Fashion manufactured by rain. The poetics of this novel design approach by Dutch designer Jef Montes is so captivating, that it is easy to miss his reinvention of the fashion system. While his Re-FREAM research started as a fashion collection, the process propelled Montes towards the development of a new fashion business model. The resulting Adaptive Archi-Filament radically redefines entrepreneurial strategy for fashion designers. Rather than simply using fibers to produce fashion, his signature creative filaments both shape and financially sustain his creative collections, becoming the foundation for his brand.
His research flow began with the aquatic interplay of the “Marinero” fashion collection. Rather than using traditional pattern-making, the goal was to create woven and knitted garments with 2D fabrics which re-configure into 3D shapes through their interaction with water. Underwater experiments and tests with soluble yarns gave way to rain interaction experiments, as well as sweat testing.
Through the close collaboration with the Re-FREAM hubs, Montes gained a new understanding of the process of creating yarns. “Aitex was like a kindergarten playground for me”, Montes recalls, “there are so many ways to produce a filament or a yarn. It was amazing for me to collaborate with all the technicians and the chemists, to understand a multifilament works! Or where do the polymers come from? As I became more open-minded, it went from macro to micro, and became yarn innovation”. These exchanges re-oriented the founder and creative director of Studio Adaptive Skins towards textile architecture.
His final presentation demonstrates co-creation with rainy weather. 42 garment designs were exposed to rain in a dramatic roof installation over 30 days, showcasing and documenting the potential of manufacturing with the new hydro-responsive yarns. Meteorological conditions generated dynamic shapes. In the course of this design process, the Adaptive Archi-filament evolved into the resolution for a major fashion design challenge: creating commercially viable signature pieces without compromising design integrity.
Co-designing with nature means lowering energy consumption and waste. Montes re-situates the slowness of these natural processes into the field of the sublime. Deeply rooted in Conditional Design, the garments were given shape and evolve through the chance and rhythms of drizzle and downpours, or transpiration. The garments embody environmental consciousness, aesthetically drawing attention to the poetics of nature
The generative framework of Montes’s designs produces no waste. As water is an overarching theme and a precious resource, materials found within the sea were also used to create garment structures. Testing included recycled sea-plastics interwoven with sea-weed based threads (horizontal versus vertical).
Producing filament prototypes of his concept in both Spain and Austria, Montes was able to work with two different teams and outcomes. In addition, the testing provided by the EMPA lab allowed a comparison of the – more uniform – impact of weather on the textiles to the impact – more localized – sweat interaction. The collaborations allowed for not only material innovation, but also a vast collection of data on all the parameters of the filaments and their qualities, as well as a potential application analysis.
By reorienting his research, the call also allowed him to restructure his vision of design entrepreneurship. The research journey will be presented in the ‘Makers Secrets’ at the Dutch national TextielMuseum Tilburg, starting 26th of June 2021 until the 8th of May 2022. During London Fashion Week, Montes collaborated with Fashion Scout, for a digital presentation of project Marinero.
In 2022, as part of the commercial development of the project, Montes will showcase the filament prototype available for order at the Frankfurt TechTextil Fair. Intrigued by the materials’ responsiveness to the human body, Montes aims to continue collaborations with his research partners to investigate the interplay of textile architectures with their surroundings – including the experiences of light, sound and climate. A shift from rainwater to seawater experimentation is another key goal.
Yet the work reaches far beyond material innovation as a source for composing aesthetically sensational fashion. Intertwining his fashion expertise with that of technicians, scientists and industry experts, the project evolved from adaptive garments which morph through the weather into rethinking fashion entrepreneurship. Not just responsive filaments, but also frameworks, supply chains, and design processes which incorporate transition and new forms of interdisciplinary interplay. Adaptive manufacturing which responds to both humans and the environment.
The Project
Inspired by the contrast of the sea and plastic pollution, Marinero is the first project of Studio Adaptive Skins. The focus of Marinero is to create an architectural blueprint that transforms organically over the course of time due to different meteorological conditions.
The Partners
Jef Montes worked within the Sustainable Finishing Hub of Re-FREAM with Aitex, Wood K plus/ Johannes Kepler University and the Fashion & Technology department of the Ufg in Linz, as well as Empa, Haratech, TextielLab Tilburg
Patricia Moñino, Aitex, about the project
“Jef Montes’ project, Marinero, is the most conceptual art project that came to the Sustainable Finishing Hub. He is a dreamer – and he imagined a new mindset regarding filaments. The Archifilament was developed in parallel, with different techniques, in Aitex and Haratech (and validated by EMPA), with the aim of creating a flexible yarn that may be modified through the temperature and humidity of the environment.
The project ended up with successful results. In fact, he is about to launch his first commercial production from the Aitex Archifilament development. The Archifilament was tailored by the weather, showing beautiful shapes, made by the wind, the rain, and the sun. Sometimes, dreams come true.”
The Technologies
First trials at Haratech tested 3D printing of recycled ocean plastics into moving spiral adaptive filament, with a coating filler of silicon. It became the 3D printed prototype for the layered multifilament yarn for the Johannes Kepler University and Wood K plus, which allowed the development of one type of filament production.
In parallel at Aitex in Alcoy, the team used the core of Elastan, and then twisted absorbent multi-filaments around it. Three different types of mechanical yarns were twisted, and then dipped in a soluble polyvinyl alcohol coating, resulting in a raffia-like texture when dry. The thickest variation of the Adaptive Archi-Filament, it displayed the best absorption quality.
Montes made first knitting tests with these yarns on the industrial Italian knitting machines at the Ufg fashion department, which he continued at the TextielLab Tilburg. A total of 42 woven and knitted garment versions were produced and experimented upon. They combined Aitex Archi-Filament,
Wood K Plus textured and melt-coated filaments, soluble yarns, Rpet yarns, monofilaments, and Seacell yarns dyed with seaweed pigments. In addition, testing by the Empa Swiss Federal Laboratories for Materials Science and Technology analyzed how the garments were transformed by sweat, allowing for a new alternative to the “tailored by weather” experiments: tailored by the user’s bodies.
The Artist
Jef Montes: “To describe my artistic process will be that its an ongoing process. Studio Adaptive Skins is a textile architecture studio based in Arnhem with a strong focus on responsive materials. A new approach on creating shape within the materials rather than cutting patterns out of 2D fabric. The materials are applied on the human skin but also connected to the structure of a building and interior. Responsive to the human and its surrounding the textiles improve the function and experience of: body, light, energy, areas, acoustics and climate.
I have been working as a fashion designer since 2012. After graduating for my Bachelor degree at the institute of the arts Arnhem I started working on fabric projects. As a designer I felt the need to make my own fabrics to create the ideas that I had in my mind. In the beginning it started as a creative process capturing my own signature. But afterwards I started to react on what I experienced as a designer. The first project that I did was Illuminosa. Within this project I focused on upcycled fiberglass materials made from my own studio. During the presentation I noticed that I wanted the materials to react on that moment rather than just showing of the clothing. So capturing the process was more important. With support from Creative Industries Fund NL Montes I was able to research architectural materials, using professional weaving machines. Creating luxurious fabrics by using waste materials. The second project Velero was designed and developed in collaboration with TextileLab Tilburg. This project was based on my passion and personal connection with the maritime world. The third project Tormenta reflects a Storm around the body and consists of 6 nylon material categories that were recycled from fishing nets. For my international debut I did a crowdfunding campaign to be able to finance my international team. After my Paris presentation I was selected for 33rd Hyères award 2018. This was a very key moment for me to present my vision to international professionals. This chance helped me to make the next step. I got inspired and started Studio Adaptive Skins with a new future focus and vision in mind.”
Follow Jef
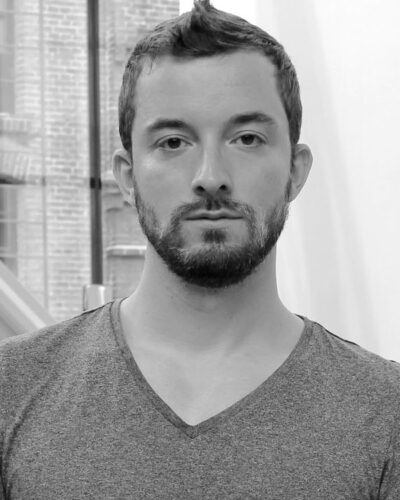