to create a worn, old look. It’s a cheap, quick method that manipulates garments but its main ingredient, silica, is harmful to workers.
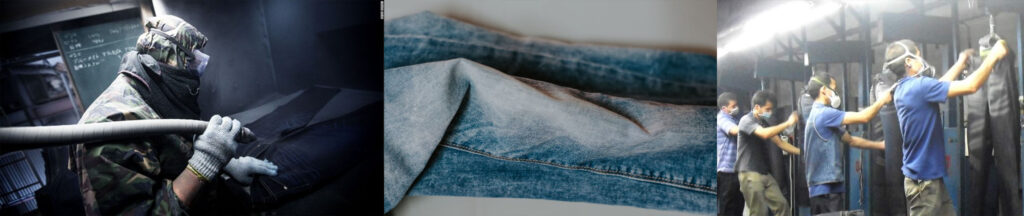
Sandblasting on Denim
Less dangerous processes is Laser and Ozone technology, Advanced Denim by Archroma, and Ecofinish technique by my partner Care Applications. The objective of our collaboration in Re-fream project is to adjust and scale up a technology to provide environmental-friendly garments and fabrics.
These materials are made from the upcycling of cork industry waste. When this cork dust, which is a very abundant residue from manufacturing bottle stoppers, is treated with Ecofinish process. The first key step is “Micronebulization”, thus we obtain a totally functional alternative to conventional finishes which is appealing and well-performing.
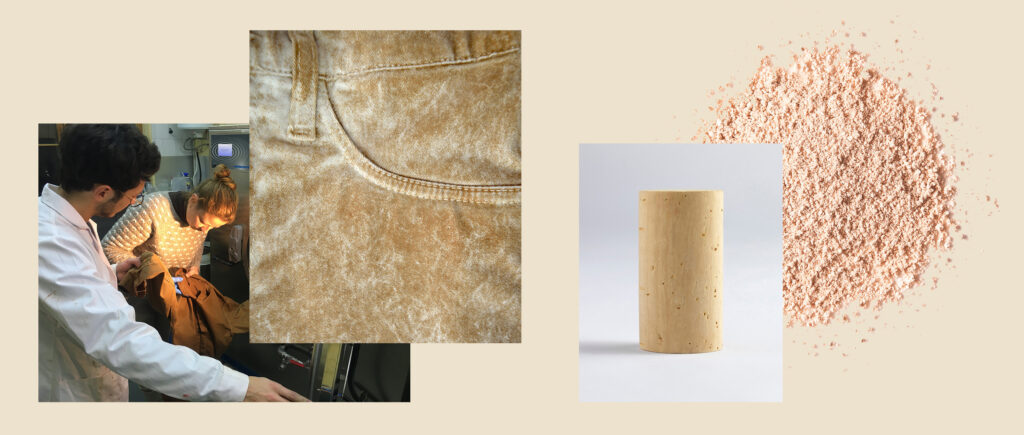
Nanocork Moodboard
The cork particles, along with other bio-based products and natural pigments, are nebulized creating a mist that envelops the garment or fabric. In this way, the particles gradually penetrate into the fibers of the support fabric (organic cotton, hemp, linen, etc.) adhering and depositing in a controlled way the amount of cork needed depending on the structure and weft of the garment/fabric. In this way, bio-denim effects are achieved with the use of only vegetable raw materials, without adding toxic products to achieve a worn effect.
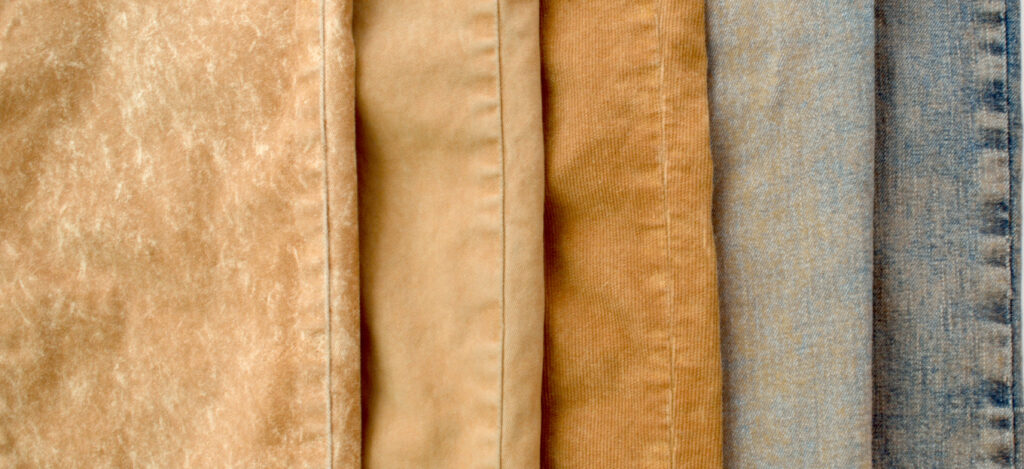
Cork finish effects
In the production process, significant savings in water and chemicals are achieved, since the fabric, wrapped in a cork mist, needs only a minimal amount of water for the particles to penetrate into the fibers, allowing savings of water that can reach up to 90%. Cork-solution is applied in a quantity that garments are able to absorb, without wastes. The process also allows significant savings in textile material, since ad-HOC garments can be made and dyes can be added and finishes directly on garments and on-demand, without having to produce more than is needed, avoiding overproduction and recycling old clothes giving them a new finish.
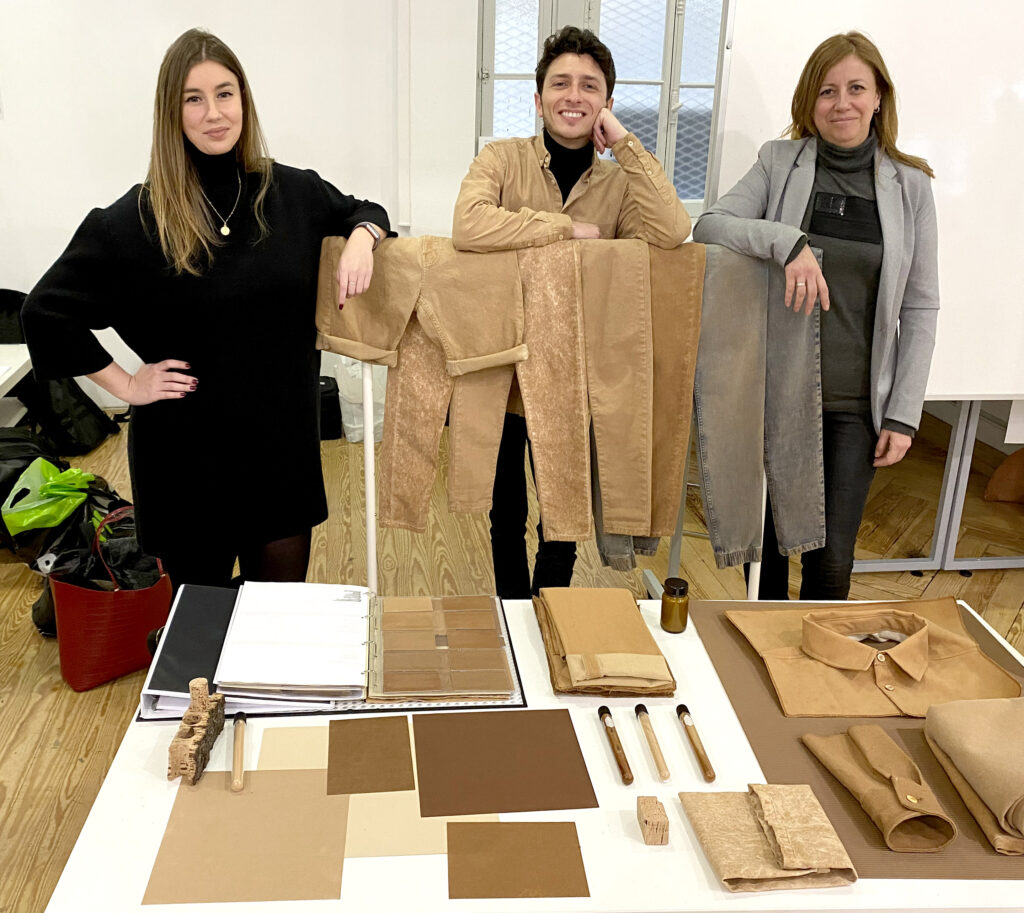
Fabio Molinas and Care Applications' team during the Mid-Term presentation.
There is no other type of equivalent process on the market, the fact of being able to apply a natural finish without full immersion in water, and with the use of the least amount of chemical products, and the low use of energy represents an innovation in the field of the textile industry, which is the second most polluting activity in the world. The fact of using natural resources, without damaging the environment, so I can assure that ART+TECH collaboration is essential to finally close the production cycle of a garment.
Bibliography
About Organic Cotton. (n.d.). WHAT YOU SHOULD KNOW ABOUT ORGANIC COTTON. http://aboutorganiccotton.org
How Denim Manufacturing Impacts the Environment
Moni Omotoso -1st June 2018 https://fashioninsiders.co/features/opinion/how-denim-manufacturing-impacts-the-environment/
Archroma: www.archroma.com
Denim Garment Finishing: Process Overview https://www.cottonworks.com/topics/sourcing-manufacturing/denim/the-art-of-denim-garment-finishing-process-overview/
Denim Garment Finishing: Finishing Machinery
https://clothingindustry.blogspot.com/2017/12/sandblasting-denim-health-problems.html