Marinero – 8
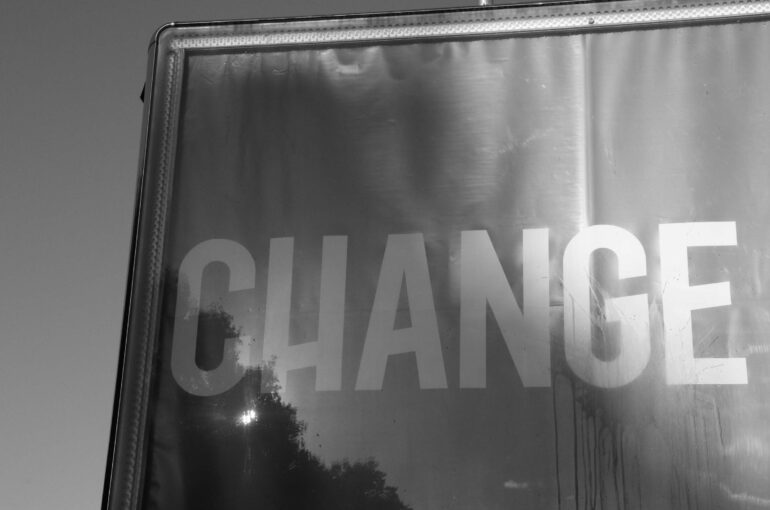
Since we are currently focusing on the new normal, I realize how important it is to think about the meaning of positive change. The daily news is asking what we can do to create a better future. What fundamental change do we need in order to shape the new world? My contribution towards this positive change would be to work with nature, instead of working against it. In my own experience I am currently feeling the urge to escape urban life. Within this time of crisis I take much joy wandering in forests and studying the growth of plants. To look for slow natural developments. Very small and simple, but truly super complex things! What I love about raw nature is that life grows uncontrollably. ”No control” inspired me to challenge myself, to not experience any control within the shaping process ´´design follows material´´. I can inspire myself to draw life lines within a textile blueprint, but the idea is to ”not touch or style the fabric” going from 2D to 3D. It’s about letting go the constant desire to control and perfect the process of creation in fashion. Allowing future fabrics to make a direct dialogue around the body, constantly changing and adapting.
With this project I am researching yarns and fabrics on a technical challenging level. Within this process I am shaping new design aesthetics, based on responsive technology interacting with meteorological conditions. The goal is to analyze the deforming behavior of 36 adaptive fabric designs. I can see what techniques work the best, based on the tailored by weather overview results. This information will allow me to improve high performing fabric blueprints in the future. The intention is also to optimize new and improved versions of the Archi-Filament. I would like to learn more about how I can push the boundaries between new materials and current technology. To eventually make the filament mechanically more powerful.
How can we shape our future fabrics? By looking at the essence of creating fabrics. For me this starts with designing and developing new yarns, that have unique architectural characteristics.
–
*Installation platform build up
During the installation build up process I asked Bart Nijboer to help me to install everything on the roof top. There was no working elevator in the building, so we spend a few days bringing everything to the roof. It took 1 day extra to install all 4 installations on the roof platform. I was very happy that Bart helped me to build up everything. He knows all the ins and outs of his installation design. We bumped into a few technical issues that Bart could solve very fast. I could not have done it so well myself. So, I am very thankful for his helping hands and adaptive insights.
I decided to start with 6 weaving designs ( seaweed category ) and 6 knitting designs ( mix category ). Starting with 12 designs, to be able to complete the total of 36 garments. There are 4 installations with 6 mannequins inside each installations. The idea is to begin with the first 12 in September and October and to finish the remaining 24 in November and December 2020. Starting this process is always very exciting, because you will always find nice surprises along the way. I am planning to use the first 12 as a trial and learn what I want to adjust, following up towards the second and last experiment.
–
*Installation 1 before & after effect
–
*Installation 1 overview – one by one
The idea for installation 1 was to create the Seacell category. The first 6 designs were meant to be non deforming, but during the process we did add some of the Aitex Archi-Filaments. It was a good initial test to see how these yarns work in a woven structure.
- Design 1: This design has a rib binding with Aitex yarns in the upper chest part. The lower part of the garment creates an a-line volume, because the Aitex yarns contract on the upper part of the pattern.
- Design 2: What you see here is the twill variation. The Aitex yarns are added in the waist area. This design has a lot of potential aesthetically.
- Design 3: This is the satin variation. The Aitex yarns are added partly throughout the entire fabric design. I think the right side of the binding shows an interesting texture effect.
- Design 4: Another twill variation. We added the Aitex yarns in the upper chest area and lower hips area. I am not a big fan of this design, but it is interesting to compare to the other designs.
- Design 5: This is another satin variation. The Aitex yarns are added throughout the entire fabric, using an interesting gradient technique. I like the detailed wavy textures on this fabric design.
- Design 6: I thought that the rib binding would be the ideal solution for the Aitex yarns. But this tighter woven binding shows that it was not really the case. It is important to know that we need to approach the fabric designs in an open woven style.
Important note: the twill technique works the best with the Aitex yarns.
–
*Installation 2 before & after effect
–
*Installation 2 overview – one by one
The idea for this category was to work with multiple knitting techniques and see how the Archi-Filaments respond within these structures. We were inspired by the base blueprints of the weaving designs and transferred this information within knitting structures.
- Design 7: What you see here is 1 of 3 variations. We used 1 fabric blueprint and switched the base yarns to create variations. We applied Rpet yarns for the base knitting construction and added the Aitex floated yarns on top of the knitting structure ( knitting and weaving ) The result with rain was clearly visible, but too minimal for what I preferred.
- Design 8: This is the second variation and has the same binding design as the previous one. We replaced the Aitex yarns with soluble yarns on top of the Rpet yarns. This deformation process is what I like to see, but I prefer that this effect is caused only with the Archi-Filament and not using soluble yarns to reach this effect.
- Design 9: Variation 3 is a mix of soluble Aitex and soluble yarns on top of the Rpet structure. As you can see, it’s visually a mix of the first previous designs, in terms of reached transformation. I don’t know if I personally like this aesthetic, but a good start for my first time ever knitting production. The issue for me lies in the technical limitation of the transparent net part of the design. We used a transparent thin monofilament to develop the net texture and created a knitted hole part for the head. It was nicely finished and we also added monofilaments floats on top of it, this in order to make it look more technically complex. It looks good, but it does not grab me so much as I wished for.
- Design 10: We decided to switch the pattern of the previous designs and try something new. The challenge here is that we are knitting in a different direction of the machine ( basically flipping the pattern 90 degrees ) The limitation here is that you need to accept the width limit of the ADF knitting machine. This is the reason why we created a top and skirt for this design. Aesthetically this matches more with the weaving designs, because of the 0,2 monofilament floats near the arms and the neck. I also liked what it did in terms of rain transformation. We used Rpet yarns to create the entire base knitting structure. The Aitex yarns create asymmetrical smocking effects, that result into an intricate texture. For now this was an interesting additional experiment. I will keep this in mind for the future.
- Design 11: The previous designs were interesting experiments, but I was still looking for a knitting variation that matched my expectations aesthetically. The final two designs came very close towards reaching that goal. We used the Wood K Plus textured monofilament to create the entire base of the garments ( floats within the knitting structure and also floating parts to create the sleeves and neckhole. Everything needs to have an organic flow )
- Design 12: The base of the final two designs ( 11 & 12 ) are developed with soluble yarns and textured monofilaments, all together connected throughout a knitted net. Only one variation is more loose connected and the second one has a tighter binding. This results into the two different looking textures. During the rain process the soluble yarns cause a chain effect together with the Wood K Plus filaments. The soluble yarns melt away and the net texture is what holds everything together, making this designs perfectly wearable. At the same time I also think that the material is transforming enough to make an aesthetic design statement. My goal is to study this technique more within a new project. But for now this was a very interesting experiment.
–
*Installation 1 + 2 time lapse documentation
–
*Installation 1 + 2 overall conclusion
The overall conclusion for the first two installations is that the combination of weaving and knitting show the best potential of wearable quality. The knitted prototypes are developed with sharp technical filaments, but they still feel soft on the skin. My plan is that I will continue to work with the knitting techniques in the future and also to create wearable prototypes for the commercial fashion market. In terms of project Marinero there is one woven design that shows the best balance between weaving techniques and added yarns. Design 2 could be a commercial prototype by just adding a few adjustments, in terms of silicone hem finishing. But I would need to find a production company that could create this finishing for me.
The biggest challenge with technical filaments are that they need to get a special unconventional ( non fashion ) finishing, because the cut ends can feel a bit sharp on the skin. This issue could be solved, by for example dipping the ends of the warp filaments with liquid silicone. This would also help to keep the entire construction locked in its own shape. So, the quality of the woven design will also become much better.
–
*Installation 3 before & after effect
–
*Installation 3 overview – one by one
The weaving mix category consists several materials like: Aitex Archi-Filament, Wood K Plus Textured and melt coated filament, soluble yarns, Rpet yarns, monofilaments and Seacell yarns. This category was intended to experiment with floats, but it did not seem to have worked out nicely in my opinion. I will continue to work on these fabrics by deconstructing some of the designs. I believe there is a potential when several filaments are removed.
- Design 13: What you see here is the twill variation. The idea for the first 3 designs was to add melt coated monofilaments. These Wood K Plus filaments needed to be added manually by hand. This was a time consuming and precious process. It’s a pity that I will need to cut them away, but in the end it will be much better aesthetically.
- Design 14: There are some minor transformation changes using the rib binding, but not enough to match my vision. What I am noticing is that the Aitex yarns do not work effectively near the neck parts. This is due to the fact of gravity ( fabric weight versus filament quality power )
- Design 15: This variation has the satin binding. The combination of all those yarns create a messy look, something that I don’t like. I am noticing that the Aitex yarns need to be only woven within a woven structure ( does not work effectively with floats )
- Design 16: The addition of soluble yarns in the remaining 3 designs contribute to make an interesting dialogue with the Aitex transforming yarns and the Wood K Plus filaments. This variation has a twill binding. I don’t mind the floats on this design, it looks good.
- Design 17: The second version shows another twill variation. The rain transforming part shows a different kind of deformed shape. The previous first twill ( 16 ) contracts in a flexible way and the second twill ( 17 ) becomes a bit stiff and reflects more light on the fabric surface. The difference between those two is that the first twill is woven more open and the second twill has a tighter binding.
- Design 18: The last design of this category showcases the rib variation. It seems that the chest, waist and hips are emphasized ( similar to the previous two designs ), but this quality is the most flexible. This means that the combination of soluble yarns and Archi-Filaments are crucial within this multi yarns category. However, 13 + 14 + 15 are wearable and 16 + 17 + 18 are more artistic objects.
–
*Installation 3 time lapse documentation
–
*Installation 4 before & after effect
–
*Installation 4 overview – one by one
The interesting part of this project is that you can experiment a lot. There is room to make mistakes, sometimes good and sometimes bad. However, it’s also about working on it until it feels right. The case with this category is that we only applied Wood K Plus filaments. It feels a lot more pure comparing to the chaotic playing around, that we did with the woven mix category. I am very happy with the aesthetic outcome of the Wood K Plus category. Visually it’s not something that I expected, it was a nice additional surprise.
- Design 19: With the first 3 designs we again applied the thick Wood K Plus melt coated monofilament. You can see it much clearer now, because we kept everything else very soft and simple. The transformation is minimal, but if you look clear enough you can see that it’s not a change in size, it’s more about a change in flexibility. We choose to add the melt coated filament every 21 cm within this twill variation.
- Design 20: The green glow is caused by the green sea weed yarns. The stiff melt coated yarns are placed every 14 cm within this satin variation. The melt coated filament has a thick outer layer of PVA and a thin monofilament within its core. During the rain it goes from very stiff to super flexible.
- Design 21: In this third rib variation it becomes clear to me that my favorite measurement is to add the melt coated filament each 7 cm. This is the most time consuming and expensive variation of all 3.
- Design 22: The remaining 3 designs are my favorite till now. Inside this rib variation we added the Wood K Plus textured monofilament together with soluble yarns. Within this category I do really like the floated design aesthetic. It matches more with what I had in my mind for the floated design. I wanted to create a synergy with the floats near the arms and more added floats within the fabric design. All together creating an organic flow.
- Design 23: The second variation showcases the satin binding. We used normal monofilament and added the Wood K Plus filaments within small strokes across the entire fabric. The effect looks crystalized and reflective at the same time.
- Design 24: This twill variation has the most added textured monofilament. I really like that the textured filaments and soluble yarns work well together. This combination creates the correct transformation during the rain. At first I was a bit worried, because monofilaments in general are stiff and not so flexible. But it seems that this combination causes a contraction. The only part that needs to be worked on for me is that this experiment is not wearable enough. It’s more a special item that I could show for example during an official presentation and also for pr purposes.
I am currently still looking for the correct balance within the remaining fabric experiments. I got a feeling that we will find this wearable balance within the next categories.
–
*Installation 4 time lapse documentation
–
For more info visit: www.studioadaptiveskins.com