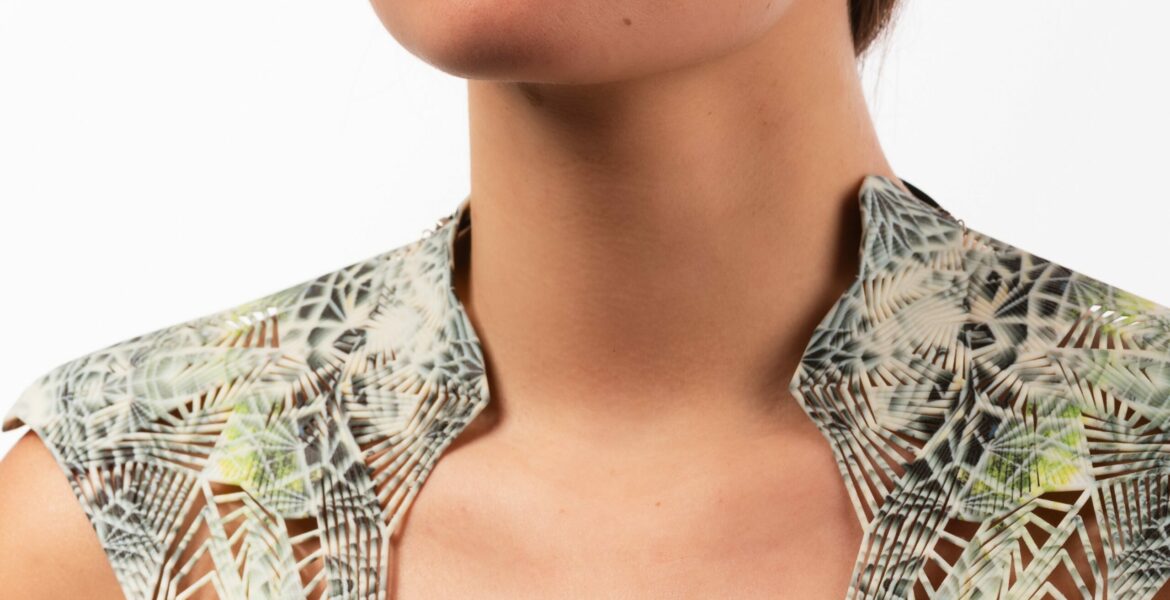
In the past 6 months, the tech team in hub Linz supported my research of using 3D scanning and 3D printing techniques to produce wearable 3D printed garments. I have been supported by Haratech, Stratasys, Profactor and F&T to re-invent how clothes are going to be made in the very near future.
I believe it is not just an algorithm that will shape the future of fashion, and not just the use of the latest technological developments, but it is the human factor that will determine how the future is going to be in terms of scale and production. Especially when we see how Covid-19 impacting the fashion industry and our daily lives. It is the time for a massive change which already been in many discussion for years.
With such great developments we have today within 3D printing, 3D scanning, VR & AR, I’ve been lucky to work on new techniques due to ReFREAM project. But I am always trying to throw myself back, practice hand made techniques which I believe will bring the human aspects in an ethical and aesthetic point of view, bring them to the front with the latest technology. The hand touch could bring back the balance and harmony in textile and fashion developments, which in many aspects, lost due to mass production processes. This mixture will be the place of re-inventing how we buy and how we dress in the fashion of tomorrow.
I am constantly going back to imagine the future, to think about how technology can help us to achieve better working processes – but also to use them in a conscious way.
I believe that by bridging past and future techniques, the tradition will co-exist alongside the amazing new developments that we have today in the virtual space. It is the combination of tradition and culture, which will enhance the new era of production, to bring fashion production- forward.
The ‘Fast Fashion’ (refers to low-cost clothing collections that mimic current luxury fashion trends) and especially movements that appeared against it in the last few years made us to question the resources, the way of production, and to really ask how a garment, from all the process of cutting, sewing, shipping can cost a ridiculous amount.
From my practice, the understanding of how difficult and complex the system of production of hand made techniques ( traditional weaving, embroidery etc.) affected how I see the textiles of the future, and how precious design processes are. I’m aiming for a design process that think about the starting point and the endpoint in a circular way, putting together a system of sustainable approach from the beginning to the end result.
In my research, two factors that I mainly investigate are, firstly, the process of customized garments, fit to measure by using Reverse Engineering methods, and secondly, fabrication of the garment using 3D printing techniques.
I believe that customization is the key factor in producing sustainable garment production, the uniqueness of each body shape, each figure, is the key for me to develop the new system of manufacturing 3D printed clothes.
3D scanning process of myself made at Haratech, using multi 360 Depth Camera, Linz, Dec’ 2019.
“For dealing with this challenge, I realized that my process consists of the methods of Reverse engineering, going back and forth to create the bridge between the digital and physical worlds”.

Exhibited in Milan Design Week 2019.
Photograph: Michael Tzur
The term “reverse engineering” refers to the approach for analyzing the design of existing devices or systems includes any activity you determine how a product works, or to learn the ideas and technology that were originally used to develop the product. The idea of using the body figure to produce the garment is the idea of thinking about the end product, before applying any design method. The development of 3D scanning for my project made it easier, for applying this vision into the reality of customizing garments.
In my practice from the past few years, I made many projects that relate to 3D body scans including garments, shoes, and jewelry designs. The ability to work on a specific figure is not only a solution for taking fast measurements, but also a new state of mind which allows sustainable fitted garments/ accessories production.


3D scanning & pattern making process using parametric design software (Haratech, F&T) Linz.
In ReFREAM project, I am focusing more on the production of customized garments, but I found that especially for shoe design, the need for a perfect fit using 3D scanning techniques is extremely relevant, connecting our body, technology, and customization for unique products.
Here some of my past projects for shoe design using the same method of Reverse Engineering in footwear.
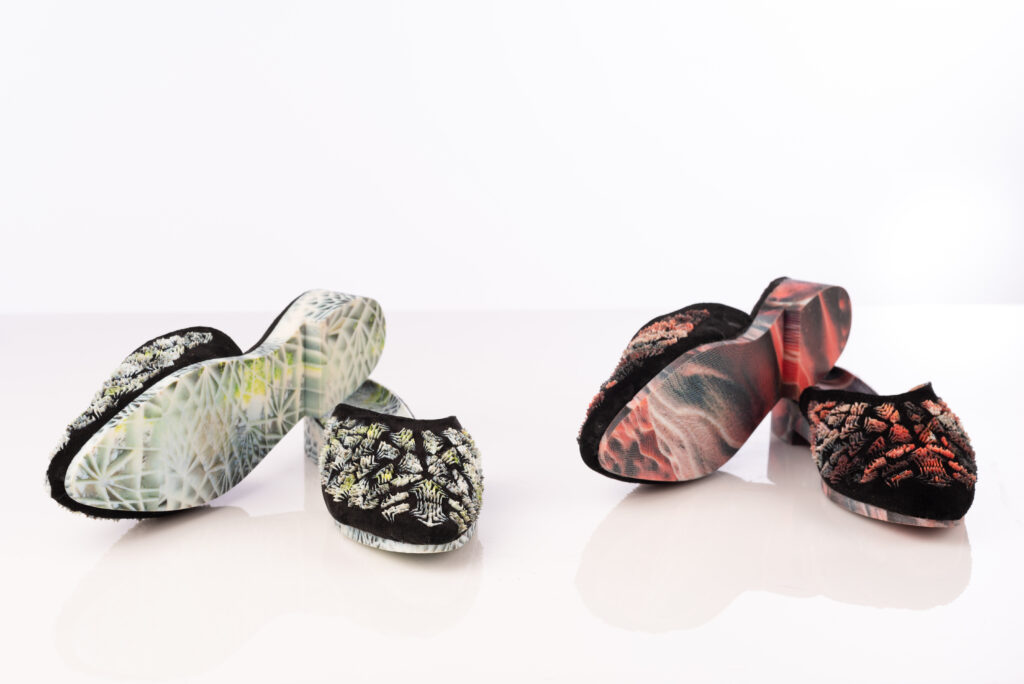
Presented part of Milan Design Week 2019, photograph: Michael Tzur.
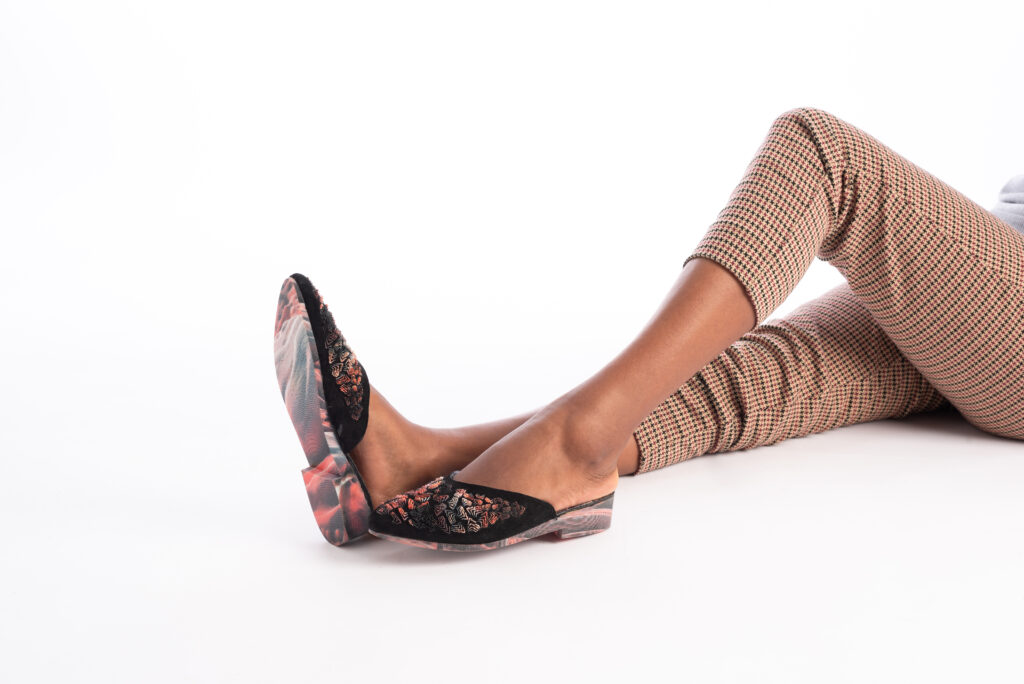
Presented part of Milan Design Week 2019, photograph: Michael Tzur.
For more information about this shoes you can check this link:
https://www.3dprintingmedia.network/ganit-goldstein-japenese-fabric-3d-printed/
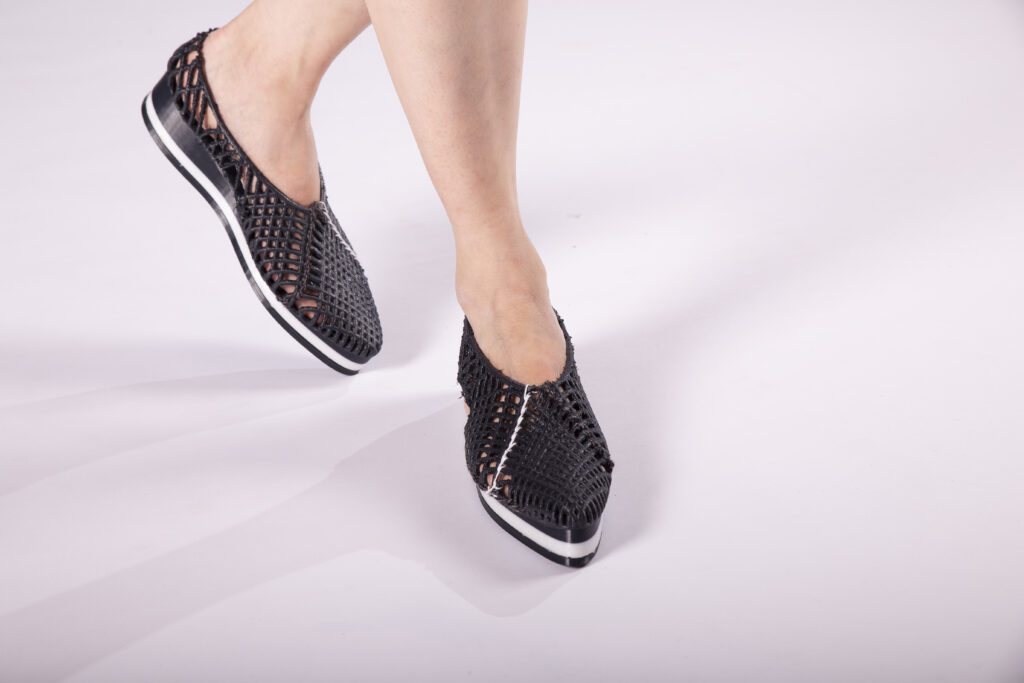


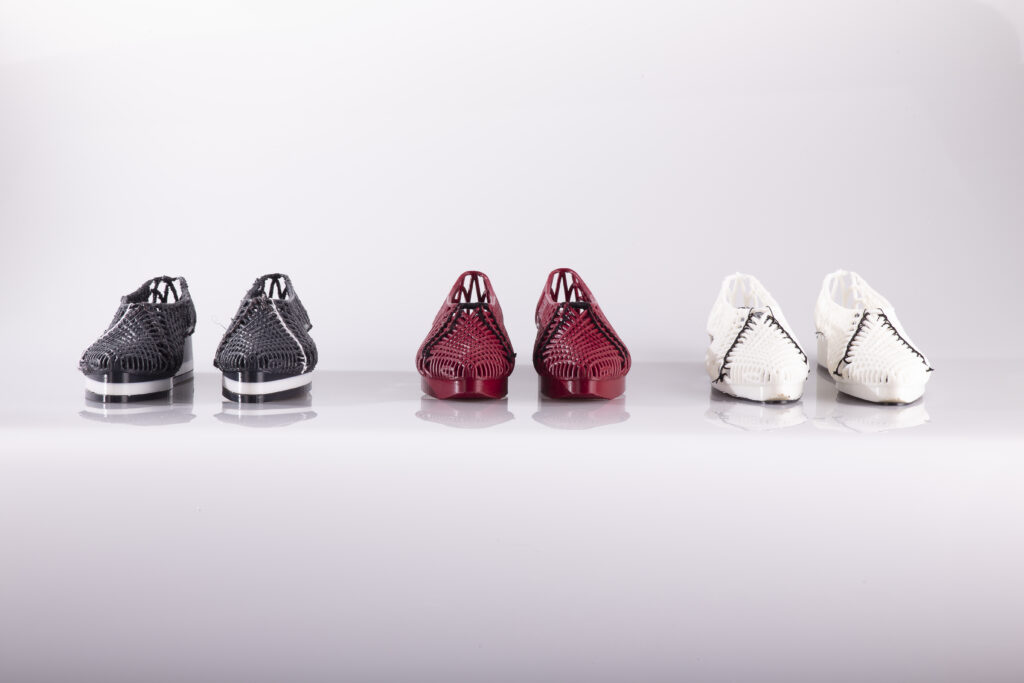

wearable 3D printed shoe collaboration with Prusa Research part of Emma Creative Center Residency program. photograph: Benedikt Adler
visit this article for more info:
https://3dprint.com/257261/ganit-goldstein-prusa-wearable-collection-of-3d-printed-shoes-and-outfits/
visit my website with more project related to this blog post : www.ganitgoldstein.com