What is “Re-FREAM”?
Re-FREAM was a collaborative research project implemented between 2019 to 2021 where selected artists and designers teamed up with a community of scientists to rethink the manufacturing process of the fashion industry.
It’s a pillar of the STARTS Programme (Science + Technology + Arts), an initiative of the European Commission under the Horizon 2020 research and innovation programme. Awarded artists of the two rounds received a grant of 55,000 Euros.
Over a nine-month period, these hybrid teams embarked on a co-research and co-creation journey guided by a specific art/tech collaboration methodology in which they employed some of the most powerful technologies from some of the world’s most cutting-edge labs.
With a focus on the future of urban manufacturing of fashion, the research was carried out at three different European scientific hubs (Berlin, Linz, Valencia). Each hub was dedicated to one area of research: additive manufacturing, smart textiles and sustainable finishing. We called them challenges.
In our co-creation spaces we provided access to technologies (LINK zu Resources/technologies) such as 3D printing (PolyJet), micro-nebulization, ozone or calendering technology, laser cutting, injection-molding etc.
All research results, co-creation processes and the technological tool box were being shared openly to build up a self-running and sustainable innovation community with artists and technologists.
The goal was to develop new concepts for the future of fashion by means of new processes and aesthetics that are inclusive and sustainable. 20 projects accepted the challenge and contributed valuable ideas and concepts – all of them thinking ahead about the future of fashion and materials.
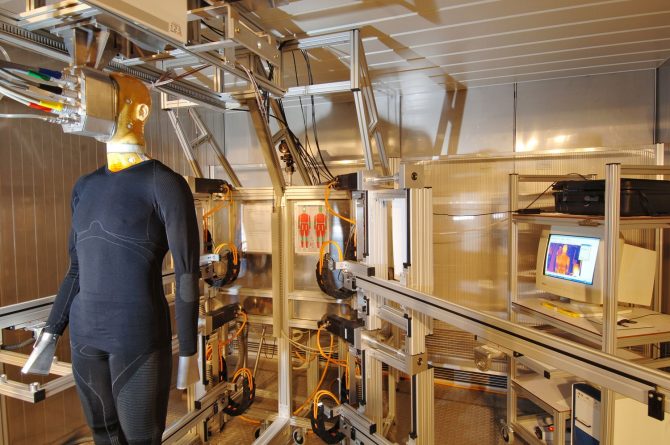
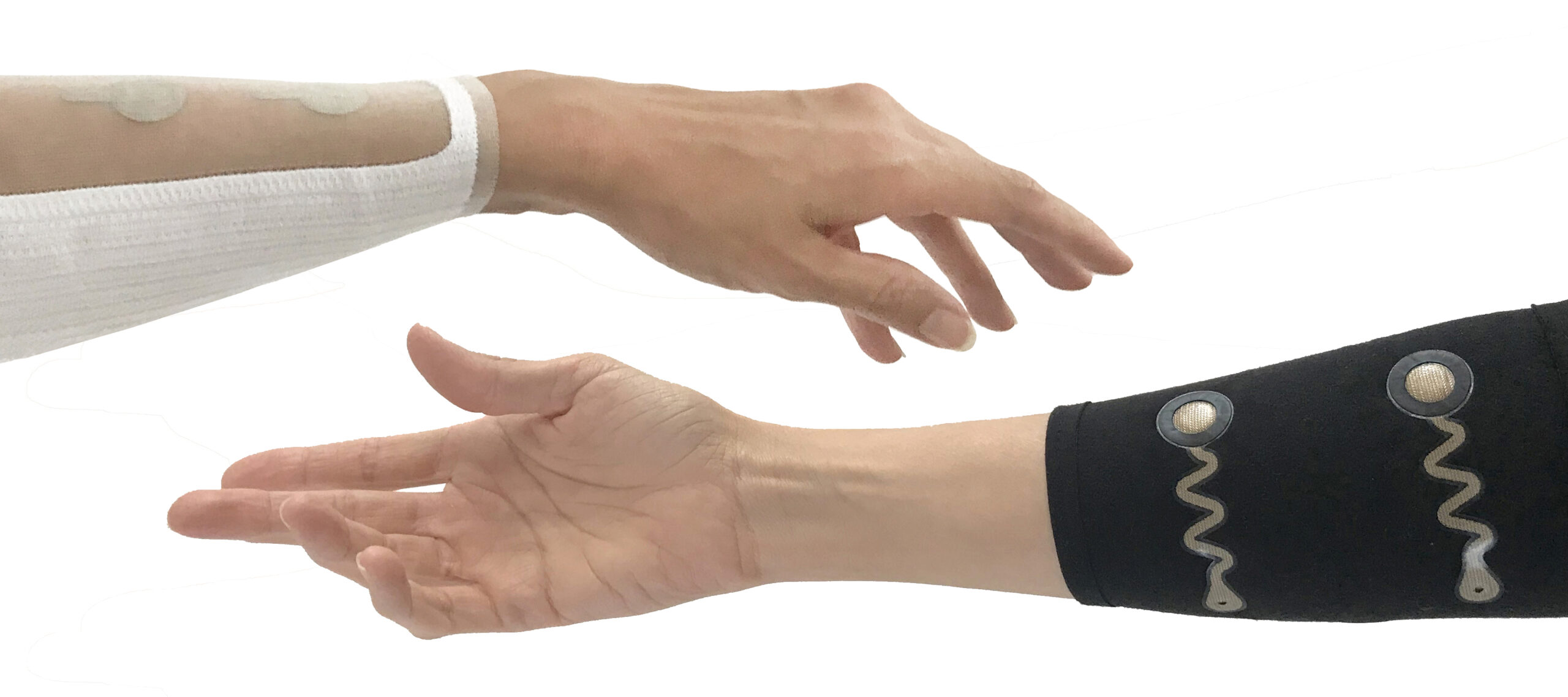
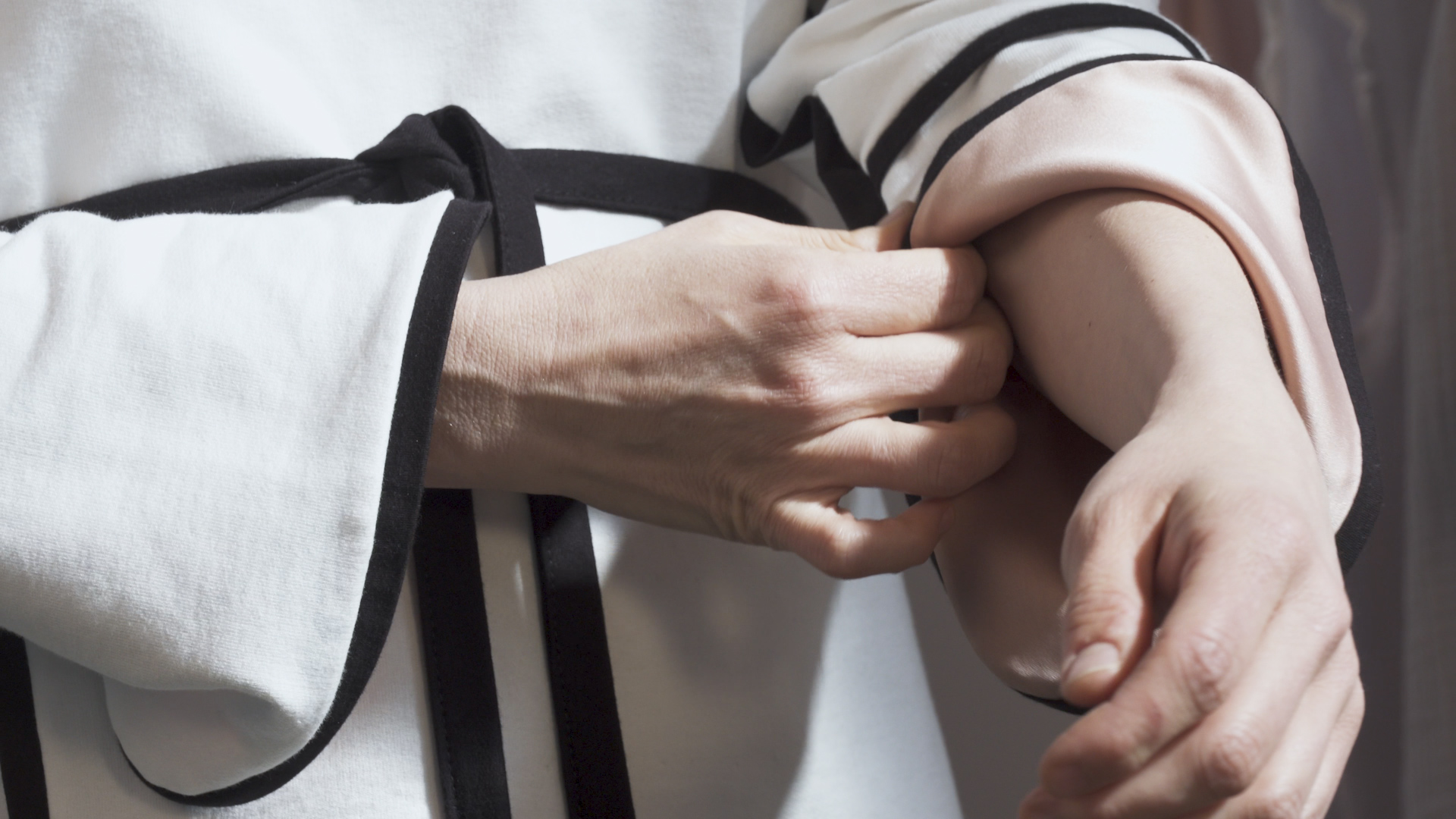
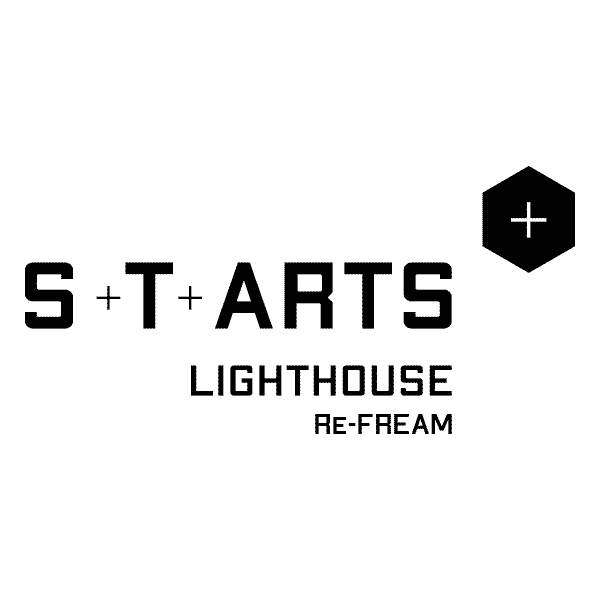
Re-FREAM’s mission
FREAM is a term, established in the US in the 1950ies. It was used for a group of people who began to rebel against the norm. In 1997, Steve Jobs Apple Computers picked up the term in his famous tv-commercial to talk about the crazy ones, the geniuses, those who are the real shapers of a future world. Today, misfits and rebels have become rare, and where the world has turned, we miss you like crazy.
Re-FREAM supported art-driven innovation in European R&I projects by incorporating artists into scientific research teams with strong support from art-related partners like the Art University of Linz (UFG) and the European Institute of Design (IED).
This STARTS lighthouse pilot for “art-inspired urban manufacturing” engaged industry, technology, end-users, and artists in a broad artistic exploration of technologies with the aim of creating novel products, processes and services that respond better to human needs. In a co-creation process of arts and technology, it was validated, how digitalized manufacturing of fashion can enable small-scale production of fashion in an urban environment.
The digital technologies that are transforming the fashion industry exemplify the changes impacting businesses and industries across the world. The mega trends in technology directly affect the creation, production, distribution/sale, and presentation of fashion to consumers; technology is finally set to disrupt fashion at every stage of the product lifecycle. Besides technology, a “new aesthetic” will influence the fashion of the future.
The latest manufacturing technologies are currently changing not only fashion itself, but also design and production methods. Technological advances are about to change processes in development, material design, production and several other fields within this industry.
Re-FREAM’s topics
The focus of the research lied on the FUTURE URBAN MANUFACTURING OF FASHION by using additive manufacturing, smart textiles and sustainable finishing together with social and environmental values to create a new value chain for the fashion industry. The goal was to put more emphasis on these two trends:
Small Scale Production
Additionally apparel manufacturing will not only be about simply making physical products. It will also cater to the fundamental shift of economics of production through customizations and customer-demand personalization.
Customization
Additionally apparel manufacturing will not only be about simply making physical products. It will also cater to the fundamental shift of economics of production through customizations and customer-demand personalization.
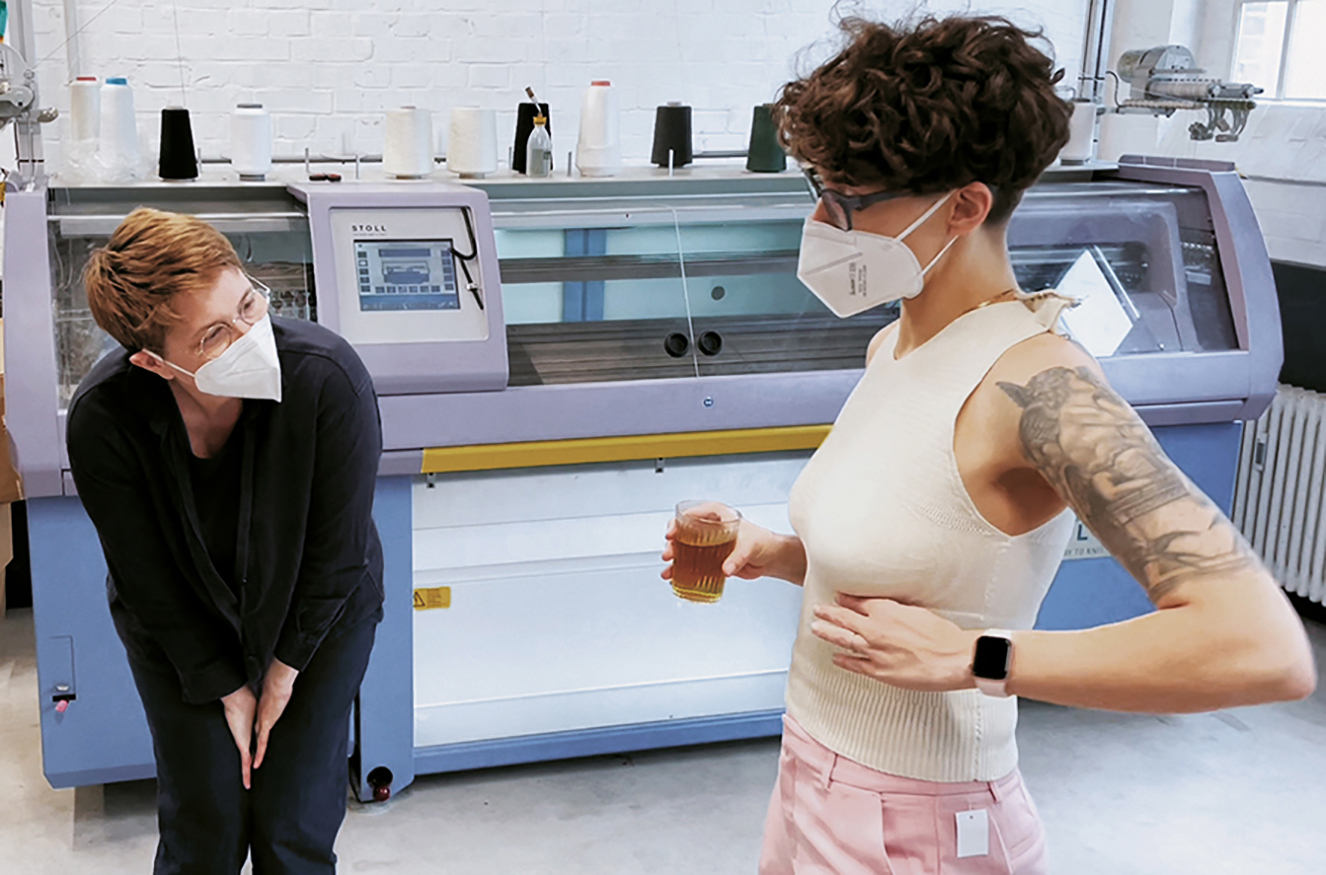
Re-FREAM’s research challenges
The research in both rounds was carried out at three different European scientific hubs (Berlin, Linz, Valencia). Each hub was dedicated to one of these areas of research – we called them challenges.
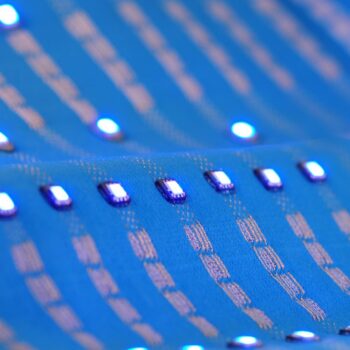
From analog to connected
The integration of electronics into textiles enables new potentials of how we communicate in the future with each other in the post-smartphone era and to find new ways of interaction between the human body and its environment.
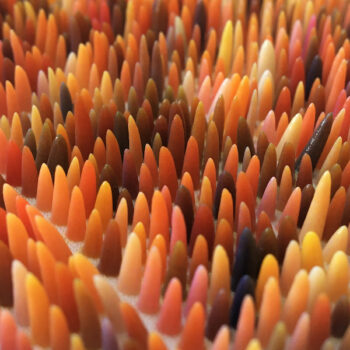
From 2D to 3D
Traditionally, the predominant use of textiles as fashion materials has led to the development of 2D pattern-making methods for dressing the complex shape of the three-dimensional human body. Nowadays, digital design tools allow us to easily design and 3D print complex shapes for the human body.
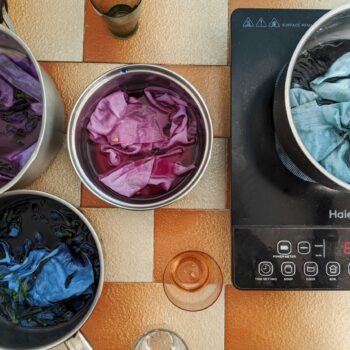
From linear to sustainable circular systems
Nature works in cycles - nothing is wasted, everything is reused. In contrast, the textile industry operates in a linear way, leading to extreme wastefulness and pollution.