Embroidered Touch | Life Space
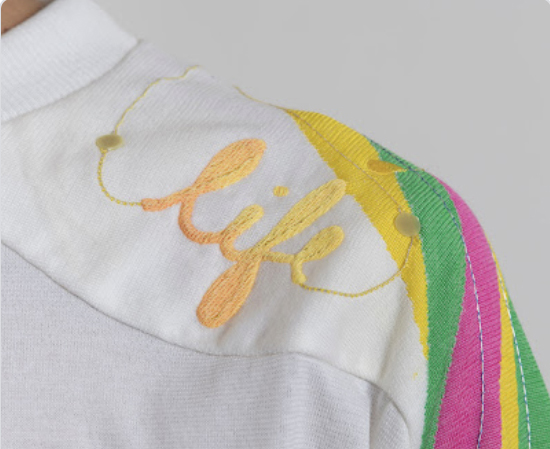
We’re in the home stretch of our Re-FREAM collaboration and it’s been an exciting journey to see everything come together. Together with the Fraunhofer Team, Christine Shallenberg, has been a masterful technology consultant during the entire process, ever steadfast at troubleshooting the software and programming for our garments.
With the Fraunhofer IZM team’s delivery of functioning prototypes, we were able to complete our photoshoot (with a big thank you to our wonderful models Nejla, Maia, and Enki). We will also record an informative video within the next two weeks, that tells the story behind this endeavor and its team of committed scientists and technology experts, that’s been a most rewarding aspect of a project that’s come full circle.
For readers who are new to our team’s work: Re-FREAM is a collaborative research project where artists and designers team up with a community of scientists to reimagine manufacturing processes within the fashion industry. The aim of the collaboration with my Re-FREAM partners at the Fraunhofer IZM was to advance and contribute to the development of touch-sensitive embroidered textiles.
At the center of this collaborative project, we’ve named ‘Touch (and in Staying in Touch),’ is the tactile nature of working with textiles, particularly in the context of machine embroidery.
- ‘Touch’ created the foundation and guiding principles for developing the technology and design choices I’ve made throughout this project, which is particularly relevant while living during a pandemic, where social distancing and a lack of physical interaction has become essential, as well as our ‘new normal.’
- To illustrate the interaction between the wearer and the smart textile, we designed software that communicates with a circuit board, picking up signals from the embroidered material when it’s touched.
- The data collected is then transmitted via Bluetooth to an app on an external device (laptop or mobile phone). The signals trigger a sound file to play through the device.
- The available sound files are a mix of field recordings from nature, urban spaces, string, and percussion instruments (a big thank you to the musician Peter Maunu for creating these sounds, as well as to Christine Shallenberg for her spoken and sung words).
- The result of this collaboration were four sweaters (two for adults and two for children), which communicate through sound and change color as a response to touch and body heat.
- The electronic module is integrated into the embroidered conductor tracks using the E-Textile Bonding technology developed at the IZM. The modules are connected to the textile substrate with thermoplastic, a non-conductive adhesive, thus enabling electrical and mechanical contact in one step. The new technology also provides contact with our thermoplastic insulated embroidery yarns, without having to strip them off beforehand.
- The sweaters for children were made with the TexPCB technology developed at the IZM. For this purpose, conductively coated knitted fabrics are laser cut into a conductor pattern and laminated into a thermoplastic matrix. The TexPCB was then laminated to the fabric and the electronic modules bonded
At the end of September, we will present the required 5-minute video and the 10 professional photographs within the Re-FREAM Group, and very soon after, we will share them outside the Re-FREAM community.
I hope you’re as excited as I am to see the final outcome! Stay tuned 🙂
Photo Ⓒ: Anke Loh, Detail