Fashion Design and Reverse Engineering? – Conversation with Guillaume, Sander and Ganit
As part of my research within ReFREAM project, I interviewed Guillaume (Haratech) and Sander (F&T) about the idea of using 3D scanning in the context of fashion design. They were both part of the process I worked on in Linz, Austria, in which I scanned and manipulated 3D files, and they are thus also part of this journey to find the best method for the unique new processes in my project.
The 3D world offers new possibilities and opportunities for designers to create unique and complex products that can’t be produced by any other method. But a more complex achievement is the way in which the physical world can combine with the digital world, and this is one of the missions I have been working on in recent months: to connect materials and processes from the point of view of the physical (the body), the digital (software) and finally production (materiality).
In the journey, one of the very initial steps involved a 3D body scan, which allows me to work out new ways of thinking about the transition from 2D to 3D garments. This process, which fascinates me, involves studying the combination of reality and the virtual world, and how these can be merged. The ability to design for a specific person enables me to design in a more efficient way, and produce garments that are not only unique, but that also ends up being a perfect fit for the wearer.
In the early stages of the process, I asked Guillaume and Sander three questions relating to things I was interested in- from their practice. It was interesting to analyze their answers and learn about their unique approach – one that tackles the idea of combining fashion design and Reverse Engineering.
Here’s the summary of our interview:
Ganit: Q1- Can you tell a bit about your background? Is reverse engineering part of the research you are working/have worked on?
Guillaume: Reverse engineering is rather new because the software and hardware we need for it was not available / not powerful enough before – though it is evolving rapidly and always giving new opportunities. The cases in my practice where it’s been used are:
1. working with a part that can’t be designed solely by using CAD software, or (with much difficulty) only by 3D-scanning it and importing it into design software. The Goals can be: making a mold to reproduce it, direct 3D printing, integrating it into a design for rendering, using it as a support/mannequin for further designs…
2. Reproducing a part that exists already with precision.
3. Controlling the precision of a part already produced by scanning it and comparing it to the original CAD data
Reserach Developments RE:
– Research project in fashion for tailor-made garments
– Research project in medicine, to design patient-specific bone implants
– Based on a CT scan, the implant is designed to fit the patient’s morphology, but also to optimise the mechanical strength of the Implant – its handling, its fastening, the bone growth after surgery, etc.
Sander : I worked as a product developer for a design company for about eight years. During this time I have reverse-engineered 3D models of products based on archival sources: 2D drawings, photos, 3D scans and prototypes.
This experience has had a great influence on the way I work: the direct connection between an object and the 3D interface and constant referencing helps me to focus not just on details but on the overall characteristics of form such as surface curvature continuity.
I see most of the creative process where 3D modeling is involved as a sort of re-engineering process, in which the concept and sketches lead. You have a vision of the product, and the way to get there is not just by blindly following the steps to model it quickly to get it done.
I see the process of modeling as a natural extension of the sketching process, where you can be just as easily inspired and distracted by finding new shapes and solutions. If you combine this with parametric models like those in Grasshopper, you can also easily shift through many iterations and variations to generate a family of designs, just as you would in your sketchbook.
Ganit: Q2 Fashion design and reverse engineering? what do you think about these two subjects together, especially in relation to the future direction of design?
Guillaume: RE can offer fashion design:
1. Huge potential for tailor-made garments, not only regarding the body shape, but also in relation to the addition of features/shapes that are suggested by the customer (for example, you could scan your cat and have it 2D- or 3D-printed on your pullover)
2. Greater independence from physical shops, as most of the steps, can be achieved at home and online
Sander : Right now my experience with these two is the literal reconstruction of a body or parts thereof, whether this is a scan that needs to be simplified or a couple of simple alterations to a standard avatar to get the custom size you are looking for. I believe the future is a flexible digital counterpart to the mannequin, where designers can quickly alter sizing, drape their fabrics and create their patterns for manufacturing, to be either outsourced or created on demand for a specific customer.
On the other hand, I don’t believe everybody should have to make an effort to buy custom-made clothes. Fashion designers and labels should instead strive to develop sizing systems that are clearer and more flexible, where you can trust the label if you know your specific size/body type.
Ganit: Q3 Can you share your thoughts on how the fashion industry/ the future of clothing will look like from your perspective? (Fashion in terms of wearing outfits – this could be related to smart textiles / sportswear / army uniforms, etc.)
Guillaume:
- Garments adapted to the body shape but also to the kind of activities they are used for (regarding stretching, wear resistance, transparency, breathability, heat insulation)
- Additional functions compared to what we have today (integrated phone, security features (airbag?), adaptive behaviour (to communicate with other people, to adapt to environmental changes (heat, rain…) or to activities (sport, sleep…)), transport (integrated flying suit?)…)
- Produced quickly without the need for human labour
Sander:
I believe the environmental aspect will play the biggest role in the future of how fashion is designed, made and ultimately worn. Given the cyclical nature of trends in fashion, the actual styles and types of outfit might not even be that different from those we wear today.
Thanks Guillaume & Sander for sharing with me your thoughts about the future of fashion & reverse engineering!
Looking forwards to share more information and ideas in the upcoming webinar today 5 PM (Austria) with the tech partners of hub Linz and the awarded Artists:
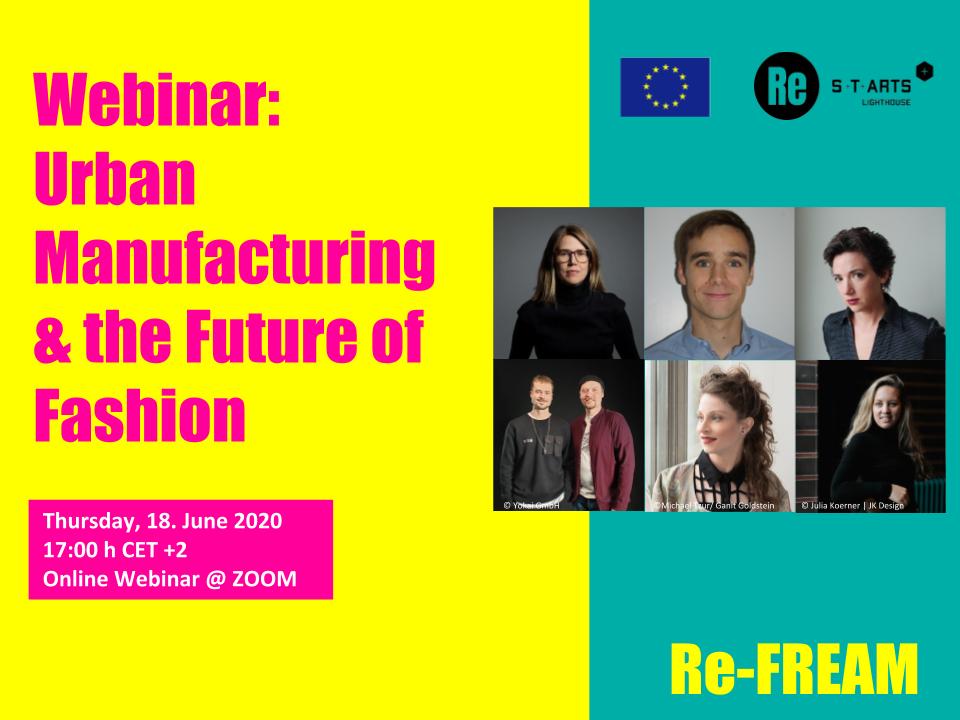