Marinero – 2
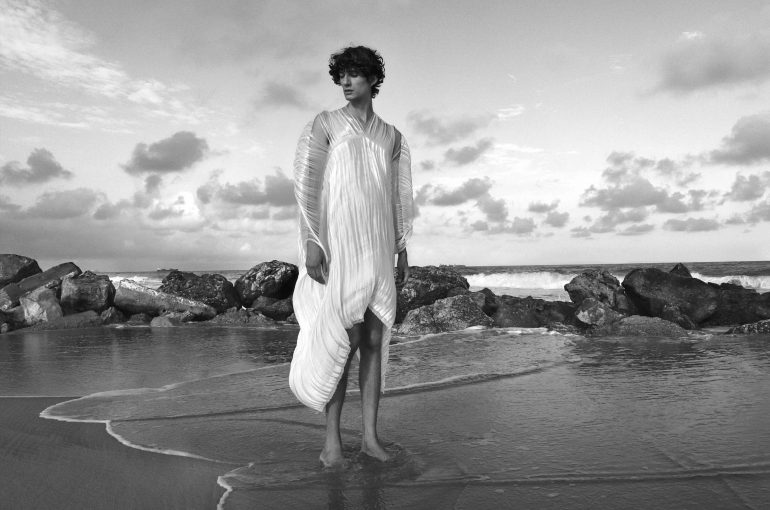
*Alternate yarn prototype
Medio December was the first meeting with Wood K plus in Linz. I got a tour inside the Johannes Kepler University Linz demonstrating all the services and techniques that the company offers. The facility main office and showroom of W.K+ are inside the university. It was surprising to see an experiment with one of their products, analyzing quality checks after 10 years exposure to several weather conditions. *Optical problem <-> mechanical problem / materials: wood in combination with polymers. You could actually see that the material was affected by mold and moss. This was very inspiring because of the connection with project Marinero and outside weather experiments.
In terms of Adaptive Archi Filament prototypes Wood K Plus team showed 2 variations. These were more monofilament based, but no deforming aspect. The team will follow up and make new prototypes early 2020.
Guillaume from Haratech will focus on mentoring the process with Wood K Plus. I was able to get in touch with Wood K Plus because they are a tech partner of Haratech. This connection was made after we decided to go from 3D printing towards yarn and filament producing. It is actually an amazing chance because I am now able to produce the same archi filament concept in Alcoy and Linz. From a research point of view this will be very interesting to compare the 2, in terms of deforming behavior.
–
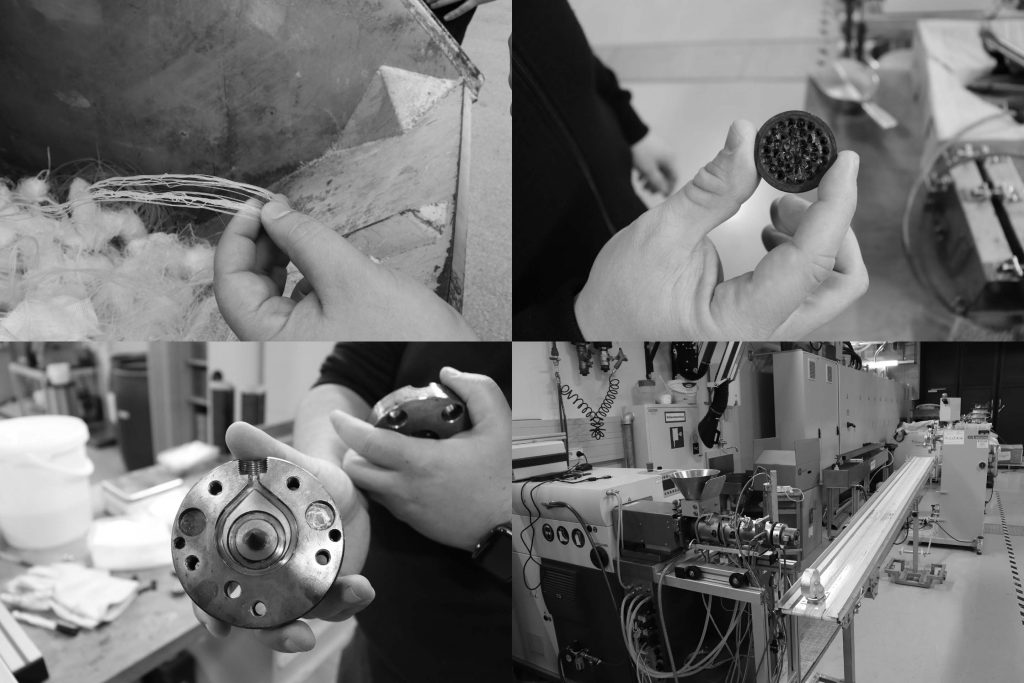
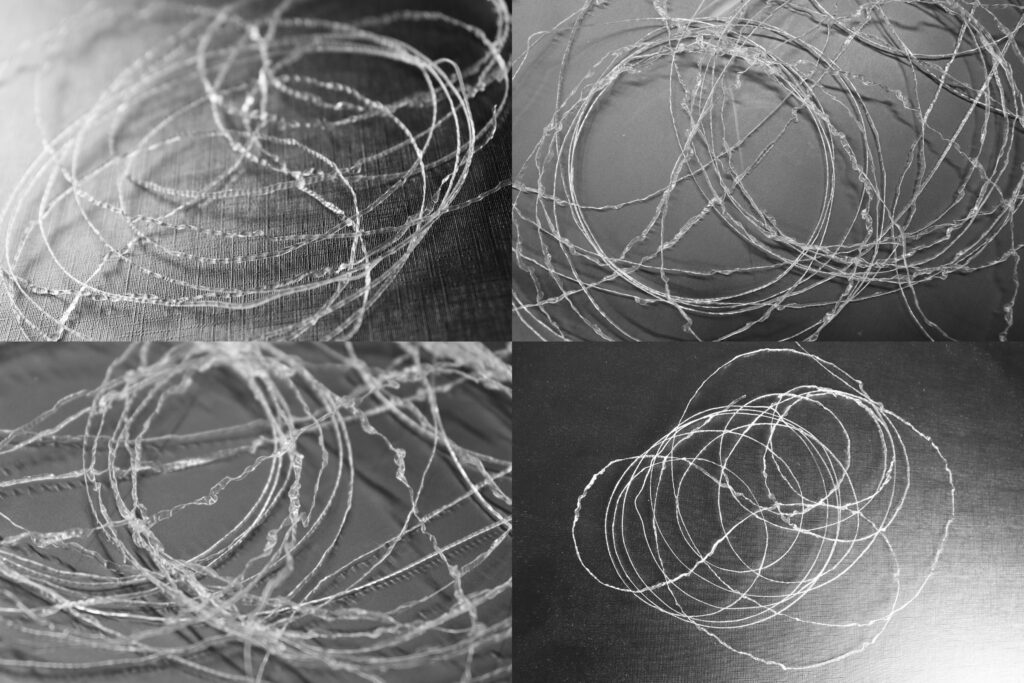
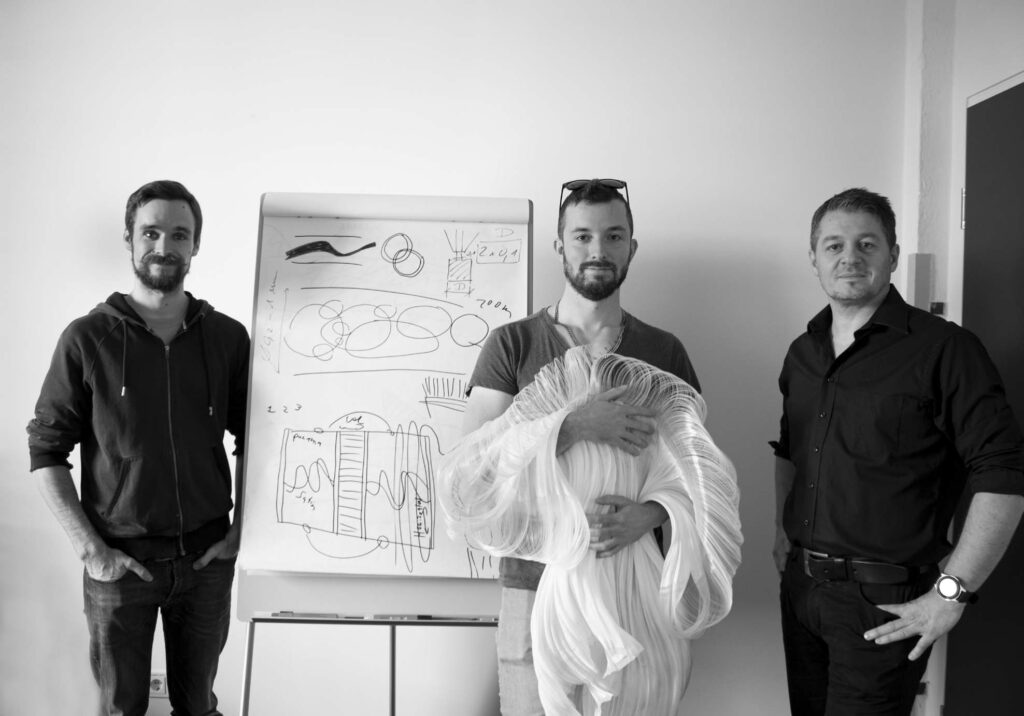
–
*F&T knitting test
In December Jef and Kevin went to Austria to visit the Fashion and Technology department (F&T) at the Linz art university (UFG). Kevin Pleiter is a knitting commissioner of Studio Adaptive Skins. He will analyse the first knitting samples in combination with the first prototype of the Adaptive Archi-Filament. The fashion department has an interesting collection of antique industrial Italian knitting machines. Kevin worked on the double bed knitting machine to produce some material samples. He used the Aitex version of the Adaptive Archi-Filament. The final step was to test the deforming effect of the material. To see and analyse the effect of the Archi-Filament, within a knitting structure.
Observation knit experiment -> Yarn gives a tendency to shrink, density is too dense, water cannot go anywhere. The knitted surface becomes to tight. The double bed knitting technique also retains water, such as sportswear fabrics. Elasticity is held together, does not get a free run. The looping technique of knitting is a limitation on the filament’s curl. The loops of the knit must therefore be as straight and open / large as possible.
Conclusion = you can see there is an effect within texture change and size. But the real 3D effect needs to be further developed on the industrial knitting machine of the TextileLab Tilburg. The body context and gravity will also play a major factor within the final knitted blueprints. The predictions are that the 3D effect of the Archi-filaments will start working effectively when the fabric is surrounded within a 3D (body) context.
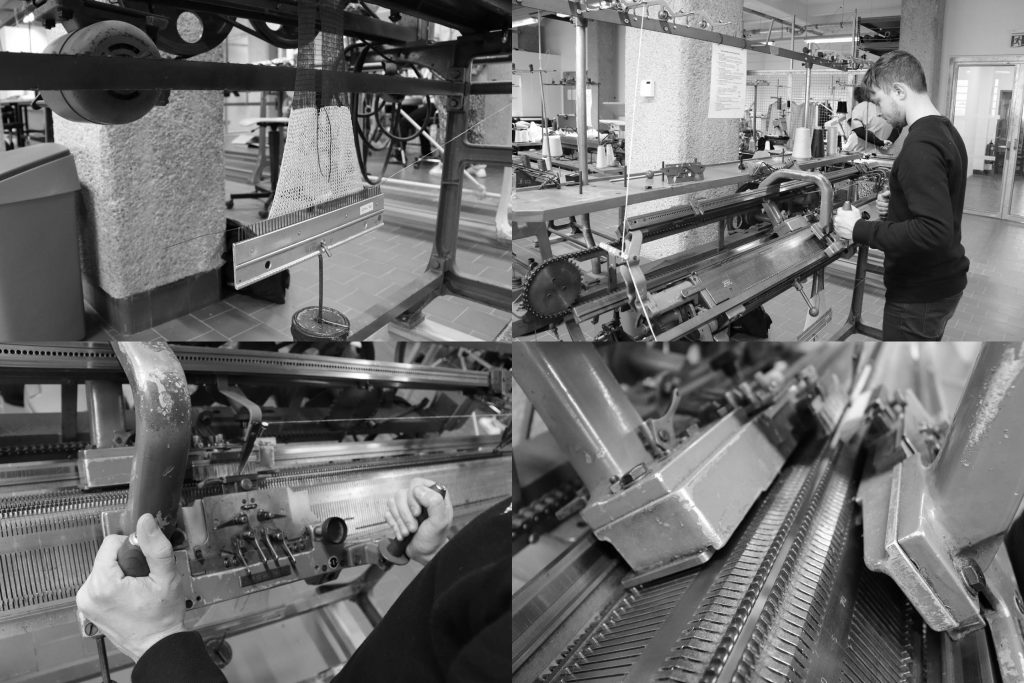
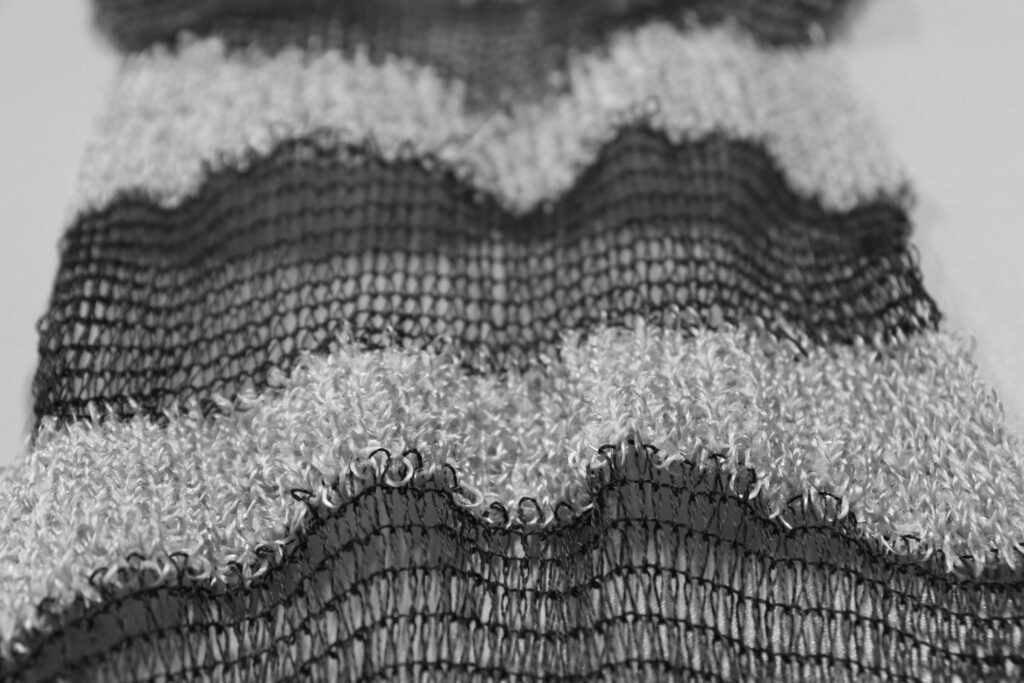
–
*Empa sweat robot
The last Re-FREAM meeting of the year 2019 was dedicated to Empa in Switzerland. Studio Adaptive Skins provided 2 of the Marinero first blueprints from experiment 1 & 2. Empa Swiss Federal Laboratories for Materials Science and Technology will analyse these garments on sweat mannequins. Parameters will be analysed and data will be collected. The rain is more an organic process, that you can not really capture data within the deformation of the actual garments. The sweat mannequin controls the moisture that comes from within. Within this frame we can actually see and collect data from certain parts of the body that have the most deforming fabric effect. In this case we can compare the ”tailored by weather” next to ”tailored by sweat’ experiments’.

–
*Tailored by sweat
Medio January 2020 Agnes from Empa material technology tested the two Marinero Satin and Panama samples. Compared to the ”tailored by weather experiment” the Empa robot test shows another way of material versus sweat behavior. The matrix shows that the chest and hips parts are the most effecting, because these body parts have a direct connection with the fabric. However the sweat also finds its way around the direct contact areas, depending where it moves through the fabric. This means that movement also will have an influence in making contact with the fabric. This robot experiment inspired me to think about a future project focusing on sweat. This seems an interesting step after having focused on the weather. In this case the next stage of project Marinero will go from external towards more internal.
Underneath you will see an example of the Panama garment (on the left) and the Satin garment (on the right) before and after effects.
Panama on the left shows more direct contact with the body – Satin shows more abstract 3D shape moving away from the body
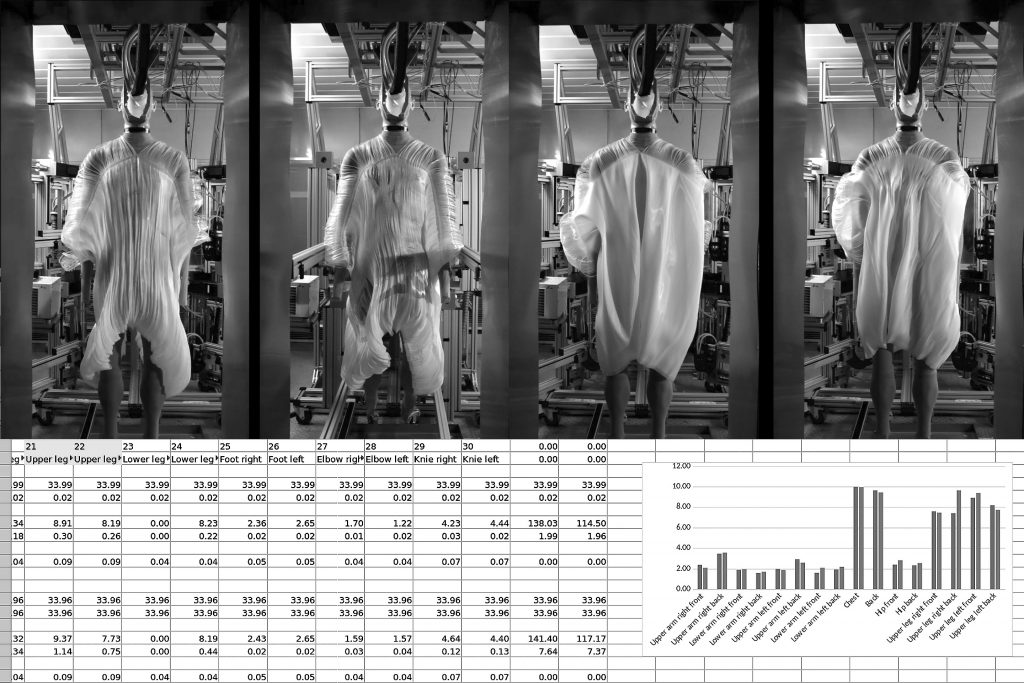
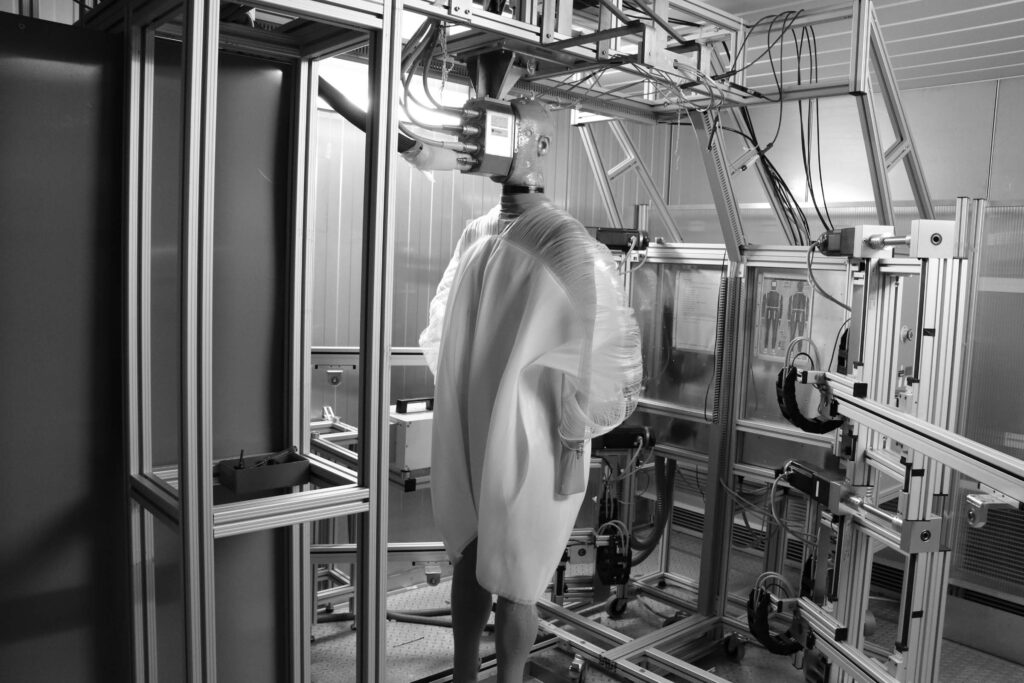
–
*Aitex prototyping
During the last week of January I was able to create a weaving test version with Aitex in Alcoy. Quico helped me to create the woven fabric. He knows how to control the weaving machine. The process of the mono filament warp needs to be done by hand. This was done one day before by two Aitex employers. Each warp filament needs to be transported by hand through the frame of the weaving machine. Quico placed the warp into the weaving machine to prepare the weaving process. The prototype of the Adaptive Archi-Filament (weft) was applied to create the fabric. It became clear that the final version of the filament needs to get a double dip-coating production process. During the weaving production the archi-filament started to unravel and this was not optimal. We need to improve this element. In the end we were able to create a weaving sample of 30 cm wide and 2 meters long. This was a great timing because we could show the yarn and fabric samples during the Midterm presentation in Madrid.
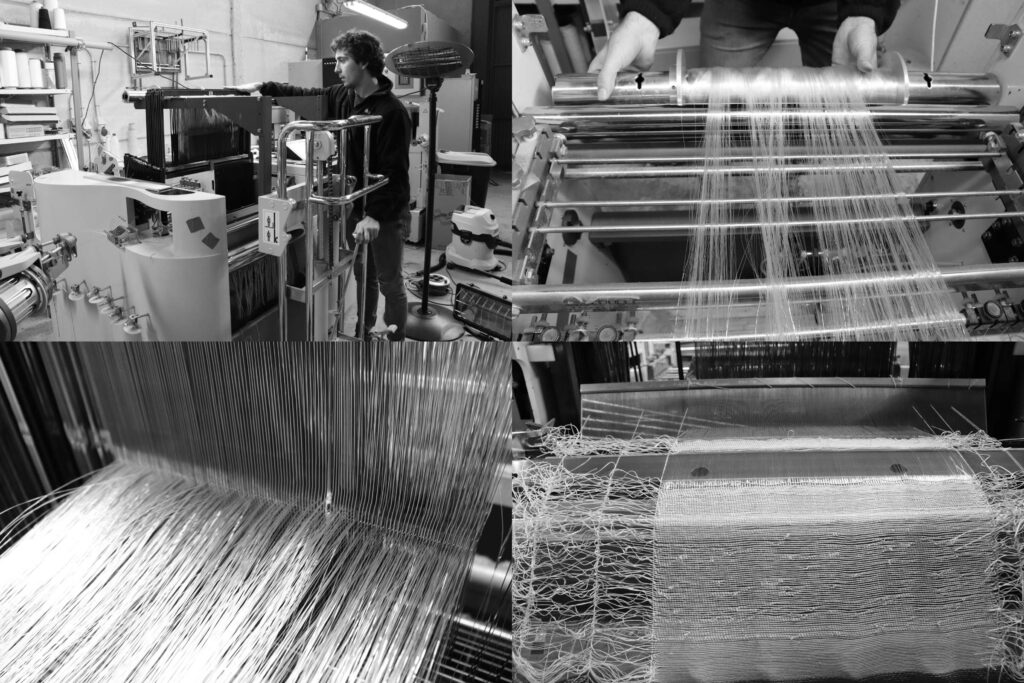
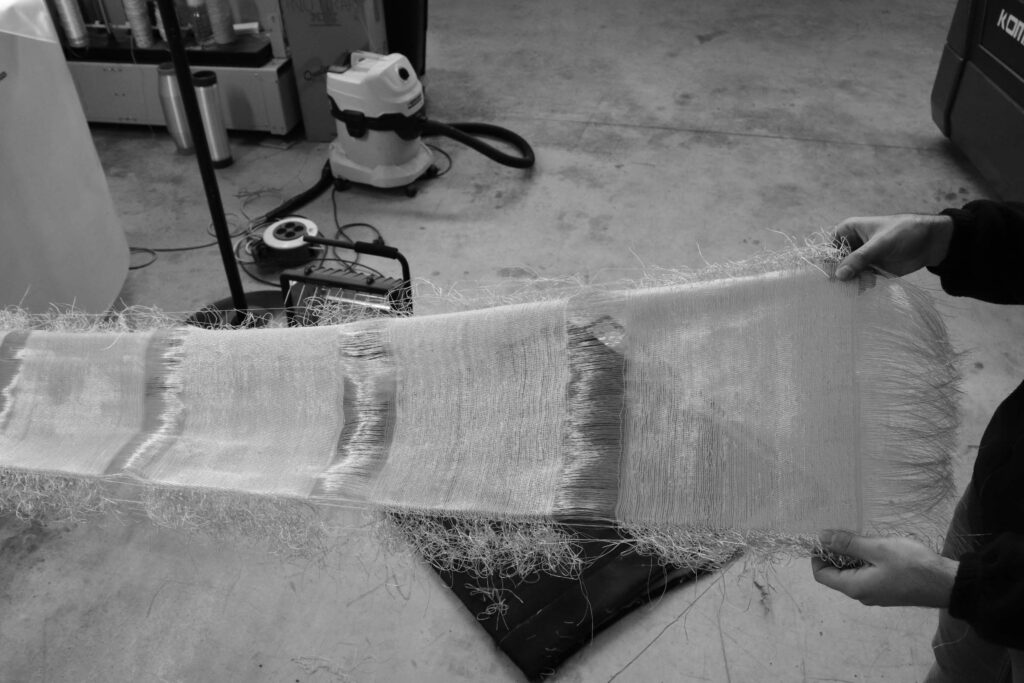
–
*Midterm presentation
During the midterm presentation in Madrid all the tech partners came to attend the Re-FREAM meetings. On the 27th of January we had a panel discussion and on the 28th all the artists gave a 10 minute presentation at the IED university, center for higher education of design. Aitex mentor Jaime and myself explained about the current developments and the next steps towards the final Re-FREAM presentation. Currently all the yarn prototypes from Aitex and Wood K Plus are almost production ready. In April I will work with TextileLab Tilburg to create the fabrics. And finally some metal constructions will be produced to start the outdoor ”tailored by weather” experiments.
Photo by: SOMOSMONOS
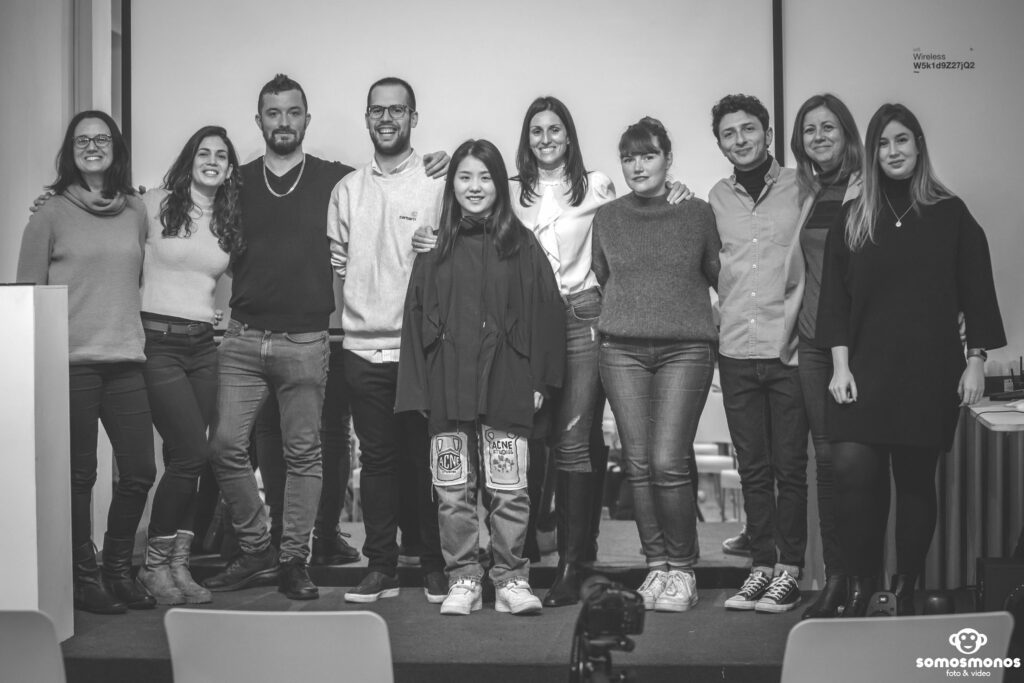
–
For more info visit: www.studioadaptiveskins.com