POSTNATURAL PROSTHESES: LINEAR FORMATIONS AND POLYJET SAMPLES
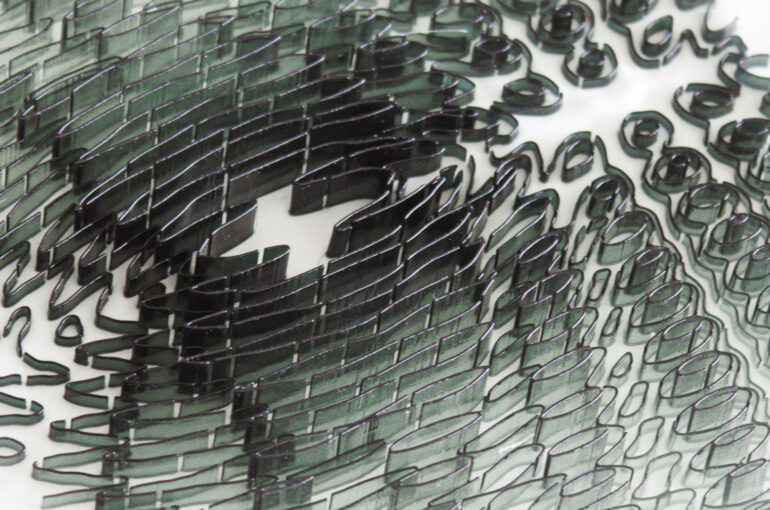
Our Co-research phase started by experimenting with Stratasys on PolyJet 3d printing on fabric.
The technology allows to augment a textile by printing three-dimensional structures onto it, whose shape, colour, transparency and flexibility can be controlled through a digital 3d model, at the resolution of the printed particle.
We are intrigued by the ability of the technology to fabricate such complex formations, and the potential to control the material at a granular level to interweave functionality and aesthetics.
Out of many sketches from the first couple of months, we selected two design strategies that seemed to have more fitting to address the potential of the technology, which are temporarily named linear and granular formations.
This blog post focuses on linear formations.
The idea of linear formations comes from a set of abstract drawings, whose visual language is defined by continuous lines and curves, distributed in a bi-dimensional space according to complex patterns. These studies are inspired by the visual richness and complexity of natural and biological formations.
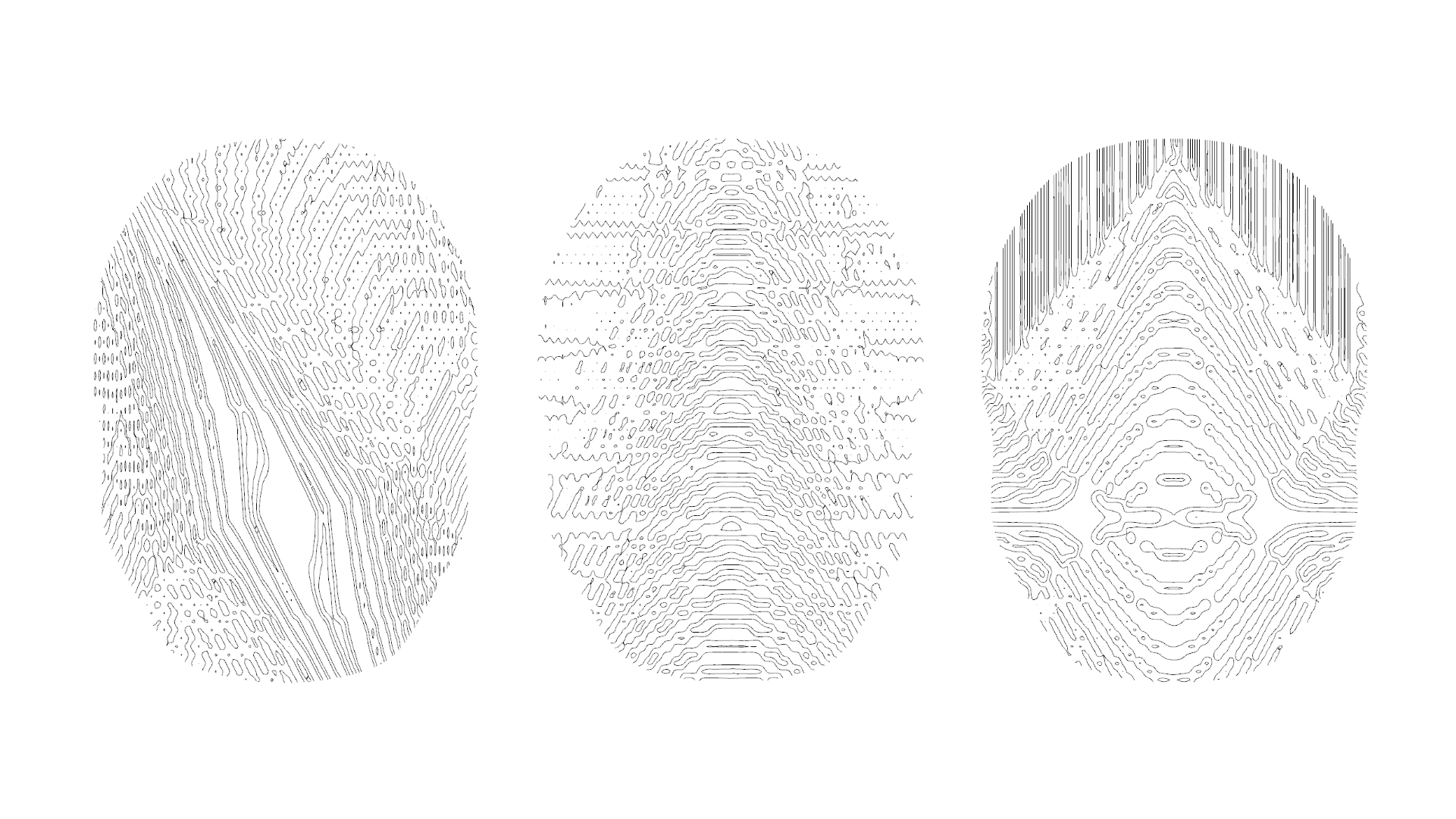
These abstract drawings were then developed in a set of 3d models for the whole protective mask, where the linear patterns are distributed on fluid surfaces, accounting for the shape of the fabric.
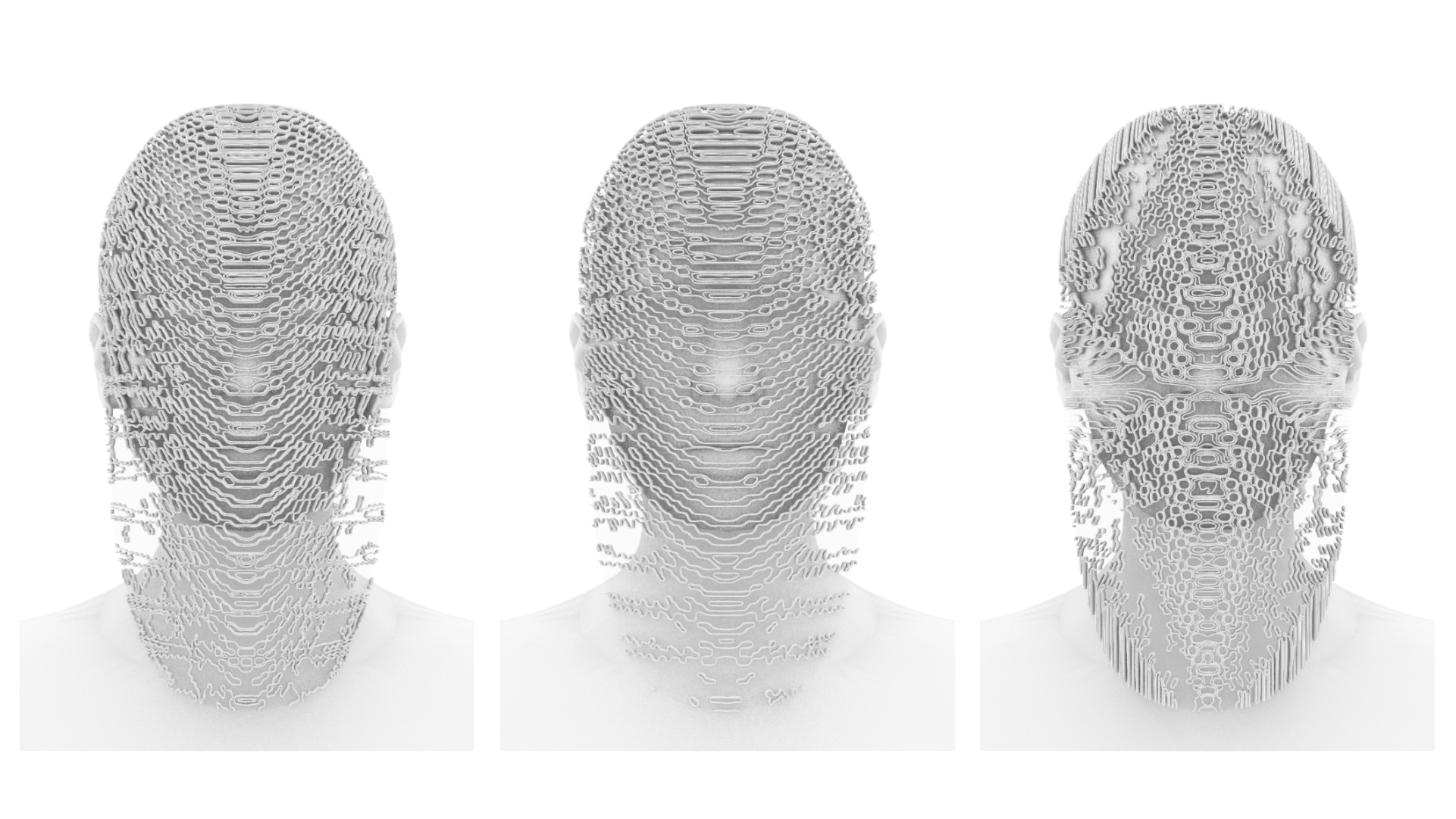
The concept and preparation of the files for printing was discussed with Stratasys, and it was decided to proceed by printing a number of small-scale samples, whose size and shape was designed to be at the same time general, and able to act as a prototypical mask.
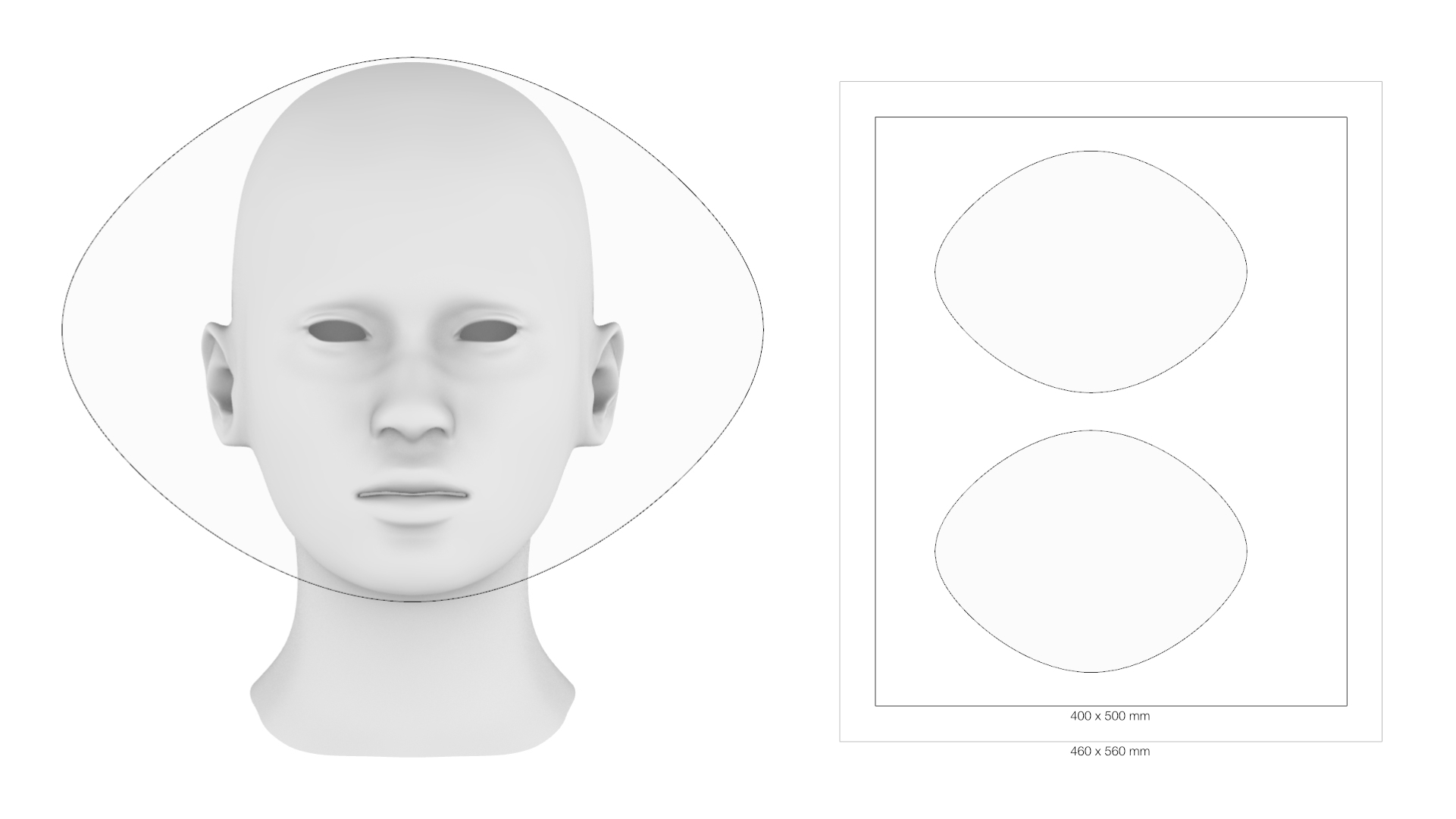
The idea is to distribute the material along the linear pattern on the surface of the textile, while varying its depth in space.
Such curves would act as non-linear grid for the distribution of the material, allowing for a cohesive visual language to emerge, while the functional and behavioural needs of the mask would be addressed by the quantity and thickness of the material being distributed. This may vary from area to area to adapt to local conditions, and relate the distribution of material to the physiological mappings of the body which are being developed in the Co-research with Empa.
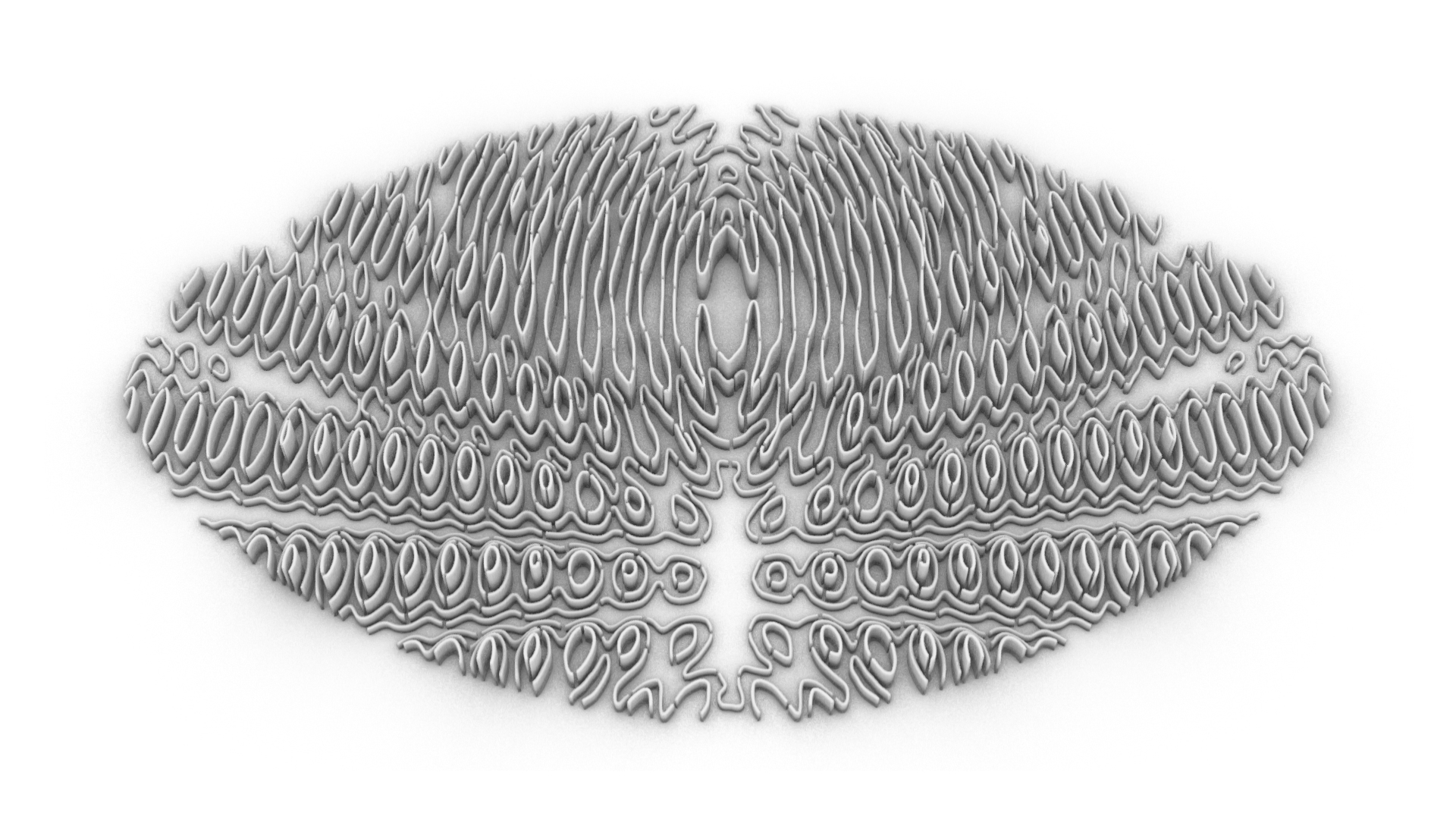
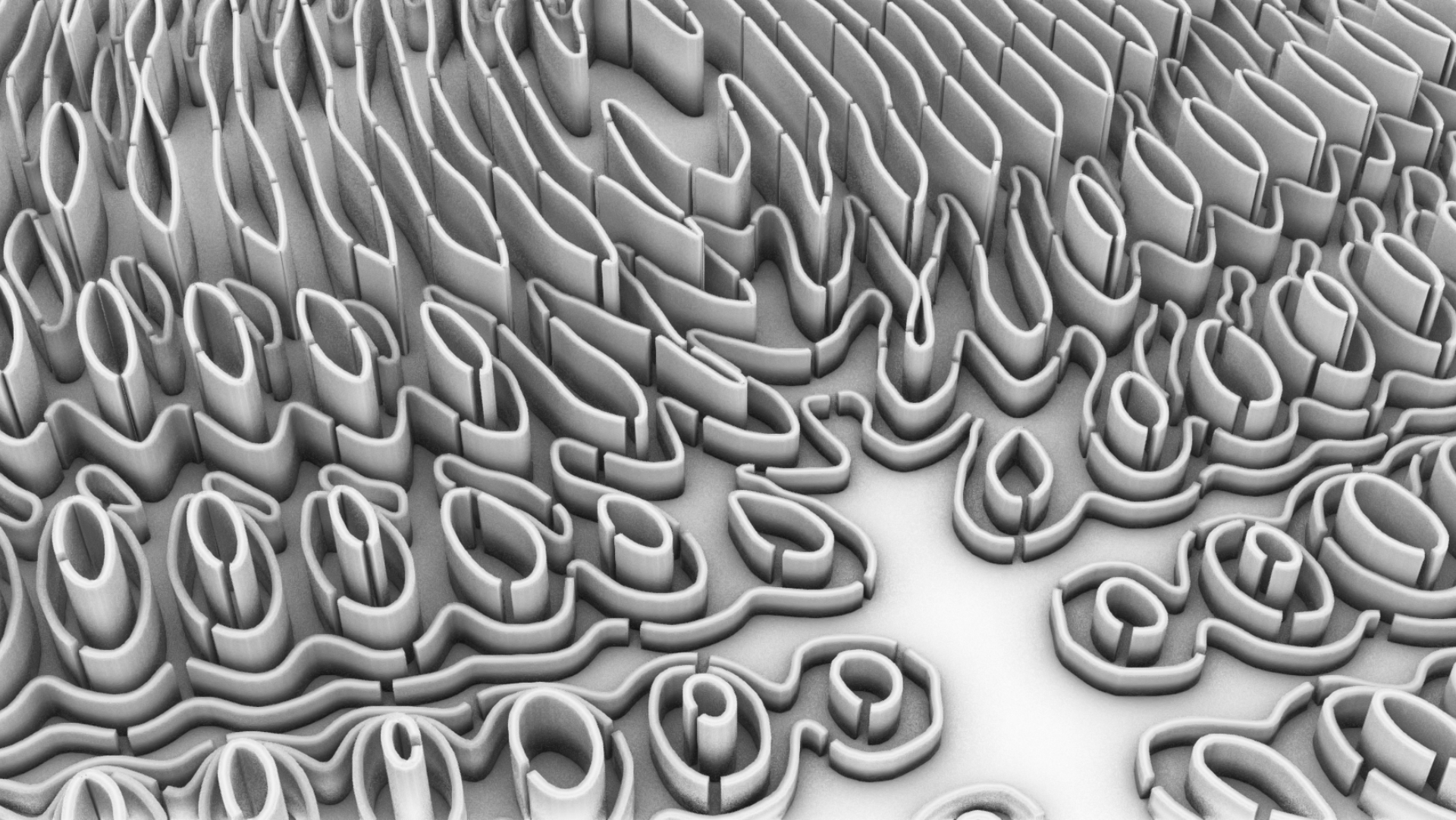
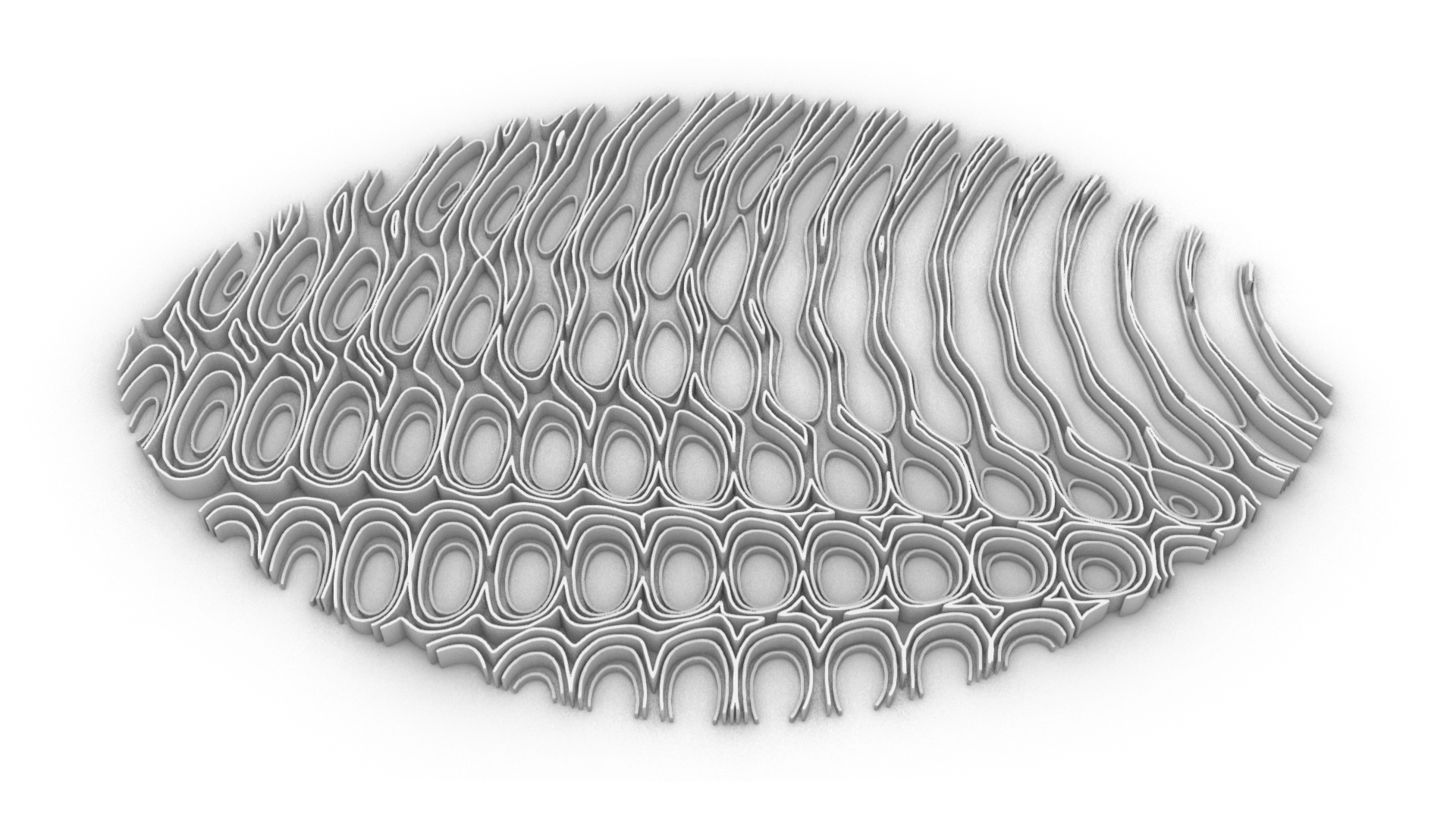
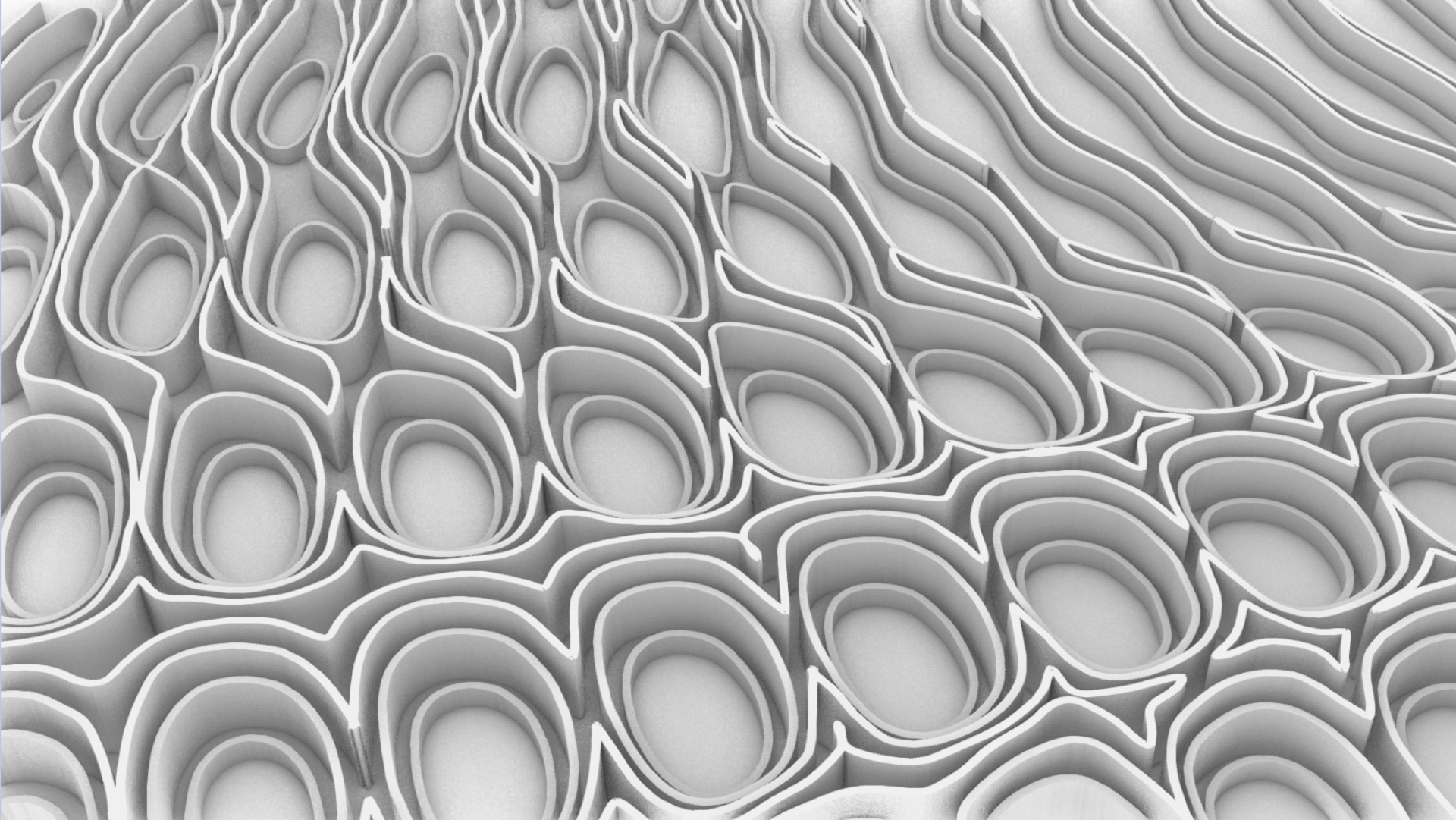
The PolyJet technology allows to change continuously the properties of the object, such as colour and transparency. Our co-research with Stratasys focused on coordinating such variations between the design model and the information sent to the printers.
After a few tests, we decided to work with a clear, rigid material, which supports the distribution of gradients of colours. By varying such colours, the transparency itself can be modulated, within a spectrum that spans from completely transparent to opaque.
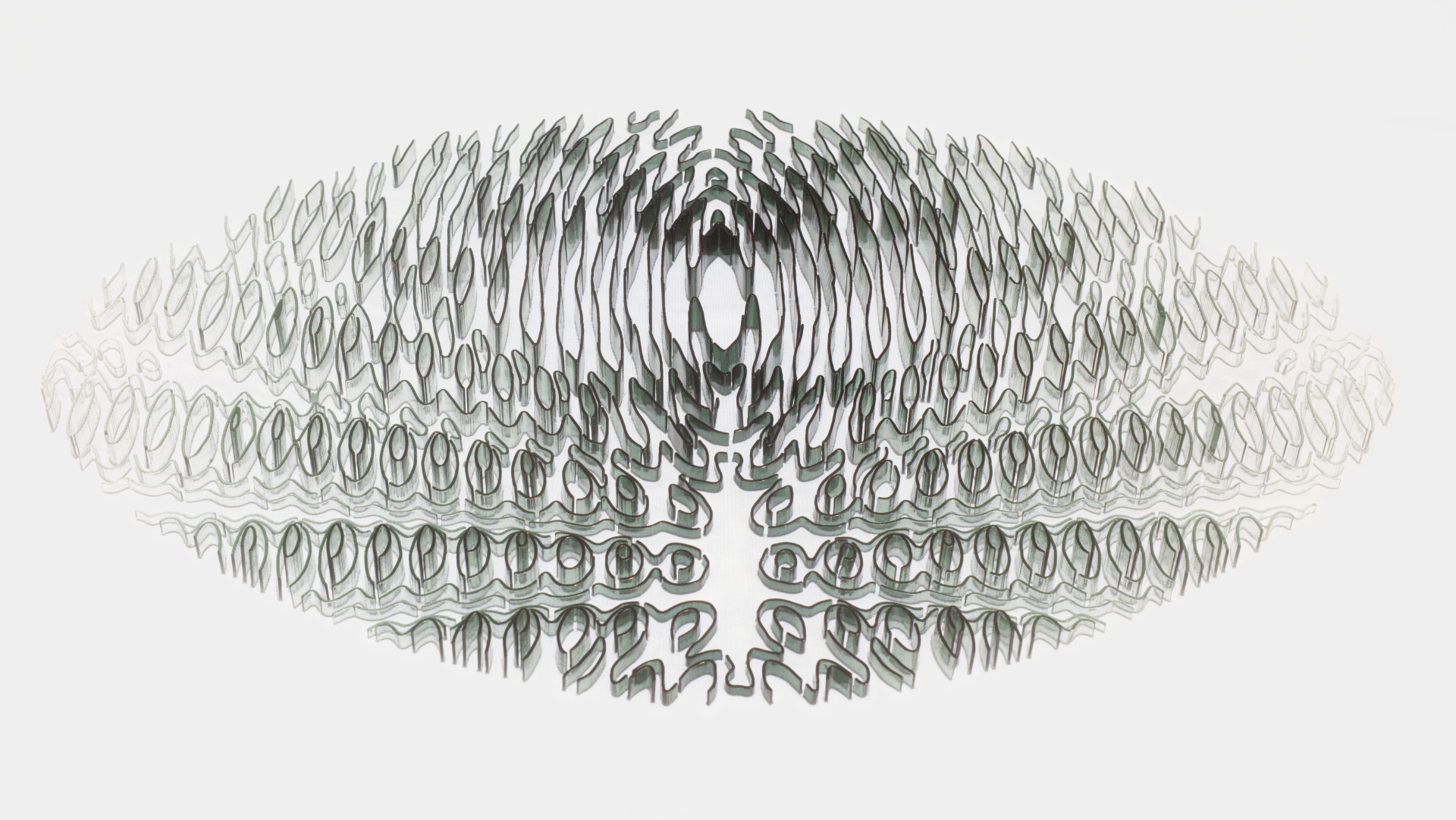
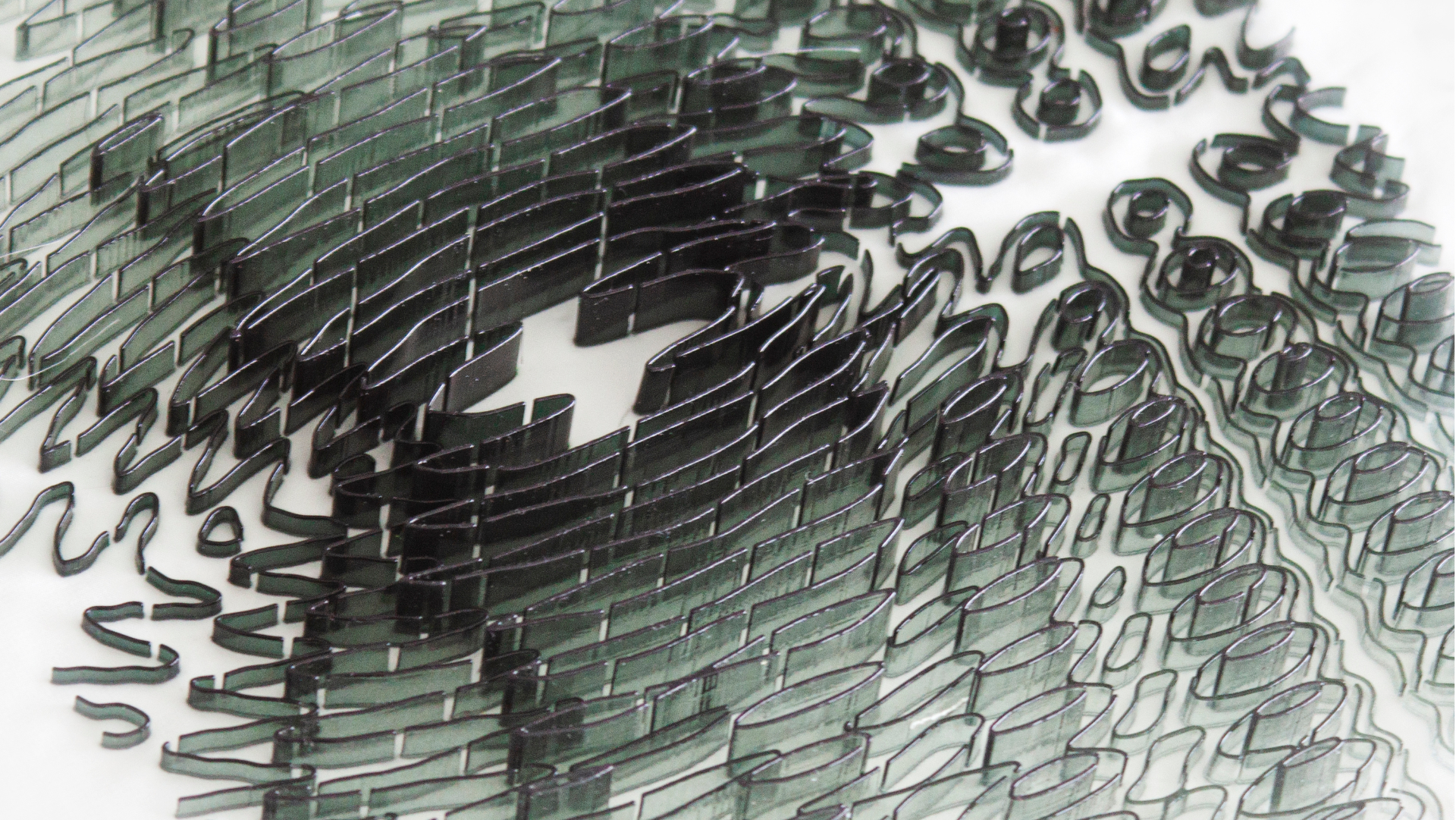
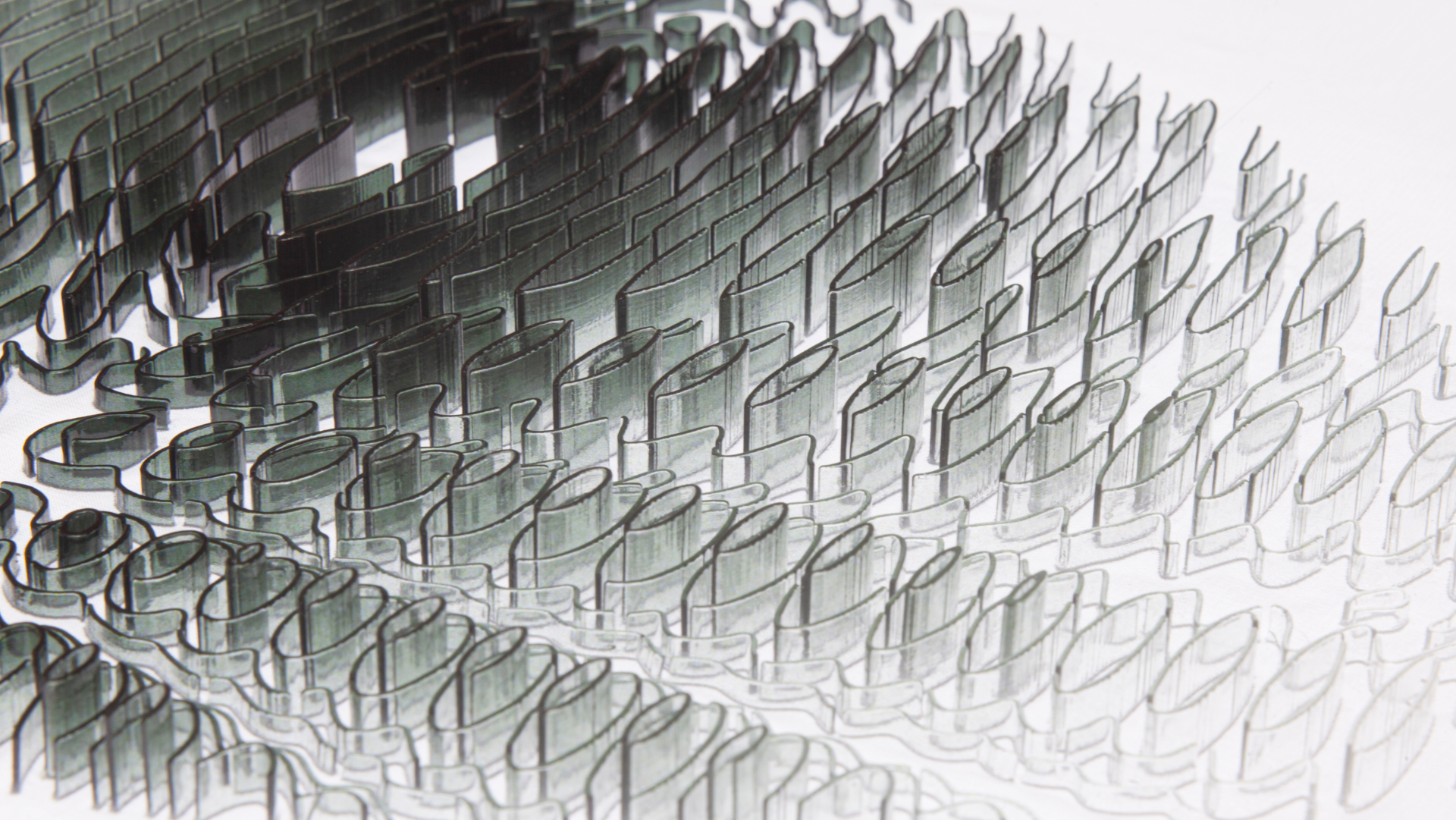
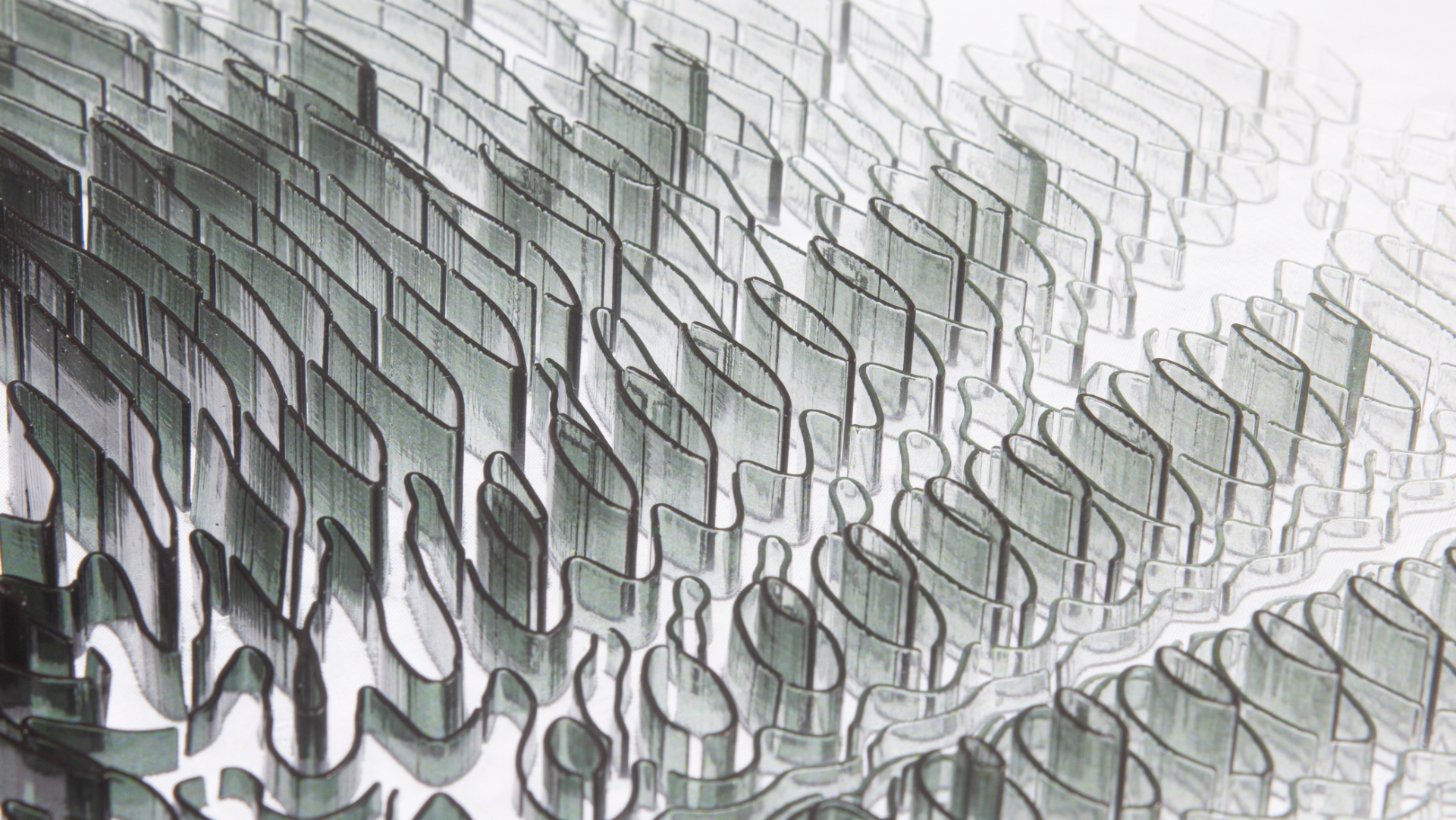
There was a machine error in one of the samples, which was printed completely transparent. While trying the sample on the face, we realised that the transparency allowed to nicely perceive details of the face behind the mask. Such unplanned feature proved then to be instead a strong opportunity.
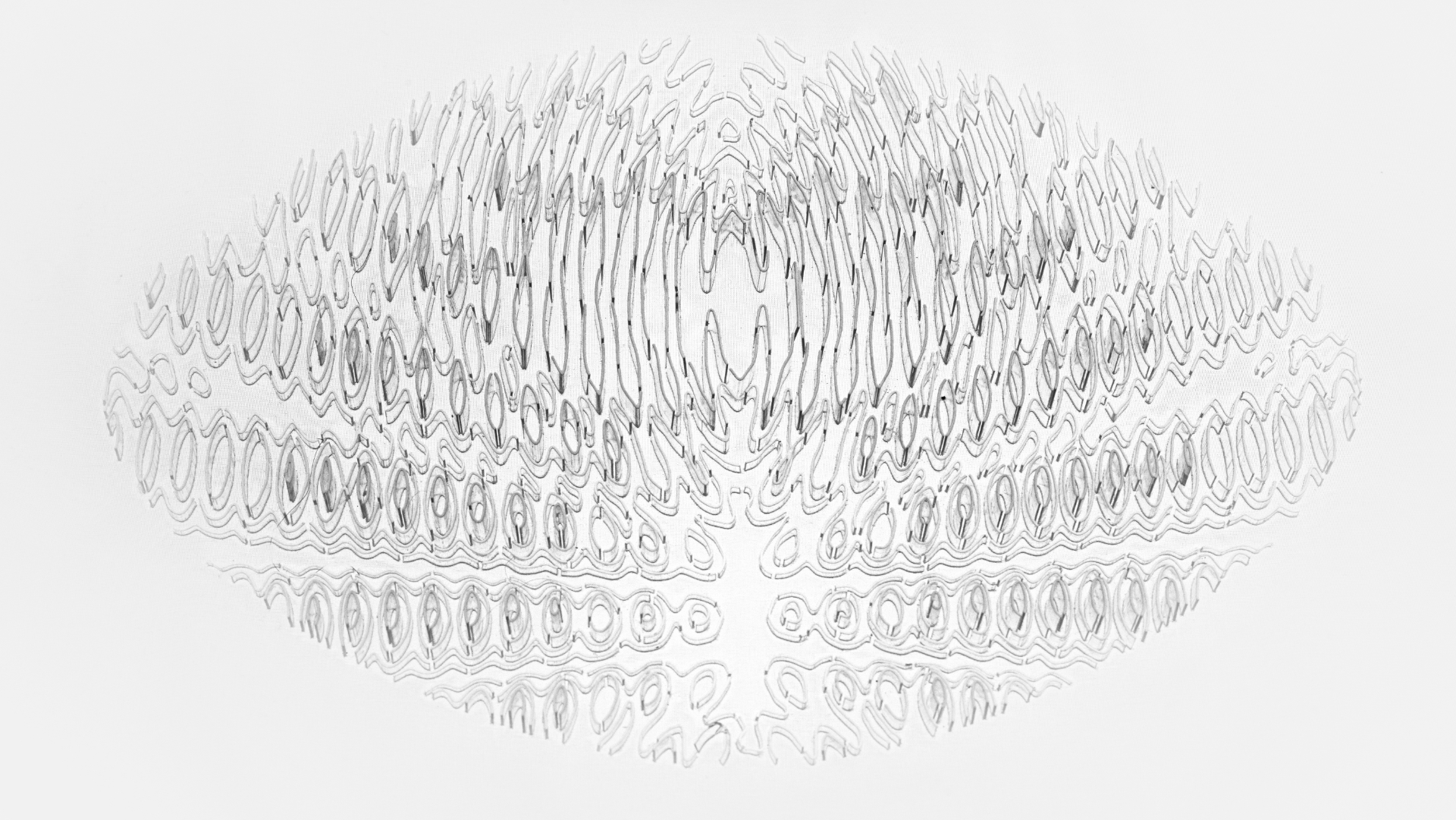
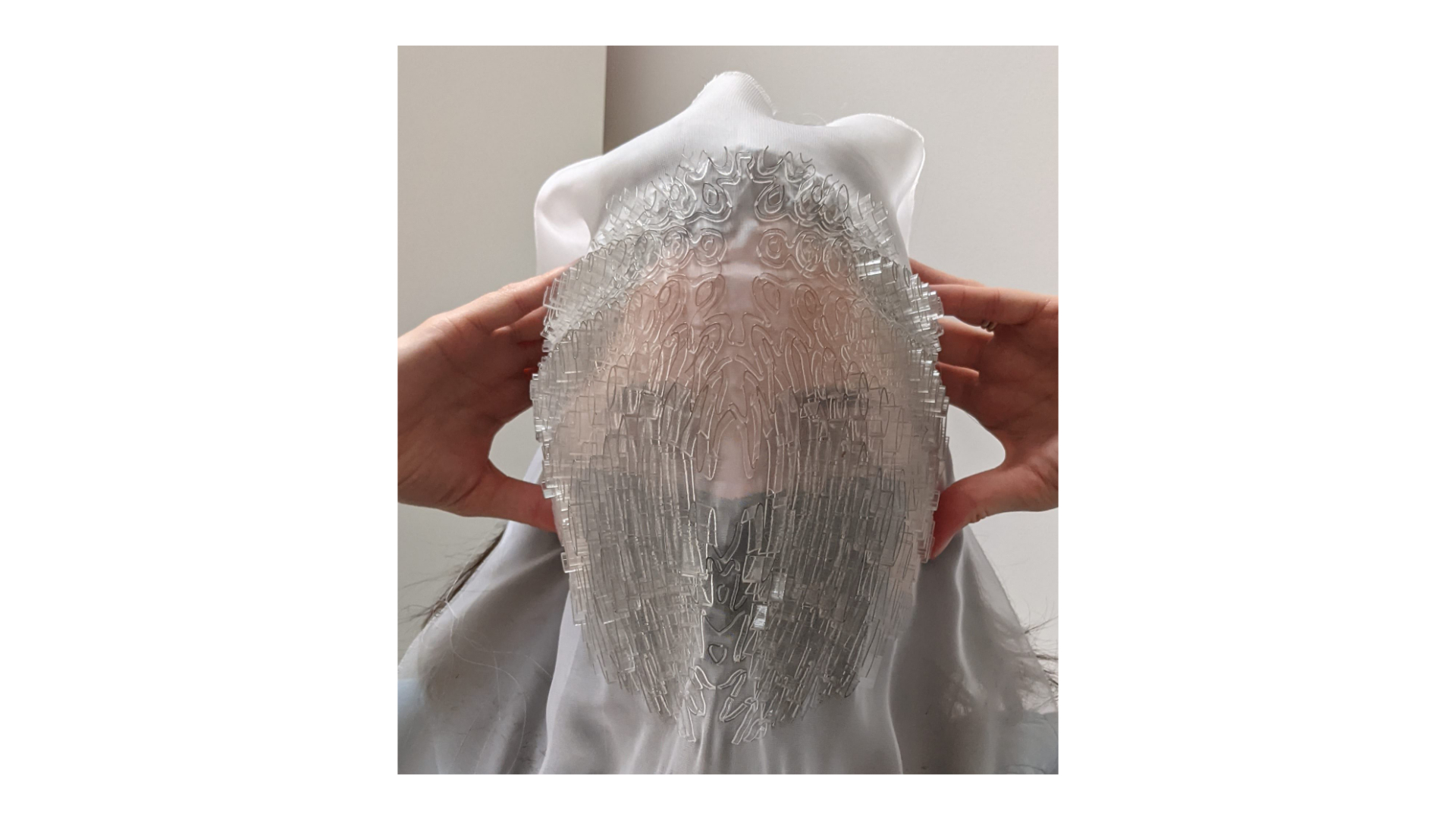
Outcomes of this sampling phase seem promising to be developed further onto a full mask prototype, as such they can be considered valid proof of concept of the linear option.
We are intrigued by the play of transparency supported by the varying pattern of the 3d printed structures, which allows to catch details of the face, while shielding it.
The design team and the Tech partners are planning to develop this direction further in the next months, by developing a first toile and design of the whole mask, and by assigning stronger functional meaning to the thicknesses of the printed elements, relating them the physiological mappings of the head.