Digital Vogue – 3D Printing on Textiles: customized, sustainable, and ready-to-wear
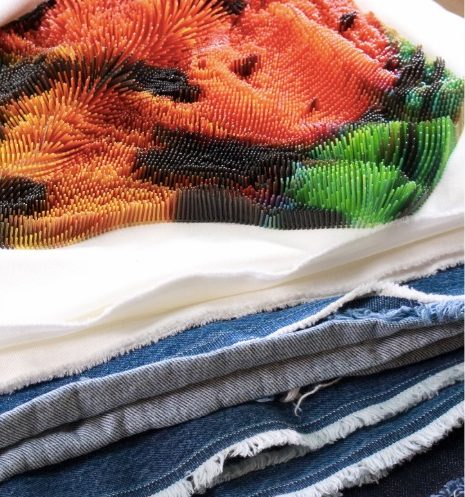
Re-Fream | Digital Vogue – from 2D to 3D | Co-Creation: Co-Define, Co-Research
Co-Creation Partners: Stratasys, Haratech, Profactor, University of Art and Design Linz, Department of Fashion & Technology.
The last couple of weeks in Linz have been intense. From early mornings until late at night. Days packed with meetings with my co-creation partners. We codefined our research questions & started with testing. We even traveled to Israel to visit the Headquarters of 3D printing company Stratasys and developed new research together.

Photography by Florian Voggeneder
“The core of my work is to create a relationship between art and technology – to break boundaries and to enter new dimensions in design & production”.
Within Re-Fream my Technology partners are Stratasys, Haratech, Profactor & my Consulting Partner is the University of Art and Design Linz, Department of Fashion & Technology. Since my creations are deeply rooted in interdisciplinary work the co-creation partners are one of the main assets of my projects, and with most of them, I have collaborated before. They are experts in their field that help me to get out of my comfort zone by giving me new insights into their disciplines and pushing my creations to a higher level.
Therefore, Re-Fream is the perfect project for me. Since the beginning, I knew I wanted to be part of it and applied with my Pilot-Project the “SETAE Jacket.”
Photography by Florian Voggeneder
Two main research points are “3D Scanning to Fabrication” and “Joinery and Assembly Methods” apart from investigating innovative geometries and novel aesthetics.
Innovation in the digital workflow from 3D Body Scan to optimized 2D layout for 3D printing
“The impact of 3D scanning of bodies could fundamentally change the way we shop for clothing. You could get your 3D individualized garment, which is perfectly molded to your proportions, to the symmetries in your body”.
Traditional design workflows involve design development for the standard-sized mannequins at early stages and transition into cutting patterns that developed for a series of standard sizes (S, M, L, XL, or 2,4,6, etc.). Customized tailored garments involve an extensive measurement process to develop a personalized fit garment. Today, three-dimensional digital design workflows include a design for a base 3D model and require adaptation at later stages for customization to individuals. When designing for printing on textiles, the process then requires an additional step of unrolling the 3D model to two-dimensional surfaces for direct printing on the textile, to be later put together into a 3D design.
This research aims to streamline the design process, from 3D-body scans to the final 2D layout for fabrication. Generative and parametric design methodologies, together with software interoperability workflows, can enable an efficient and automated process of adapting a design to every unique individual’s dimensions.
Photography by Florian Voggeneder
Photography by Florian Voggeneder
Innovation in nonstandard sewing techniques and connections
3D printing on textiles comes with limitations of the printer bed-size as well needs assembly after the printing process. This limitation means that a garment needs to be produced in several parts, and a joinery technique is required. Traditional processes utilize sewing of the pieces, which can be time and resource-intensive, and also the quality can vary. Similarly, this means that the garment needs to be 3D-printed in one location, assembled in another, and shipped to a final place. This research aims to investigate innovative joinery methods that can result in high quality and novel techniques of assembling a garment that can also be done at the same location where 3D-printing occurs, or even at the final place with the consumer.
Photography by Florian Voggeneder
Innovation in a fashion that is environmentally friendly, revolutionary in its designs, materials, and process
“The fashion industry has a significant negative impact on our environment, from water consumption, natural resources, carbon footprint, to waste — similarly, a negative socio-cultural impact from sweatshops”.
3D-printing has the potential to disrupt the fashion industry and turn around its environmental impact by using recycled materials, biodegradable filaments, reduced waste by higher durability, and elimination of sweatshops. Using additive manufacturing directly on the fabric, we design the geometries in a way so they don’t use any support material and therefore only use as much material as needed. There is no water used in the process. The color is added during the printing and therefore no color dye is used either. Along with the research into innovative novel geometries and aesthetics, I am continuously interested in the sustainability aspect of what these technologies can offer. I think it is important to look at the choices that can be made within 3D-printing on textiles which can result in a positive environmental impact.
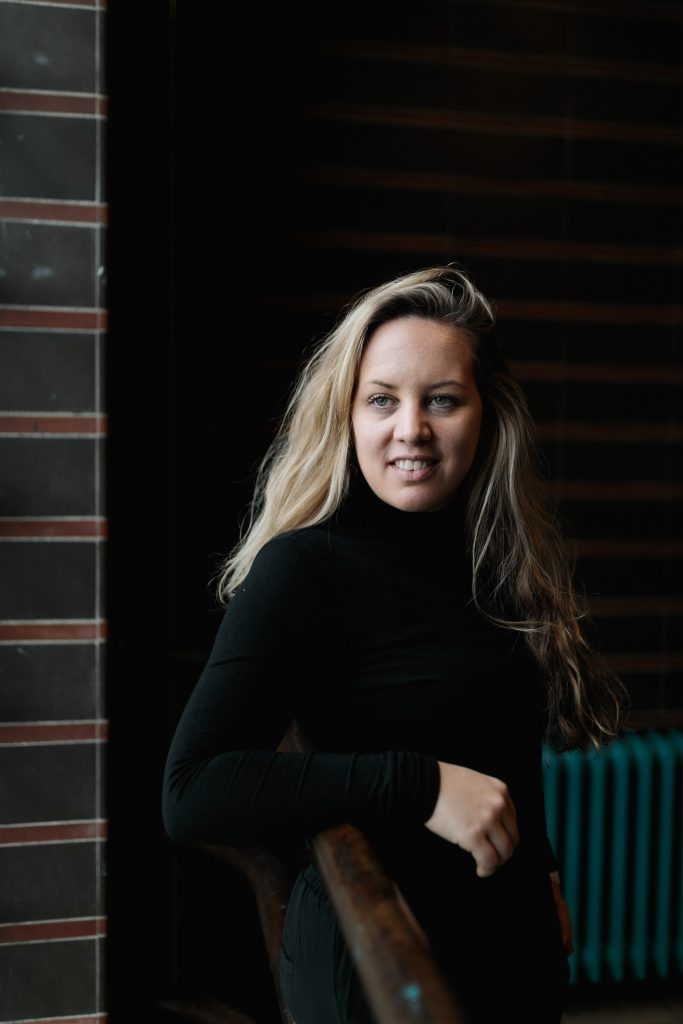
Photography by Florian Voggeneder
To read my other Blog Posts follow the links:
Blog Post #1 Digital Vogue – from 2D to 3D
Blog Post #3 Digital Vogue – Destinations within Re-Fream