Fragments Garments #3 — Prototyping Start
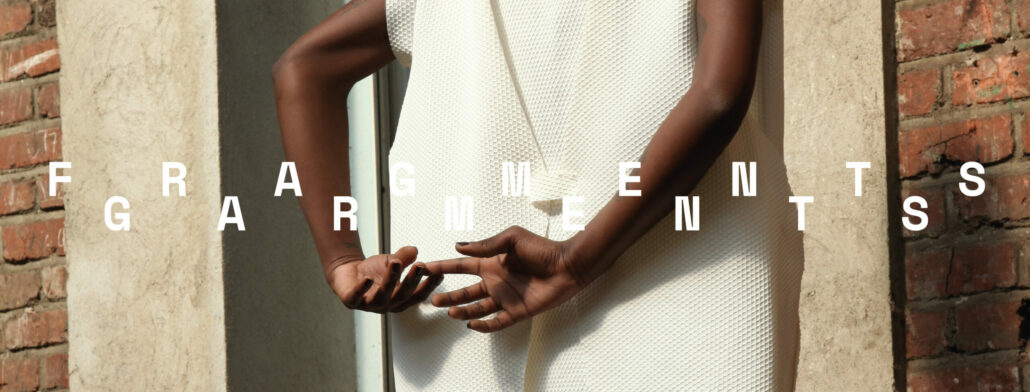
Switching from Physical to Digital Pattern Making
In order to remain coherent with the sustainable production goal, I decided to move away from classical garment 3D fabric-based shape modeling, and traditional pattern making drawn on paper or cardboard to 3D modeling in order to save material and to reduce pre-production waste. Having been previously used to working on the open-source parametric pattern making software Seamly 2D, I tried this time Clo3D which allowed me to work on flat pattern parts shapes while visualizing at the same time the result on a human avatar.
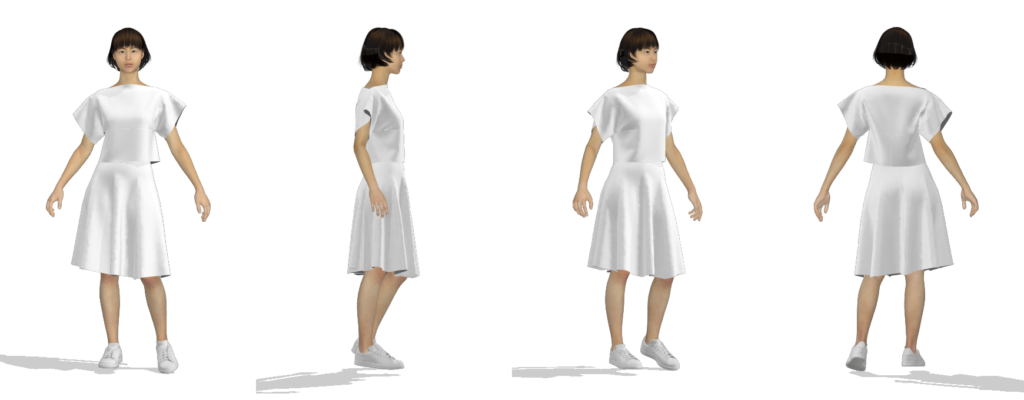
To conceive the high-waisted full skirt inspired by the 50’s New Look style, I had to work with triangular shapes, which was a new experiment with the seamless interlocking attachment system I created. This demanded a lot of computations so as to arrive at the proper skirt volume and the appropriate number of fasteners to achieve harmony and practicality.
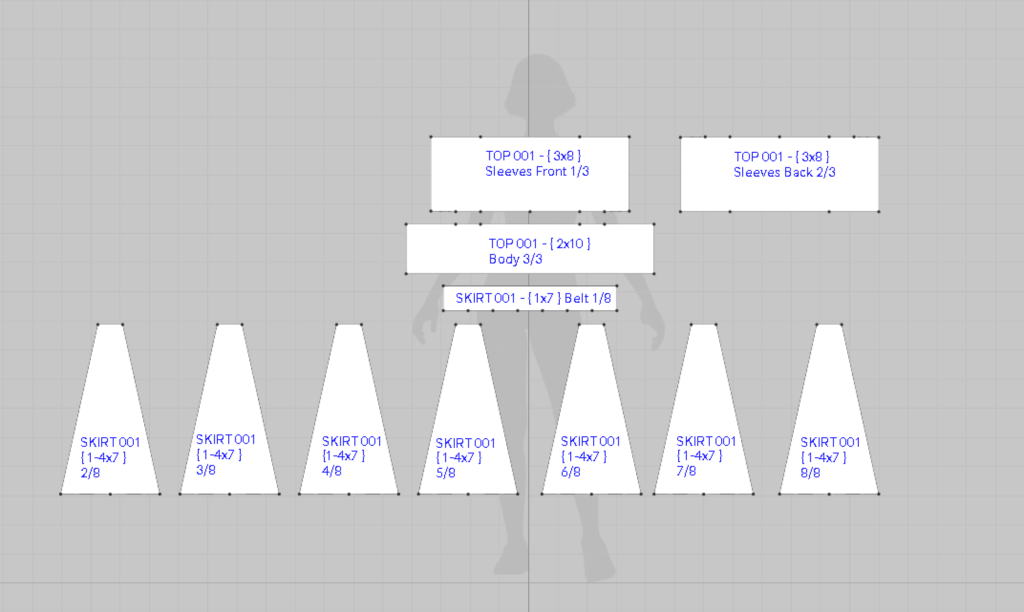
A Blank Canvas for Customization
Once the clothes patterns conception is over, starts the pre-production phase, which implies finding the proper fabrics apt at being laser-cut. I visited textile suppliers which are specialized in reselling end-of-collection rolls of high-quality fabrics used by Parisian luxury houses to limit wastage. The Re-Fream project allowing me to collaborate with the company Care Applications to experiment with on-demand textile dyeing and finishing using the micro-nebulization technique developed by Carmina, Romano, and Belen Ferri Valero, as a consequence I exclusively needed to source white or natural fabrics to work with.
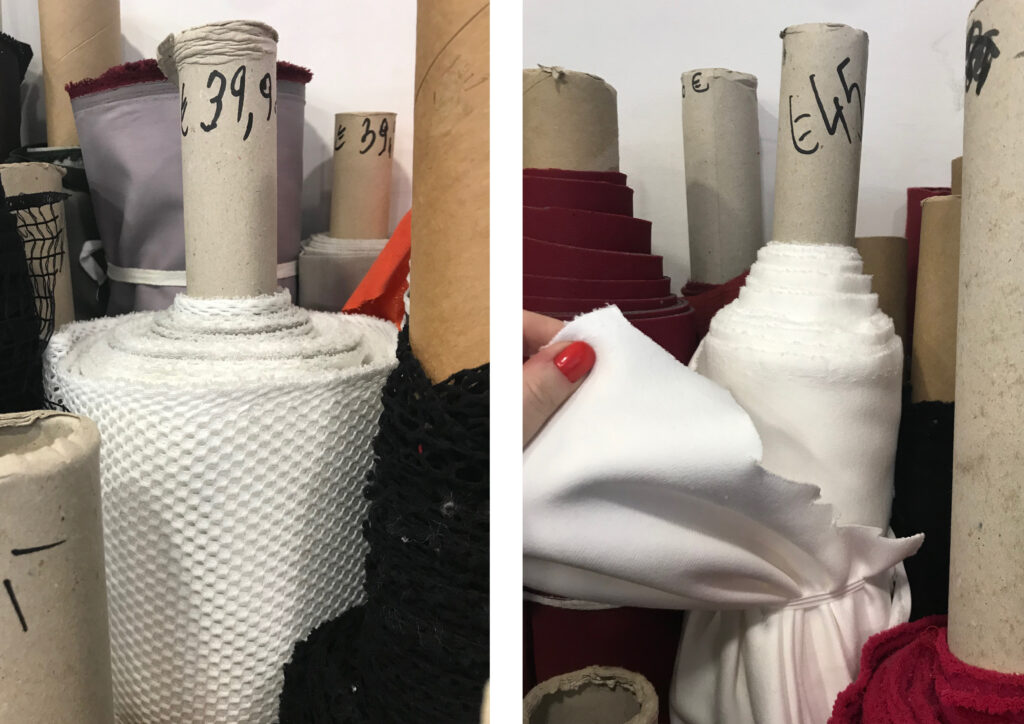
The micro-nebulization equipment follows all circular economy prescriptions; not only can it be implemented on any existing industrial washing machine to avoid costly and unsustainable machine replacement, but it is also modular to perfectly fit the factory owner requirements. This process offers both water and chemical savings and non-polluting washing, dyeing, and finishing as the micro-nebulization produces no liquid waste at all.
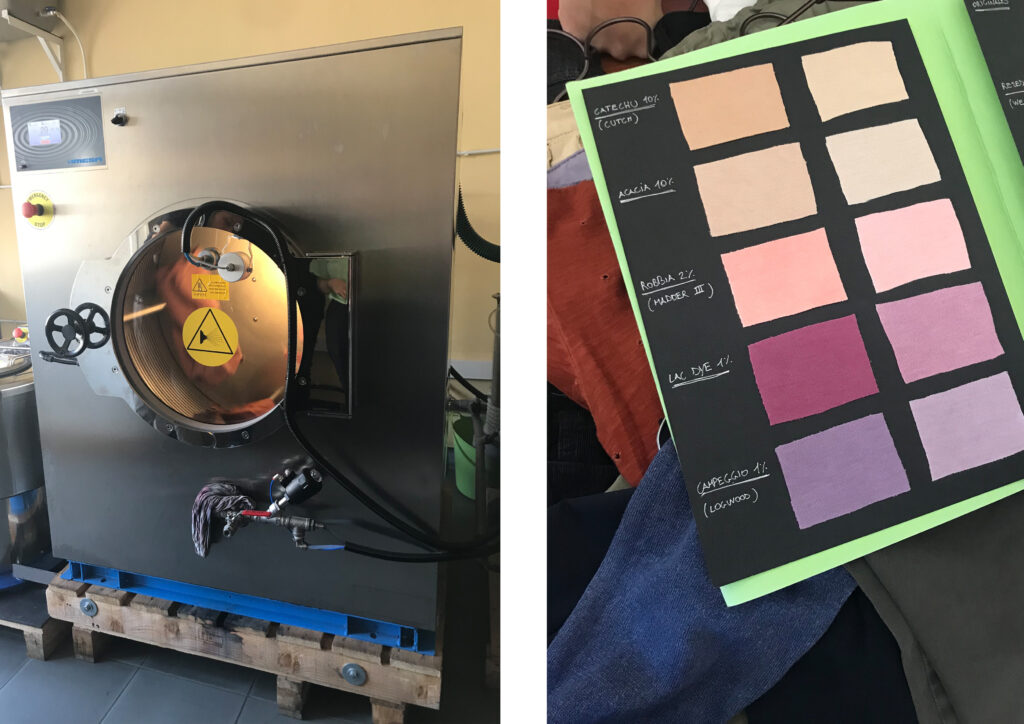
First Prototype Production
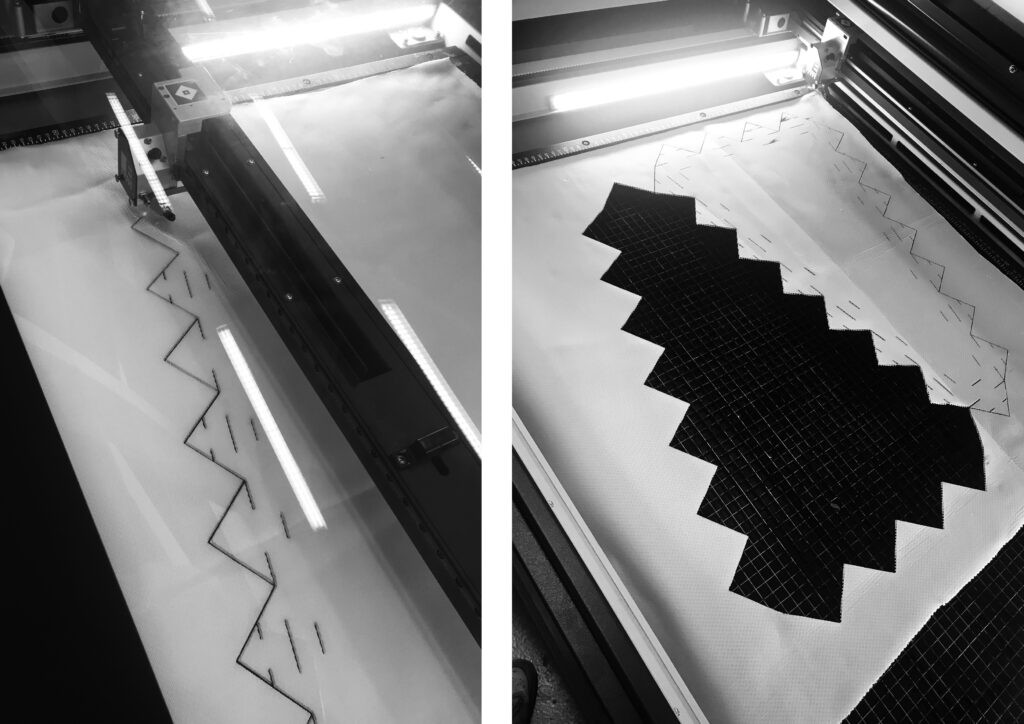
Once the proper fabrics have been found, and the correct machine settings established thanks to sampling tests, I launched the production of the first silhouette prototypes. Unfortunately unable to travel at this period of time to my other partner’s Aitex facilities, I was limited to using a small laser-cut machine instead of my partners’ industrial one which should have allowed me to cut all the skirt and crop top parts at once.
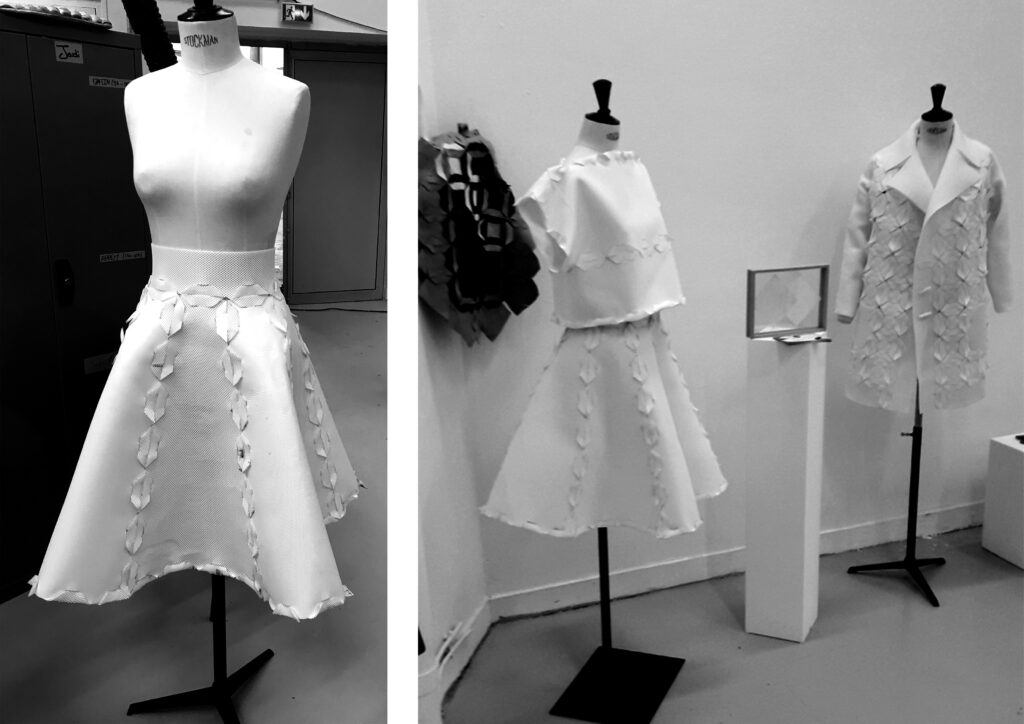
I performed the assembly of both the high-waisted skirt and the crop top on my own in less than two hours, which proves how easy and quick these puzzle garments are to mount.